Shandong Qilu lndustrial Co.,Ltd.
Top 10 Forged Shaft Manufacturers to Watch in 2024
Introduction
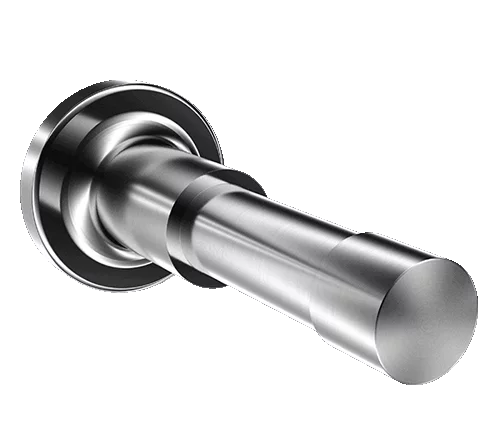
In 2024, the demand for precision-engineered forged shafts continues to grow across industries such as automotive, aerospace, and manufacturing. Selecting the right manufacturer is crucial for ensuring quality, reliability, and performance. This article highlights the top 10 forged shaft manufacturers known for their innovation and excellence.
What Makes a Top Forged Shaft Manufacturer?
Choosing the best forged shaft manufacturer also involves evaluating their research and development efforts in advancing forging techniques and materials. Leading manufacturers invest heavily in cutting-edge technologies such as 3D forging simulations and additive manufacturing to optimize designs and enhance the performance characteristics of forged shafts.
Furthermore, a manufacturer’s commitment to customer satisfaction is paramount for forged shaft manufacturers. This commitment encompasses not only delivering high-quality products but also providing responsive customer support, ensuring on-time delivery, and the flexibility to meet evolving customer specifications. These factors are instrumental in fostering long-term partnerships and maintaining a seamless supply chain experience with forged shaft manufacturers.
Top 10 Forged Shaft Manufacturers
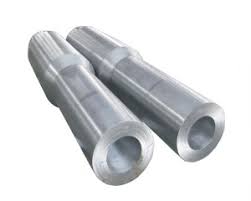
Rank | Manufacturer | Key Strengths | Industries Served |
---|---|---|---|
1 | Ellwood Closed Die | High precision forging techniques | Automotive, Aerospace |
2 | Scot Forge | Innovation in forging design | Oil & Gas, Power Generation |
3 | Bharat Forge | Large-scale production capabilities | Heavy Equipment, Marine |
4 | Qilu lndustrial | Strict adherence to international standards | Industrial Machinery |
5 | Finkl Steel | Cutting-edge forging technology | Renewable Energy |
6 | Doncasters Group | Versatility in shaft dimensions and shapes | Mining, Construction |
7 | Ellwood National Steel | Focus on sustainable manufacturing practices | Defense, Railways |
8 | FRISA | Global supply chain and logistics expertise | Aviation, Nuclear |
9 | Scot Forge (Medical) | Rapid prototyping and short lead times | Medical Devices, Robotics |
10 | PCC Forged Products | Excellence in customer service | Consumer Goods, Tooling |
Trends in Forged Shaft Manufacturing
In 2024, the industry is witnessing significant advancements in digital forging technologies, which are revolutionizing the precision and efficiency of shaft manufacturing processes. These technologies enable manufacturers to simulate and optimize forging designs with greater accuracy, reducing lead times and enhancing product quality.
Moreover, the adoption of lightweight materials continues to grow, driven by the need for improved fuel efficiency in automotive and aerospace applications. Manufacturers are exploring advanced alloys and composites that offer superior strength-to-weight ratios, contributing to lighter and more fuel-efficient end products.
Key Considerations When Choosing a Manufacturer
When selecting a forged shaft manufacturer, consider their track record of successfully delivering high-quality products to diverse industries over an extended period. Look for certifications such as ISO 9001, which ensure robust quality management systems are in place, guaranteeing consistency and reliability in their manufacturing processes. Additionally, assess their ability to adapt and innovate in response to evolving industry standards and technological advancements, ensuring they remain at the forefront of forging technology and capability.
Sustainability Practices in Forged Shaft Manufacturing
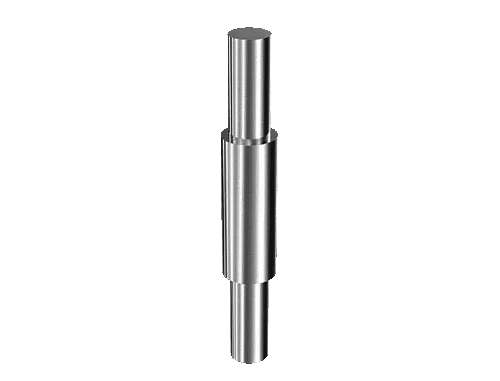
Sustainability is becoming increasingly important in the manufacturing industry, including forged shaft production. In 2024, leading manufacturers are adopting various sustainable practices to minimize environmental impact and enhance operational efficiency. Key initiatives include:
- Energy Efficiency: Implementing energy-efficient technologies and practices to reduce overall energy consumption during the forging process.
- Waste Reduction: Optimizing material usage and recycling scrap metals to minimize waste generation and improve resource efficiency.
- Emissions Control: Implementing advanced filtration systems and emission reduction technologies to mitigate air pollutants emitted during forging operations.
- Water Conservation: Adopting water-saving technologies and practices to minimize water usage and reduce environmental footprint.
- Supply Chain Sustainability: Collaborating with suppliers to ensure sustainable sourcing practices and promote environmental responsibility throughout the supply chain.
Conclusion
The manufacturers listed here represent the forefront of forged shaft production in 2024, each bringing unique strengths and capabilities to meet diverse industry needs. By choosing a manufacturer aligned with your specific requirements, you can ensure the reliability and performance of your critical components.
FAQ
Q: What are forged shafts used for?
A: Forged shafts are essential in industries like automotive, aerospace, and power generation for their strength, durability, and ability to withstand high stress and load conditions.
Q: How are forged shafts manufactured?
A: Forged shafts are typically made through hot forging, where a metal billet is heated and shaped using forging dies under high pressure. This process ensures superior mechanical properties compared to cast or machined shafts.
Q: What certifications should a forged shaft manufacturer have?
A: Look for manufacturers with certifications such as ISO 9001 (quality management), AS9100 (aerospace), or ISO 14001 (environmental management) to ensure they meet international standards for quality and compliance.