Shandong Qilu lndustrial Co.,Ltd.
Top Benefits of Billet Forging in Metal Manufacturing
Welcome to My Blog!
Before we dive into the content, I’d love for you to join me on my social media platforms where I share more insights, engage with the community, and post updates. Here’s how you can connect with me:
Facebook:https://www.facebook.com/profile.php?id=100090903441806
Now, let’s get started on our journey together. I hope you find the content here insightful, engaging, and valuable.
Introduction
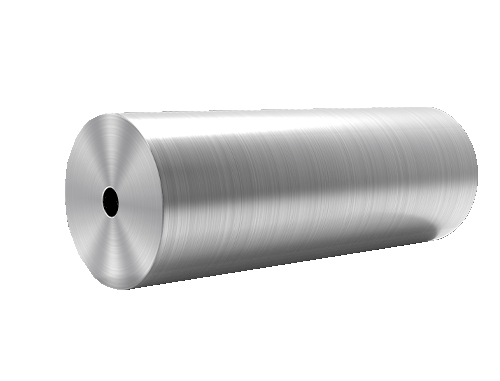
Billet forging is a core process in the metal manufacturing industry, recognized for producing high-strength, durable components with superior mechanical properties. Unlike casting or machining, billet forging uses compressive forces to shape preheated metal into desired forms, resulting in parts that exhibit exceptional structural integrity. In this comprehensive guide, we’ll explore the top benefits of billet forging in metal manufacturing and explain why it is a preferred method for industries requiring reliable, high-performance components.
With billet forging, manufacturers can enhance both the strength and performance of metals while reducing material waste. This article will also address frequently asked questions about billet forging to provide a complete understanding of the process and its applications.
What is Billet Forging?
Billet forging involves taking a solid piece of metal, known as a billet, and shaping it using compressive forces. The billet, often cylindrical or rectangular, is preheated to a specific temperature before being deformed into a desired shape by hammering or pressing. The process may be done using open die or closed die forging methods, depending on the complexity and size of the final product.
The extrusion forging process stands out for its ability to preserve the inherent strength of the metal. The forging technique helps in maintaining grain flow, which is essential for creating components that need to withstand extreme pressures or mechanical stress.
Billet Forging vs. Other Metal Forming Processes
Billet forging is often compared to other metalworking processes, such as casting and machining. Understanding the differences between these processes highlights the unique advantages extrusion forging offers.
- Casting: Casting involves melting metal and pouring it into a mold to form a shape. While casting is ideal for complex shapes, it often results in components with weaker mechanical properties due to porosity and inconsistent grain structure.
- Machining: Machining involves cutting away material from a larger block to create a part. While it can achieve high precision, it generates substantial material waste and may not deliver the same strength and durability as forged parts.
Billet forging, on the other hand, is superior in terms of strength, durability, and material efficiency, making it a go-to process for industries that require robust components.
Top Benefits of Billet Forging
Superior Mechanical Properties
One of the biggest advantages of extrusion forging is the superior mechanical properties it imparts to the final product. Forging compresses the metal, eliminating voids and reducing porosity. This leads to improved toughness, fatigue resistance, and tensile strength compared to cast or machined components.
Improved Grain Flow
During billet forging, the metal’s grain structure is altered in such a way that it follows the shape of the part. This enhanced grain flow increases the strength of the component, especially in areas that will experience stress during use. Proper grain alignment is crucial for parts subjected to heavy loads, as it improves performance and reduces the likelihood of failure.
Reduced Material Waste
Billet forging is an energy-efficient process that minimizes material waste. Unlike machining, which removes material to shape the part, forging reshapes the metal without significant material loss. This not only makes the process more cost-effective but also reduces environmental impact by lowering the amount of scrap metal produced.
Enhanced Durability
Forged parts, particularly those created through billet forging, are known for their exceptional durability. The dense structure of the forged metal makes it resistant to wear and tear, corrosion, and fatigue. This level of durability is especially beneficial in industries like aerospace, automotive, and construction, where parts are exposed to extreme conditions.
Versatility in Materials
Billet forging can be used with a wide range of materials, including steel, aluminum, titanium, and copper alloys. The process is versatile, making it ideal for various industries requiring high-performance metals with specific mechanical properties.
Cost Efficiency for Large Production Runs
While the initial tooling costs for billet forging can be higher than other methods like casting, it becomes increasingly cost-efficient as production volumes rise. The reduced material waste and the ability to produce stronger components mean less downtime and fewer replacements over time, making billet forging a cost-effective solution for large-scale production.
Customizability and Precision
Billet forging allows for a high degree of precision in the final part geometry. Using closed-die forging techniques, manufacturers can achieve near-net shapes that require little to no additional machining. This reduces production time and costs while providing the opportunity to customize parts based on specific needs.
