Shandong Qilu lndustrial Co.,Ltd.
Why Forged Steel Flanges Are Essential for High-Pressure Environments
Welcome to My Blog!
Before we dive into the content, I’d love for you to join me on my social media platforms where I share more insights, engage with the community, and post updates. Here’s how you can connect with me:
Facebook:https://www.facebook.com/profile.php?id=100090903441806
Now, let’s get started on our journey together. I hope you find the content here insightful, engaging, and valuable.
Introduction
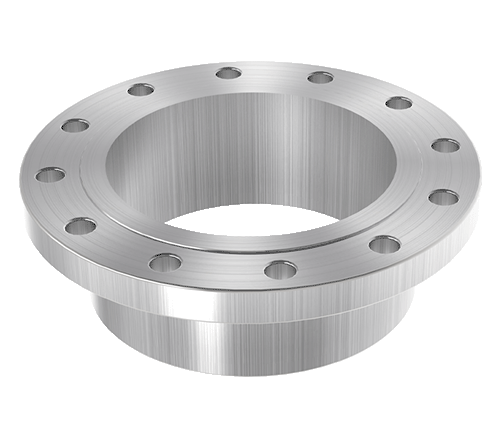
In industrial applications where high pressure and demanding conditions are the norm, the choice of materials and components becomes crucial. Forged steel flanges stand out as a key component in these environments due to their superior strength and reliability. This article explores why forged steel flanges are essential for high-pressure environments, their advantages, applications, and best practices for their use.
Understanding Forged Steel Flanges
Forged steel flanges are critical components used to connect pipes, valves, pumps, and other equipment in high-pressure systems. Unlike cast or welded flanges, forged flanges are made by deforming steel under high pressure, which imparts superior mechanical properties and enhances their performance under extreme conditions.
What Are Forged Steel Flanges?
Forged steel flange are manufactured through a forging process, where steel is heated to a high temperature and then shaped by applying compressive forces. This process aligns the steel’s grain structure, resulting in a stronger and more durable flange compared to those made by casting.
Types of Forged Steel Flanges
There are several types of forged steel flange, each designed for specific applications:
- Slip-On Flanges: These flanges slide over the pipe and are welded in place. They are easy to align and install.
- Weld Neck Flanges: These flanges are welded to the pipe, providing a strong and durable connection. They are often used in high-pressure applications.
- Blind Flanges: Used to seal the end of a pipe or vessel, blind flanges are essential for maintenance and pressure testing.
- Socket Weld Flanges: These flanges have a socket where the pipe is inserted before welding. They are commonly used for small-diameter, high-pressure applications.
Why Forged Steel Flanges Are Preferred in High-Pressure Environments
Forged steel flanges are preferred in high-pressure environments for several compelling reasons. Understanding these benefits helps in appreciating their critical role in maintaining system integrity and safety.
Enhanced Strength and Durability
Forged steel flange are known for their exceptional strength and durability. The forging process eliminates internal defects and improves the steel’s grain structure, making the flanges more resistant to high pressures and harsh conditions.
Table: Mechanical Properties of Forged Steel vs. Cast Steel
Property | Forged Steel | Cast Steel |
---|---|---|
Tensile Strength | 600-900 MPa | 350-700 MPa |
Yield Strength | 450-750 MPa | 250-500 MPa |
Impact Toughness | High | Lower |
Ductility | High | Moderate |
Improved Resistance to Fatigue
In high-pressure environments, flanges are subjected to repeated stress cycles, which can lead to fatigue failure. Forged steel flanges have better fatigue resistance due to their refined grain structure, making them suitable for applications with cyclic loading.
Superior Leak Prevention
The tight tolerances and high-quality finish of forged steel flanges contribute to superior sealing performance. Properly installed forged flanges reduce the risk of leaks in high-pressure systems, ensuring system integrity and operational safety.
Higher Temperature Tolerance
Forged steel flange can withstand high temperatures better than many other types of flanges. This makes them ideal for applications involving high temperatures, such as in petrochemical plants or steam systems.
