Shandong Qilu lndustrial Co.,Ltd.
Understanding Open Die Forging: Key Benefits and Techniques
Welcome to My Blog!
Before we dive into the content, I’d love for you to join me on my social media platforms where I share more insights, engage with the community, and post updates. Here’s how you can connect with me:
Facebook:https://www.facebook.com/profile.php?id=100090903441806
Now, let’s get started on our journey together. I hope you find the content here insightful, engaging, and valuable.
Introduction
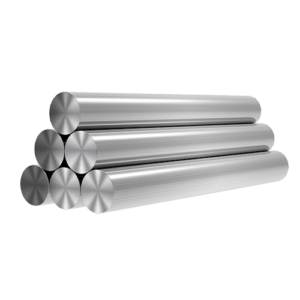
Open die forging is a widely used manufacturing process that shapes metal into desired forms through the application of compressive forces. This method is known for producing high-quality components, offering various benefits over other forging techniques. In this blog post, we will delve into the key benefits and techniques of open die forging, exploring its applications and answering common questions surrounding the process.
What Is Open Die Forging?
Open die forging, also known as free forging, involves placing a heated metal workpiece between two flat dies. Unlike closed die forging, which uses shaped dies to create specific forms, open die forging allows for more flexibility in shaping the material. The dies do not completely enclose the workpiece, enabling it to be manipulated into various shapes through repeated hammering or pressing.
Key Techniques in Open Die Forging
Heating the Metal
Before forging, the metal is heated to a specific temperature, making it malleable and easier to shape. The heating process is crucial as it affects the material’s properties and workability.
Application of Force
In open die forging, force is applied through mechanical or hydraulic hammers or presses. The choice of equipment depends on the size and complexity of the part being forged.
Upsetting
Upsetting is a technique used to increase the thickness of the workpiece. This is achieved by compressing the material along its length, allowing for better material distribution during shaping.
Stretching
Stretching involves elongating the workpiece to achieve the desired dimensions. This technique is often used in conjunction with other processes to refine the final shape.
Shaping
The shaping phase consists of repeatedly hammering or pressing the workpiece to achieve the required form. This phase can involve various motions, including radial and axial movements.
Benefits of Open Die Forging
Cost-Effectiveness
One of the main advantages of open die forging is its cost-effectiveness. The initial investment in tooling is lower than that for closed die forging, making it an attractive option for producing large or simple components.
Material Efficiency
Open die forging allows for better material utilization, as excess material can be trimmed away after the forging process. This reduces waste and contributes to more sustainable manufacturing practices.
Superior Mechanical Properties
The process of open die forging enhances the mechanical properties of the material. The compressive forces align the grain structure, resulting in improved strength and durability.
Flexibility in Design
Open die forging offers greater design flexibility, enabling manufacturers to create complex shapes without the limitations of closed die systems. This adaptability makes it suitable for custom applications.
Applications of Open Die Forging
Aerospace Industry
In the aerospace sector, open die forging is utilized to produce critical components such as landing gear, shafts, and rings. The high strength and reliability of forged parts are essential in this industry.
Oil and Gas
Open die forging is widely used in the oil and gas industry to create large flanges, valves, and connectors that must withstand extreme pressures and temperatures.
Construction Equipment
Manufacturers of construction equipment rely on open die forging for producing components like frames, pins, and connectors. The durability of forged parts is vital in heavy-duty applications.
Automotive Sector
In automotive manufacturing, open die forging is used to create parts such as crankshafts and axles, which require high strength and performance.
Table: Key Characteristics of Open Die Forging
Characteristic | Description |
---|---|
Flexibility | Allows for custom shapes and sizes |
Material Types | Suitable for various metals, including steel and aluminum |
Tooling Costs | Lower initial investment compared to closed die forging |
Production Volume | Ideal for low to medium production volumes |
Mechanical Properties | Enhances strength and fatigue resistance |
Conclusion

Open die forging is a vital manufacturing process that offers numerous advantages, including cost-effectiveness, flexibility, and superior mechanical properties. Its applications across various industries highlight its importance in producing high-quality components. As technology advances, open die forging will continue to evolve, providing manufacturers with innovative solutions for their forging needs. Understanding the key benefits and techniques of open die forging empowers businesses to make informed decisions about their manufacturing processes, ensuring the production of reliable and durable components.
FAQ
What materials can be used in open die forging?
Open die forging is compatible with a wide range of materials, including carbon steel, alloy steel, stainless steel, and aluminum.
How does open die forging compare to closed die forging?
Open die forging offers more flexibility and lower tooling costs but may not achieve the same level of precision as closed die forging.
Can open die forging be automated?
Yes, open die forging can be automated using hydraulic presses and programmable hammers to enhance efficiency and consistency.
What are the limitations of open die forging?
While it is flexible, open die forging may not be suitable for highly intricate designs that require tight tolerances.