Shandong Qilu lndustrial Co.,Ltd.
Understanding Alloy Forged: Benefits and Applications
Welcome to My Blog!
Before we dive into the content, I’d love for you to join me on my social media platforms where I share more insights, engage with the community, and post updates. Here’s how you can connect with me:
Facebook:https://www.facebook.com/profile.php?id=100090903441806
Now, let’s get started on our journey together. I hope you find the content here insightful, engaging, and valuable.
Introduction
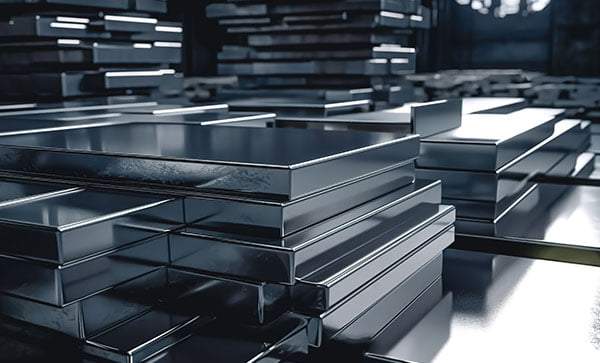
Alloy forged components are an integral part of various industries, offering enhanced strength, durability, and resistance to extreme conditions. The process of forging involves shaping metal through compressive forces, resulting in superior structural integrity compared to other manufacturing methods. In this blog, we will explore the benefits of alloy forged materials, their diverse applications, and the factors that contribute to their effectiveness.
What is Alloy Forging?
Definition and Process
Alloy forged materials are created by combining different metals to achieve specific properties, then subjecting them to high temperatures and pressure to create desired shapes. The forging process can be classified into two main types:
- Open Die Forging: Involves shaping the metal without confinement, allowing for a variety of shapes.
- Closed Die Forging: Involves shaping metal within a mold, providing more precise dimensions.
This method enhances the grain structure of the metal, resulting in superior mechanical properties.
Common Alloys Used in Forging
Various alloys are commonly used in forging processes, each chosen for its unique properties. Some of the most prevalent include:
- Steel Alloys: Known for their strength and versatility.
- Aluminum Alloys: Lightweight and corrosion-resistant.
- Titanium Alloys: Excellent strength-to-weight ratio and corrosion resistance.
- Nickel Alloys: High-temperature resistance and durability.
Understanding these alloys’ characteristics is essential when selecting the right materials for specific applications.
Benefits of Alloy Forged Components
Enhanced Strength and Durability
One of the primary advantages of alloy forged components is their enhanced strength and durability. The forging process aligns the grain structure of the metal, resulting in improved mechanical properties. This makes forged parts less prone to failure under stress, ideal for demanding applications.
Superior Resistance to Fatigue
Forged alloys exhibit superior resistance to fatigue compared to cast or machined components. The homogeneous grain structure helps distribute stresses evenly, reducing the likelihood of cracks and fatigue failure. This characteristic is particularly important in industries such as aerospace and automotive, where safety is paramount.
Improved Machinability
Alloy forged materials often have better machinability than other materials. The uniform structure created during forging allows for easier cutting and shaping, which can reduce manufacturing times and costs. This is beneficial for manufacturers looking to optimize production efficiency.
Cost-Effectiveness
While the initial cost of alloy forged components may be higher than other manufacturing methods, their long-term benefits often outweigh the costs. The durability and longevity of forged parts can lead to lower maintenance and replacement costs, making them a more economical choice over time.
Versatility in Applications
The versatility of alloy forged components makes them suitable for a wide range of applications. From automotive parts to industrial machinery, these components can be tailored to meet specific requirements, providing solutions across various sectors.
Enhanced Corrosion Resistance
Certain alloys used in forging, such as stainless steel and aluminum alloys, provide excellent corrosion resistance. This characteristic is vital for components exposed to harsh environments, ensuring longevity and reliability in service.
