Shandong Qilu lndustrial Co.,Ltd.
Understanding the Different Types of Steel Flanges and Their Uses
Introduction
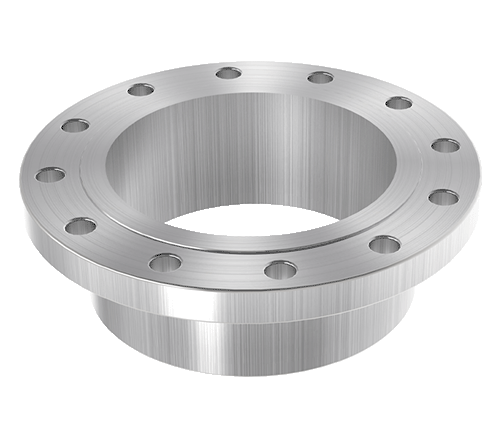
Steel flanges are essential components in a wide range of industrial applications, providing a means to connect pipes, valves, pumps, and other equipment. They come in various types, each designed for specific functions and requirements. Understanding the different types of steel flanges and their uses can help you make informed decisions for your projects, ensuring reliability and efficiency in your piping systems. This blog will explore the various types of steel flanges, their applications, and best practices for choosing the right flange for your needs.
What Are Steel Flanges?
Steel flanges are mechanical components used to join pipes, valves, and other equipment in a piping system. They provide a strong, secure connection and are typically attached using bolts and gaskets. Steel flanges come in various designs and specifications to accommodate different pressures, temperatures, and types of connections.
Types of Steel Flanges
Steel flanges are categorized based on their design, pressure rating, and application. The primary types include:
- Slip-On Flanges: Slide over the pipe and are welded both inside and outside.
- Weld Neck Flanges: Have a tapered hub that is welded to the pipe, providing a strong connection.
- Blind Flanges: Used to seal the end of a pipe or flange connection.
- Socket Weld Flanges: Designed for small-diameter, high-pressure applications with a socket weld connection.
- Threaded Flanges: Have internal threads and are screwed onto the pipe.
- Lap Joint Flanges: Used with a backing ring and are ideal for applications requiring frequent dismantling.
Common Applications for Steel Flanges
Steel flanges are used in various industries and applications, each requiring specific types of flanges based on factors such as pressure, temperature, and fluid type. Here’s a look at some common applications:
Oil and Gas Industry
In the oil and gas industry, steel flanges are used to connect pipelines, valves, and other equipment. High-pressure and high-temperature flanges, such as weld neck flanges, are often used to ensure reliable and safe connections in harsh environments.
Chemical and Petrochemical Plants
Chemical and petrochemical plants use steel flanges to handle corrosive and high-temperature fluids. Flanges such as slip-on and socket weld flanges are commonly employed for their ease of installation and ability to handle high-pressure conditions.
Power Generation
In power generation facilities, steel flanges are used in steam and water systems. Weld neck flanges are often used in these applications due to their strength and ability to withstand high pressures and temperatures.
Water and Wastewater Treatment
Water and wastewater treatment plants use various types of steel flanges to connect pipes and equipment. Blind flanges are commonly used to seal off pipelines or equipment during maintenance.
Key Features and Specifications of Steel Flanges
When selecting steel flanges, it’s essential to consider their key features and specifications. Here’s a table outlining some important aspects:
Feature | Description |
---|---|
Material | Common materials include carbon steel, stainless steel, and alloy steel. |
Pressure Rating | Flanges are rated for different pressure classes, such as ANSI 150, 300, 600, etc. |
Temperature Rating | Flanges are rated for various temperature ranges depending on the material. |
Dimensions | Standard dimensions are specified by standards such as ASME B16.5 and DIN. |
Finish | Flanges may have different finishes, including raised face, flat face, or ring-type joint. |
Connection Type | Includes slip-on, weld neck, blind, socket weld, threaded, and lap joint. |
Bolt Pattern | The number and size of bolt holes, which affect the flange’s ability to handle pressure. |
How to Choose the Right Steel Flange
Choosing the right steel flange involves considering several factors to ensure compatibility and performance in your piping system. Here’s how to make an informed decision:
Determine the Application Requirements
Consider the specific requirements of your application, including pressure, temperature, and fluid type. Different flanges are designed to handle various conditions, so it’s crucial to match the flange to your system’s needs.
