Shandong Qilu lndustrial Co.,Ltd.
Understanding the Forging Manufacturing Process Explained
Welcome to My Blog!
Before we dive into the content, I’d love for you to join me on my social media platforms where I share more insights, engage with the community, and post updates. Here’s how you can connect with me:
Facebook:https://www.facebook.com/profile.php?id=100090903441806
Now, let’s get started on our journey together. I hope you find the content here insightful, engaging, and valuable.
Introduction
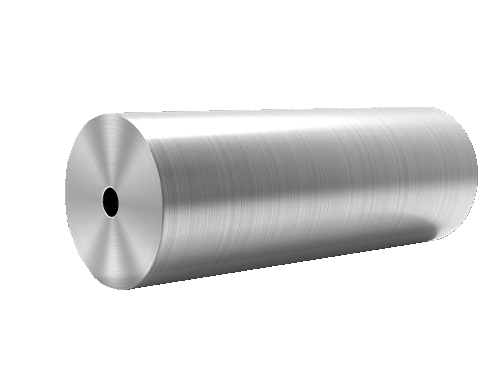
The forging manufacturing process is a crucial method in producing high-strength components used across various industries. This blog aims to delve into the intricacies of this process, discussing its methods, benefits, and applications.
What is the Forging Manufacturing Process?
The forging manufacturing process involves shaping metal using compressive forces. It can be performed hot, warm, or cold, depending on the material’s characteristics and the desired properties of the finished product.
Types of Forging Processes
Open-Die Forging
Open-die forging is characterized by the absence of a mold. Instead, the metal is deformed between two flat dies. This method is often used for large components, such as shafts and rings.
Closed-Die Forging
In closed-die forging, the metal is placed in a mold and shaped under high pressure. This allows for more complex shapes and better dimensional accuracy.
Impression Die Forging
Impression die forging combines elements of both open and closed-die methods. It uses dies that contain a cavity to produce intricate shapes.
Forging Type | Characteristics | Applications |
---|---|---|
Open-Die | No mold, large shapes | Shafts, rings |
Closed-Die | Molded, complex shapes | Gears, automotive parts |
Impression Die | Detailed, high precision | Aerospace components |
Benefits of the Forging Manufacturing Process
The forging manufacturing process offers several advantages, including:
- Strength: Forged parts exhibit superior mechanical properties.
- Consistency: The process ensures uniformity in dimensions.
- Reduced Waste: Forging typically produces less scrap compared to casting.
Applications of Forging Manufacturing Process
Forging is widely used in industries such as automotive, aerospace, and oil and gas. Components like crankshafts, gears, and turbine blades are commonly produced using this method.
Recent advancements in forging technology, such as computer numerical control (CNC) and additive manufacturing, enhance precision and efficiency, enabling the production of even more advanced materials and designs. As industries evolve, forging’s role will likely expand, contributing to innovations in manufacturing and application, ultimately shaping the future of these critical fields.
Common Challenges in Forging
While the forging manufacturing process has numerous benefits, it also presents challenges:
- Certainly, here’s a concise version of the challenges associated with the forging manufacturing process:
- Material Limitations: Forging is not suitable for all materials; it requires ductile metals that can withstand high pressures without cracking.
- Cost: High initial setup costs are associated with forging, particularly for complex dies, which can be a barrier for small-scale production.
- Tooling Complexity: The design and manufacture of forging dies are intricate and require skilled labor, which can lead to increased costs and potential delays.
- Scale of Production: Forging may not be cost-effective for low-volume production due to the high fixed costs of tooling and equipment.
- Skilled Labor: The process demands skilled operators for machinery operation and quality control, which can be challenging to find and train.
- Energy Consumption: Forging is energy-intensive, leading to higher operational costs and environmental impacts.
- Post-Forging Processing: Additional steps like trimming or heat treatment may be needed after forging, adding to the overall manufacturing cost and complexity.
Conclusion
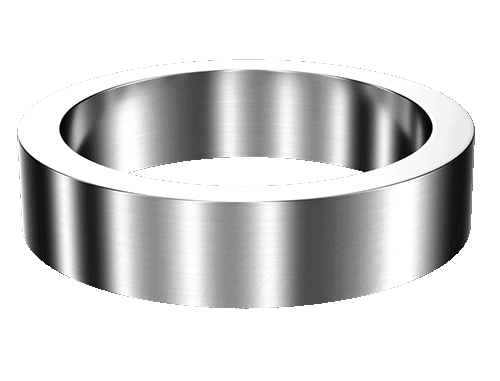
Understanding the forging manufacturing process is essential for anyone involved in manufacturing or engineering. With its unique advantages and diverse applications, forging remains a vital technique in producing high-quality components.
FAQ
What materials can be forged?
Common materials include steel, aluminum, and titanium.
How does forging compare to casting?
Forging generally results in stronger parts with fewer defects compared to casting.
What industries benefit from forging?
Industries such as automotive, aerospace, and construction extensively utilize forging.
This overview provides a solid foundation for understanding the forging manufacturing process. If you’d like to delve deeper into any specific aspect, feel free to ask!