Shandong Qilu lndustrial Co.,Ltd.
Top Benefits of Using Forge Alloys in Modern Manufacturing
Welcome to My Blog!
Before we dive into the content, I’d love for you to join me on my social media platforms where I share more insights, engage with the community, and post updates. Here’s how you can connect with me:
Facebook:https://www.facebook.com/profile.php?id=100090903441806
Now, let’s get started on our journey together. I hope you find the content here insightful, engaging, and valuable.
Introduction
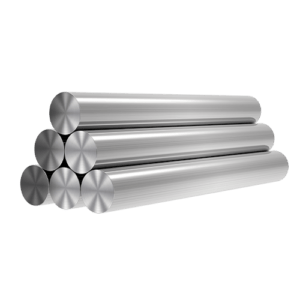
In the rapidly evolving world of manufacturing, forge alloys play a pivotal role in enhancing product quality, durability, and strength. As technology advances, the demand for robust, lightweight, and resilient materials has surged, making forge alloys a valuable choice across industries. This article delves into the many benefits of forge alloys in modern manufacturing, providing a comprehensive understanding of why they’re essential in today’s industrial landscape.
What Are Forge Alloys?
Forge alloys are metals that have undergone the forging process to increase their strength, hardness, and durability. Unlike casting or other forming processes, forging involves heating the metal until it becomes malleable, then applying pressure to shape it. This intense process enhances the metal’s grain structure, making forge alloys stronger and more resilient than many other materials.
Forged metals are widely used in industries such as automotive, aerospace, construction, and heavy machinery due to their robust mechanical properties.
The Process of Creating Forge Alloys
The creation of forged metals involves several essential steps. Here’s a breakdown:
- Heating: The metal is heated to a high temperature, making it pliable and easier to shape.
- Forging: Mechanical forces, often from hammering or pressing, shape the metal.
- Cooling and Finishing: The forged metal is allowed to cool and is sometimes tempered to achieve the desired properties.
Each of these stages is meticulously controlled to ensure that forged metals meet stringent quality standards.
Key Benefits of Forge Alloys in Manufacturing
Forge alloys offer several advantages that make them the preferred choice for manufacturing. Here are some of the top benefits:
Enhanced Strength and Durability
Forging rearranges the grain structure of the alloy, which results in greater strength and resilience. This makes forged metals ideal for high-stress applications, including heavy machinery, automotive components, and aerospace parts.
Superior Resistance to Fatigue
Forged metals are highly resistant to fatigue, meaning they can withstand repeated cycles of stress without failure. This property is crucial for applications in which components are subject to regular movement or pressure.
Improved Material Density
The forging process compacts the metal, resulting in a denser material. This denser structure gives forged metals an advantage in terms of strength-to-weight ratio, which is particularly beneficial for industries where weight reduction is essential.
Cost-Efficiency in the Long Run
While the initial cost of producing forged metals can be higher, the longevity and durability of the components made from these materials often result in cost savings over time.
Consistent Quality and Predictable Performance
Forged metals offer predictable mechanical properties, which makes them reliable and consistent in performance. This is especially important in industries where safety and precision are critical.
Common Applications of Forge Alloys
Forged metals are used in various industries due to their robustness. Below is a table highlighting some common applications:
Industry | Application | Benefits of Forge Alloys |
---|---|---|
Automotive | Engine components, gears | Improved strength and fatigue resistance |
Aerospace | Landing gear, turbine blades | Enhanced durability and resistance to high temperatures |
Construction | Structural supports, fasteners | Superior material density for stability and safety |
Oil and Gas | Drill bits, pipeline fittings | Exceptional wear resistance in high-pressure environments |
Heavy Machinery | Crankshafts, hydraulic components | High impact resistance and longevity |
Comparison of Forge Alloys with Other Materials
When comparing forged metals to other materials, there are a few factors that set them apart:
Factor | Forge Alloys | Cast Metals | Welded Metals |
---|---|---|---|
Strength | High | Moderate | Varies based on welding |
Durability | Very High | Moderate | Lower than forge alloys |
Density | Compact and dense | Less dense | Depends on welding method |
Fatigue Resistance | High | Low to moderate | Moderate |
The table above clearly illustrates why forged metals are often the preferred choice in industries where durability and strength are paramount.
Future Trends in Forge Alloys Manufacturing
The future of forged metals manufacturing holds exciting potential. Advancements in forging techniques and the development of new alloys continue to expand the applications of forge alloys. Here are some emerging trends:
- Advanced Alloy Compositions: Researchers are developing new alloy compositions with superior properties for specific applications.
- 3D Forging: Integrating 3D printing and forging technology could make the creation of forge alloys more efficient.
- Eco-Friendly Processes: Newer forging techniques aim to reduce waste and energy consumption, aligning with global sustainability goals.
These innovations suggest a promising future for forged metals as they become increasingly versatile and environmentally sustainable.
Conclusion
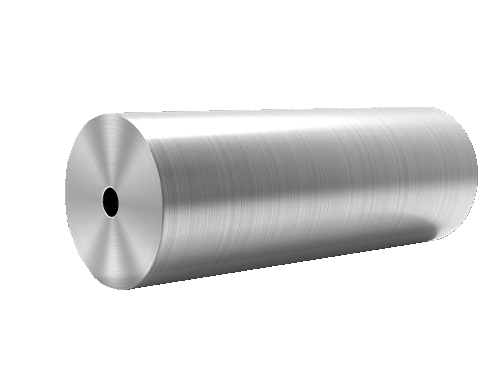
Forge alloys have revolutionized modern manufacturing by providing materials that are stronger, more durable, and resistant to wear and fatigue. Industries ranging from automotive to aerospace have reaped the benefits of forged metals, making them an indispensable component in critical applications. As technology and forging techniques evolve, the potential of forged metals will continue to grow, paving the way for innovations that will further strengthen modern manufacturing practices.
FAQs About Forge Alloys
What metals are commonly used in forge alloys?
Common metals include steel, aluminum, titanium, and copper. Each metal brings unique properties that are beneficial for different applications.
Why are forge alloys more expensive than other materials?
The forging process requires specialized equipment and skilled labor, which can increase costs. However, forged metals’ long-term durability and performance often offset the initial expense.
How do I choose the right forge alloy for my application?
The choice depends on factors such as the application’s requirements, environmental conditions, and budget. Consulting with a materials engineer can help ensure the best choice.
Can forge alloys be recycled?
Yes, many forge alloys, particularly those made from steel and aluminum, can be recycled, contributing to a more sustainable manufacturing process.
What is the difference between hot forging and cold forging?
Hot forging involves heating the metal, while cold forging occurs at or near room temperature. Hot forging is typically used for larger, more complex shapes, while cold forging is best for smaller parts with simpler shapes.