Select the Appropriate Material
The material of the flange should be compatible with the fluid being transported and the environmental conditions. Carbon steel is commonly used for general applications, while stainless steel is preferred for corrosive environments.
Consider the Flange Design
Choose the flange design that best suits your installation requirements. For example, weld neck flanges provide a strong connection for high-pressure applications, while slip-on flanges offer ease of installation for lower-pressure systems.
Review Standards and Specifications
Ensure that the flange you choose meets the relevant industry standards and specifications, such as ASME, ANSI, or DIN. This ensures compatibility with other components and compliance with safety regulations.
Installation and Maintenance of Steel Flanges
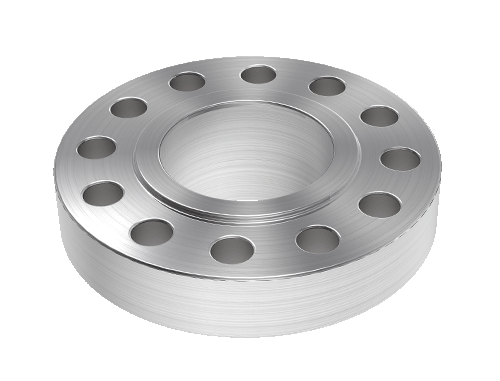
Proper installation and maintenance of steel flanges are essential for ensuring their performance and longevity. Follow these best practices:
Proper Installation
- Preparation: Clean the flange surfaces and check for damage or defects.
- Alignment: Ensure proper alignment of the flanges before bolting.
- Gaskets: Use appropriate gaskets to create a secure seal and prevent leaks.
- Bolting: Tighten bolts evenly and to the specified torque to ensure a secure connection.
Regular Maintenance
- Inspection: Regularly inspect flanges for signs of wear, corrosion, or leakage.
- Cleaning: Clean flanges as needed to remove debris and prevent contamination.
- Replacement: Replace damaged or worn flanges to maintain system integrity and prevent failures.
Troubleshooting Common Issues
- Leaks: Address leaks by checking gasket integrity and bolt tightness.
- Corrosion: Treat or replace corroded flanges to prevent further damage.
- Alignment Issues: Correct any misalignment to ensure proper function and avoid stress on the system.
Conclusion
Steel flanges play a critical role in connecting and securing components within a piping system. Understanding the different types of steel flanges, their features, and their applications is essential for making informed decisions and ensuring the reliability and efficiency of your piping systems. By considering factors such as material, pressure rating, and flange design, you can select the right flange for your needs and ensure proper installation and maintenance. Whether you’re working in oil and gas, chemical processing, power generation, or water treatment, choosing the appropriate steel flange is key to achieving optimal performance and safety in your operations.
FAQ
Q:What is the difference between a slip-on flange and a weld neck flange?
A:Slip-on flanges are designed to slide over the pipe and are welded both inside and outside. Weld neck flanges have a tapered hub and are welded to the pipe, providing a stronger and more reliable connection, particularly in high-pressure applications.
Q:What materials are commonly used for steel flanges?
A:Common materials for steel flanges include carbon steel, stainless steel, and alloy steel. The choice of material depends on the application requirements, such as the type of fluid being transported and environmental conditions.
Q:How do I determine the pressure rating of a flange?
A:The pressure rating of a flange is determined by its design and material. Flanges are rated according to standards such as ANSI, which specify pressure classes such as 150, 300, 600, and higher. Check the flange specifications to match the pressure rating with your system’s requirements.
Q:Can I use a threaded flange in high-pressure applications?
A:Threaded flanges are generally not recommended for high-pressure applications due to their lower strength compared to weld neck or slip-on flanges. For high-pressure systems, it is better to use flanges designed for such conditions, such as weld neck flanges.
Q:How often should steel flanges be inspected and maintained?
A:Steel flanges should be inspected regularly, typically as part of routine maintenance checks. The frequency of inspections depends on the operating conditions and the criticality of the application. Regular inspections help identify issues early and prevent system failures.