Improved Weight-to-Strength Ratio
Many forged alloys, especially titanium and aluminum, offer an exceptional weight-to-strength ratio. This property is critical in industries such as aerospace, where reducing weight without compromising strength can lead to significant performance improvements.
Applications of Alloy Forged Components
Aerospace Industry
In the aerospace sector, alloy forged components are used extensively due to their lightweight and high-strength properties. Applications include:
- Aircraft landing gears
- Engine components
- Structural parts
Automotive Industry
The automotive industry relies on alloy forged materials for critical components that require high strength and durability, such as:
- Crankshafts
- Connecting rods
- Gears
Oil and Gas Industry
In oil and gas applications, forged components are vital for ensuring safety and reliability under extreme conditions. Common uses include:
- Valve bodies
- Pump components
- Flanges
Marine Applications
The marine industry utilizes alloy forged components for their corrosion resistance and strength, making them ideal for:
- Propeller shafts
- Marine hardware
- Structural components
Industrial Machinery
Forged components are crucial in manufacturing machinery, where durability and precision are required. Applications include:
- Gearboxes
- Cranes
- Hydraulic systems
Construction and Infrastructure
In construction, alloy forged materials are used for their strength and reliability in structural applications, such as:
- Beams
- Columns
- Fasteners
Medical Devices
The medical field uses forged components in devices that require high reliability and biocompatibility, including:
- Surgical instruments
- Implants
- Equipment fittings
Summary of Benefits and Applications
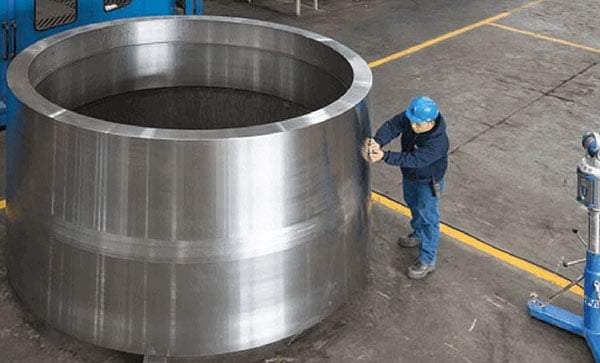
Benefit | Description |
---|---|
Enhanced Strength | Improved mechanical properties and durability |
Superior Resistance to Fatigue | Reduced likelihood of cracks and fatigue failure |
Improved Machinability | Easier cutting and shaping reduces manufacturing time |
Cost-Effectiveness | Long-term savings on maintenance and replacements |
Versatility in Applications | Suitable for various industries and uses |
Enhanced Corrosion Resistance | Longevity in harsh environments |
Improved Weight-to-Strength Ratio | Critical for performance in aerospace and automotive sectors |
Conclusion
Understanding the benefits and applications of alloy forged components is essential for industries that demand high performance and reliability. The forging process enhances the material’s properties, making it suitable for various applications, from aerospace to medical devices. By investing in alloy forged products, businesses can achieve greater durability, reduce maintenance costs, and enhance overall performance.
As industries continue to evolve, the demand for high-quality forged components will likely grow, making it crucial to partner with reliable manufacturers that specialize in alloy forging. This decision can significantly impact the success and safety of your projects.
FAQ
What is the difference between forging and casting?
Forging involves shaping metal using compressive forces, while casting involves pouring molten metal into a mold. Forged components typically have superior mechanical properties due to their refined grain structure.
What types of alloys are commonly used in forging?
Common alloys used in forging include steel, aluminum, titanium, and nickel alloys, each selected for its specific properties suitable for various applications.
Are alloy forged components more expensive than cast components?
While alloy forged components may have a higher initial cost, their durability and performance can lead to lower long-term maintenance and replacement costs, making them more cost-effective in the long run.
How do I select the right alloy for my forged components?
Selecting the right alloy depends on the specific application, environmental conditions, and performance requirements. Consulting with a material specialist or manufacturer can help in making the right choice.
What industries commonly use alloy forged components?
Alloy forged components are widely used in aerospace, automotive, oil and gas, marine, industrial machinery, construction, and medical device industries due to their strength and durability.