Better Resistance to Corrosion
Many forged steel flanges are treated or alloyed to enhance their resistance to corrosion. This is crucial in high-pressure environments where exposure to corrosive substances can lead to rapid deterioration of less durable materials.
Applications of Forged Steel Flanges
Forged steel flanges are used in various high-pressure applications across different industries. Their robustness and reliability make them a preferred choice in critical environments.
Oil and Gas Industry
In the oil and gas sector, forged steel flange are used in pipelines, drilling equipment, and pressure vessels. They ensure safe and reliable connections in high-pressure and high-temperature conditions.
Chemical Processing
Forged steel flange are employed in chemical processing plants where they handle corrosive substances under high pressure. Their durability and corrosion resistance are essential for maintaining safety and efficiency.
Power Generation
In power generation facilities, especially those dealing with steam, forged steel flanges are used in steam lines, turbines, and other high-pressure equipment. They help maintain the integrity of critical systems.
Marine Applications
Marine environments expose equipment to harsh conditions, including high pressures and corrosive seawater. Forged steel flange are used in marine applications for their strength and resistance to corrosion.
Best Practices for Using Forged Steel Flanges
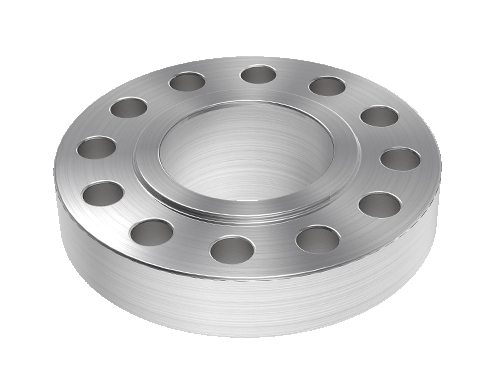
To ensure the optimal performance and longevity of forged steel flanges, follow these best practices:
Proper Installation
Ensure flanges are properly aligned and fitted before welding or bolting. Misalignment can lead to leaks or stress concentrations, which may cause failures.
Regular Maintenance
Inspect flanges regularly for signs of wear, corrosion, or damage. Routine maintenance helps prevent issues before they lead to more significant problems.
Correct Material Selection
Choose forged steel flange with appropriate material specifications based on the operating conditions, including pressure, temperature, and corrosive environment.
Use Quality Sealing Gaskets
Use high-quality gaskets that match the flange material and application requirements. Proper gasket selection and installation are crucial for leak prevention.
Follow Manufacturer Guidelines
Adhere to manufacturer guidelines for installation, maintenance, and operating limits. This ensures that the flanges perform as intended and comply with safety standards.
Conclusion
Forged steel flanges play a crucial role in maintaining the integrity and safety of high-pressure systems across various industries. Their superior strength, durability, and resistance to extreme conditions make them an essential component for ensuring reliable connections in demanding environments. By understanding the benefits and best practices associated with forged steel flanges, you can make informed decisions that enhance the performance and longevity of your high-pressure systems.
FAQ
What makes forged steel flanges stronger than cast steel flanges?
Forged steel flanges are stronger due to the forging process, which aligns the steel’s grain structure and eliminates internal defects. This results in higher tensile and yield strength compared to cast steel flanges.
Are forged steel flanges suitable for all high-pressure applications?
Forged steel flanges are suitable for most high-pressure applications, but it is essential to select the appropriate material and flange type based on specific operating conditions, such as pressure, temperature, and corrosiveness.
How do I choose the right forged steel flange for my application?
Consider factors such as the operating pressure, temperature, and environmental conditions. Consult with a flange manufacturer or engineer to select a flange that meets your specific requirements.
Can forged steel flanges be used in corrosive environments?
Yes, many forged steel flanges are alloyed or treated to enhance their corrosion resistance. Ensure you choose a flange with suitable material specifications for corrosive environments.
What maintenance is required for forged steel flanges?
Regular inspection for signs of wear, corrosion, or damage is crucial. Additionally, ensure proper installation and alignment, and follow manufacturer guidelines for maintenance practices.