Table: Comparison of Metal Forming Processes and Their Key Characteristics
Metal Forming Process | Strength | Material Waste | Grain Structure | Durability |
---|---|---|---|---|
Billet Forging | Very High | Low | Excellent grain flow | High |
Casting | Medium | Moderate | Poor grain structure | Medium |
Machining | Medium | High | No grain modification | Medium |
Extrusion | High | Low | Good grain structure | High |
This table highlights the advantages of billet forging compared to other metalworking processes, particularly in terms of strength, material efficiency, and grain structure optimization.
Applications of Billet Forging in Metal Manufacturing
Billet forging is essential across various industries due to its unique ability to produce high-strength, durable components. Below are some key industries where extrusion forging plays a critical role:
Aerospace Industry
In aerospace, components must be both lightweight and incredibly strong to handle the stresses of flight. Extrusion forging is used to manufacture aircraft engine parts, landing gear, and structural components that meet stringent safety and performance requirements.
Automotive Industry
The automotive industry relies on billet forging to produce durable parts such as crankshafts, gears, and connecting rods. These components must endure extreme forces, and extrusion forging ensures they can perform reliably over the lifespan of a vehicle.
Oil and Gas Industry
In the oil and gas sector, forged components like flanges, valves, and drill bits are crucial due to the extreme pressures and harsh environments they encounter. Billet forging provides the necessary strength and corrosion resistance for these demanding applications.
Construction and Heavy Machinery
Construction and heavy machinery industries use extrusion forging for parts that must withstand heavy loads, such as hydraulic components, shafts, and hammers. These parts need to be extremely durable to avoid costly breakdowns and repairs.
Medical Devices
Billet forging is also utilized in the medical field to create high-precision, durable instruments and implants. The process ensures that components like surgical tools and joint replacements maintain their strength and precision over time.
The Billet Forging Process: Step-by-Step
Understanding how extrusion forging works helps to clarify its many advantages. Below is a simplified breakdown of the extrusion forging process:
Material Selection
The process begins with selecting the appropriate metal based on the desired mechanical properties and final application. Commonly used materials include steel, aluminum, titanium, and copper alloys.
Billet Heating
The metal billet is preheated to a temperature that makes it malleable but not molten. Heating the billet ensures that it can be deformed without cracking and that the grain structure will align properly during the forging process.
Forging Operation
The heated billet is placed into a forging die, which determines the final shape of the part. Compressive forces are applied through a hammer or press, deforming the billet into the desired shape.
Cooling and Finishing
After forging, the part is cooled and may undergo additional processes such as heat treatment or machining to refine its properties or dimensions. The finished part is stronger, more durable, and has a more refined grain structure than it did extrusion forging.
Conclusion
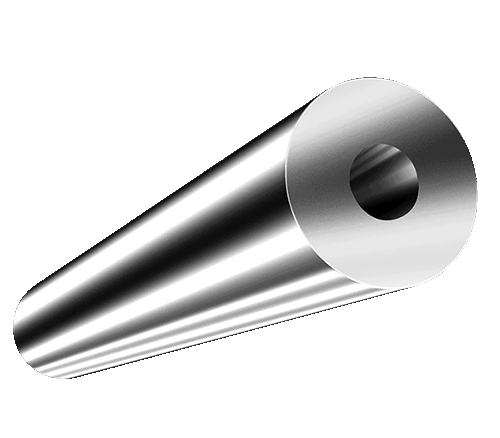
Billet forging offers a multitude of benefits that make it an indispensable process in metal manufacturing. From improving mechanical properties and durability to reducing material waste, extrusion forging stands out as a highly efficient and reliable method for producing high-strength components. Its applications across industries such as aerospace, automotive, and construction highlight its versatility and value in today’s manufacturing landscape. As technology advances, extrusion forging will continue to evolve, further enhancing its role in modern manufacturing processes.
FAQs
What is the difference between billet forging and casting?
Billet forging involves compressing preheated metal to shape it, resulting in components with superior mechanical properties and better grain structure compared to casting, which involves pouring molten metal into a mold.
Why is billet forging preferred for high-performance parts?
Billet forging is preferred because it creates parts with better strength, fatigue resistance, and durability due to the optimized grain structure and reduced porosity compared to other processes like casting or machining.
Can billet forging be used with all metals?
While billet forging is commonly used with materials like steel, aluminum, and titanium, it can be applied to a wide range of metals depending on the desired mechanical properties of the final product.
Is billet forging expensive?
Although extrusion forging can have higher initial costs due to tooling and equipment, it becomes cost-effective for large production runs because of its material efficiency and the long-term durability of the forged parts.
What industries benefit most from billet forging?
Industries such as aerospace, automotive, oil and gas, and heavy machinery benefit significantly from billet forging due to the high-performance requirements of their components.