Shandong Qilu lndustrial Co.,Ltd.
What I Wish Everyone Knew About Upset Forging
Upset forging is a metalworking process that involves heating a metal bar and then applying pressure to the end of the bar to increase its diameter. This process is used to create a variety of components, including bolts, nuts, gears, and other machine parts.
In this blog post, I will discuss the basics of upset forging, including the process, the benefits, and the applications. I will also answer some common questions about upset forging.
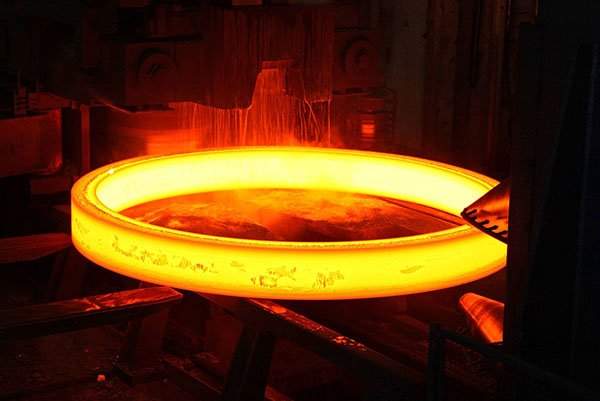
Introduction
Upset forging is a type of closed-die forging. In closed-die forging, the metal is completely enclosed in a die, which is a mold that defines the shape of the finished part.
The upset forging process begins with heating a metal bar to a specific temperature. The temperature is typically chosen to be within the recrystallization range of the metal, which is the range of temperatures at which the metal’s crystalline structure is reformed.
Once the metal is heated, it is placed in a die. The die has a cavity that is the desired shape of the finished part. A press or hammer is then used to apply pressure to the end of the bar.
The pressure forces the metal to flow into the cavity of the die. As the metal flows, it is compressed and deformed. This deformation increases the diameter of the end of the bar and creates the desired shape.
Benefits of Upset Forging
Upset forging offers a number of benefits over other manufacturing processes, including:
Strength: Upset forging produces parts with high strength and toughness. This is because the forging process works the metal, which helps to improve its mechanical properties.
Dimensional accuracy: Upset forging can produce parts with high dimensional accuracy. This is because the die defines the shape of the finished part.
Cost-effectiveness: Upset forging is a relatively cost-effective manufacturing process. This is because it can be used to produce a variety of parts in high volumes.
Applications of Upset Forging
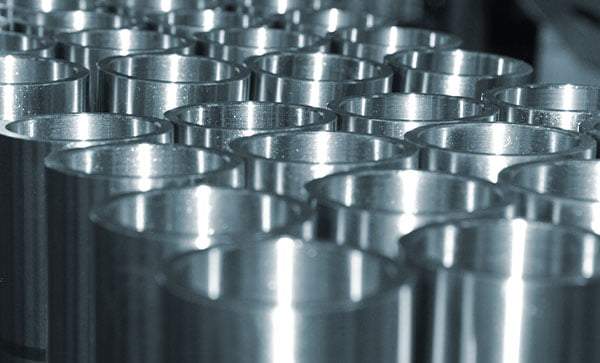
Upset forging is used to create a variety of components, including:
Bolts and nuts: Upset forging is a common process for producing bolts and nuts. This is because it can produce parts with high strength and dimensional accuracy.
Gears: Upset forging is also used to produce gears. This is because it can produce parts with complex shapes and high strength.
Other machine parts: Upset forging is also used to produce a variety of other machine parts, such as shafts, pins, and bushings.
FAQ
What are the different types of upset forging?
There are two main types of upset forging:
Incremental upsetting: In incremental upsetting, the metal is upset in a series of steps. This is done to prevent the metal from cracking.
Continuous upsetting: In continuous upsetting, the metal is upset in a single step. This process is faster than incremental upsetting, but it is also more likely to cause cracking.
What are the different types of dies used in upset forging?
There are two main types of dies used in upset forging:
Straight dies: Straight dies have a straight cavity that produces a cylindrical part.
Conical dies: Conical dies have a tapered cavity that produces a conical part.
What are the different types of presses used in upset forging?
Upset forging presses can be classified into two main types:
Hammer presses: Hammer presses use a hammer to apply pressure to the metal.
Piston presses: Piston presses use a piston to apply pressure to the metal.
Conclusion
Upset forging is a versatile manufacturing process that can be used to produce a variety of high-quality parts. It is a cost-effective process that can produce parts with high strength, dimensional accuracy, and complex shapes.
But the beauty of upset forging extends beyond its technical prowess. It’s a cost-effective dance, delivering exceptional value for every ounce of metal transformed. By minimizing material waste and maximizing production efficiency, it sculpts not just parts, but a path towards economic viability. In a world where every penny counts, this process ensures that strength, precision, and versatility come at a price that makes even the most discerning manufacturer smile.
Process | Strength | Dimensional Accuracy | Cost-Effectiveness |
---|---|---|---|
Upset Forging | High | High | Relatively cost-effective |
Casting | Medium | Low | Relatively cost-effective |
Machining | Low | High | Expensive |
Extrusion | Medium | High | Relatively cost-effective |
Stamping | Medium | Medium | Relatively cost-effective |