Shandong Qilu lndustrial Co.,Ltd.
Top Benefits of the Forging Metal Process in Manufacturing
Welcome to My Blog!
Before we dive into the content, I’d love for you to join me on my social media platforms where I share more insights, engage with the community, and post updates. Here’s how you can connect with me:
Facebook:https://www.facebook.com/profile.php?id=100090903441806
Now, let’s get started on our journey together. I hope you find the content here insightful, engaging, and valuable.
Introduction
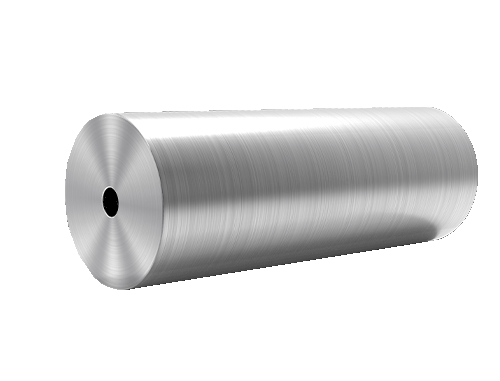
The forging metal process involves shaping metal using compressive forces, typically by hammering, pressing, or rolling. This ancient technique has evolved into a highly advanced process used to produce parts with superior strength and durability. Forging can be performed at various temperatures, including:
- Hot forging: Heating metal to make it malleable.
- Cold forging: Deforming metal at room temperature for precision.
- Warm forging: A hybrid of hot and cold forging techniques.
By understanding the benefits of the forging metal process, manufacturers can make informed decisions to optimize production.
Why the Forging Metal Process is Essential
Enhanced Strength and Durability
The forging metal process creates a refined grain structure, which improves the mechanical properties of the finished product. This makes forged parts:
- More resistant to fatigue.
- Capable of withstanding high-stress environments.
- Ideal for applications requiring long-term reliability.
Improved Structural Integrity
Unlike casting, where molten metal can form voids or porosity, forging compresses the material, resulting in a dense, uniform structure. This reduces the likelihood of defects and ensures higher quality.
Versatility Across Industries
The forging metal process is versatile, producing components for a wide range of industries, including:
- Aerospace: Jet engine parts, landing gears.
- Automotive: Crankshafts, gears, connecting rods.
- Oil and Gas: Valve bodies, flanges, couplings.
Types of Forging Techniques
Understanding the various forging methods is crucial for selecting the right approach:
Technique | Process | Applications |
---|---|---|
Open-Die Forging | Metal is deformed between flat dies. | Large parts like axles, gears. |
Closed-Die Forging | Metal is shaped in a closed cavity. | Precision components, automotive parts. |
Seamless Forging | Hollow parts like rings or cylinders are created. | Aerospace, pipelines. |
Cold Forging | Deformation occurs at room temperature. | Precision parts with tight tolerances. |
Each technique has specific advantages, making the forging metal process adaptable to diverse needs.
Top Benefits of the Forging Metal Process
Superior Mechanical Properties
Forged metals exhibit superior mechanical properties, such as:
- Higher tensile strength.
- Improved resistance to wear and tear.
- Better performance under extreme temperatures.
Cost Efficiency in the Long Run
While the initial tooling cost for forging might be higher, the long-term benefits include:
- Reduced material waste.
- Minimal post-processing requirements.
- Fewer part failures and replacements.
Design Flexibility
The forging metal process allows for custom shapes and sizes, accommodating complex designs while maintaining high strength.
Environmental Benefits
Forging produces less waste compared to machining or casting. Many modern forging facilities also focus on energy efficiency and recycling.
Table: Comparison of Forging vs. Other Metalworking Processes
Here’s how the forging metal process stacks up against other common methods:
Aspect | Forging | Casting | Machining |
---|---|---|---|
Material Strength | High | Moderate | Moderate |
Waste Generation | Low | Moderate | High |
Production Speed | Fast for large volumes | Slow | Moderate |
Initial Cost | High (tooling) | Low | Moderate |
Challenges in the Forging Metal Process
Despite its benefits, the forging metal process has some challenges:
High Initial Tooling Costs: Requires investment in specialized equipment and dies.
Complex Setup: Precision forging demands skilled labor and advanced machinery.
Material Limitations: Not all metals are suitable for forging.
By addressing these challenges, manufacturers can maximize the process’s potential.
Conclusion
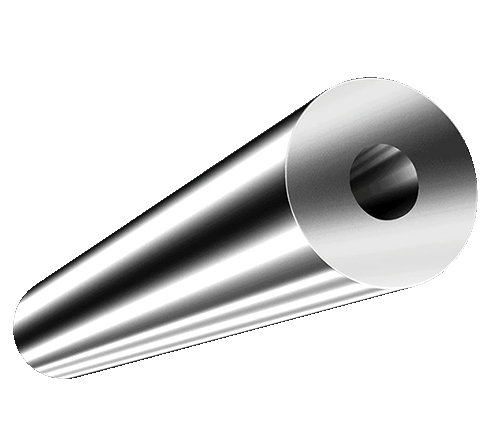
The forging metal process remains a critical manufacturing technique due to its unparalleled strength, durability, and versatility. By understanding its benefits and applications, industries can leverage this process for superior quality and cost-efficiency. Whether in aerospace, automotive, or energy sectors, forged components are the backbone of modern manufacturing.
With continuous advancements and innovations, the forging metal process is set to play an even more significant role in shaping the future of manufacturing.
FAQ: Common Questions About the Forging Metal Process
What makes forging different from casting?
Forging involves shaping metal using compressive forces, resulting in denser and stronger materials. Casting involves pouring molten metal into molds, which may lead to porosity and lower strength.
Can small businesses use the forging metal process?
Yes, smaller-scale forging setups or outsourcing to specialized facilities can make this process accessible.
Is cold forging better than hot forging?
It depends on the application. Cold forging offers precision, while hot forging provides malleability for complex shapes.
How do I choose the right forging technique?
Consider the metal type, desired properties, and application. Consulting with a forging expert can help.