Shandong Qilu lndustrial Co.,Ltd.
The Process Behind Exceptional Bar Forging
Introduction
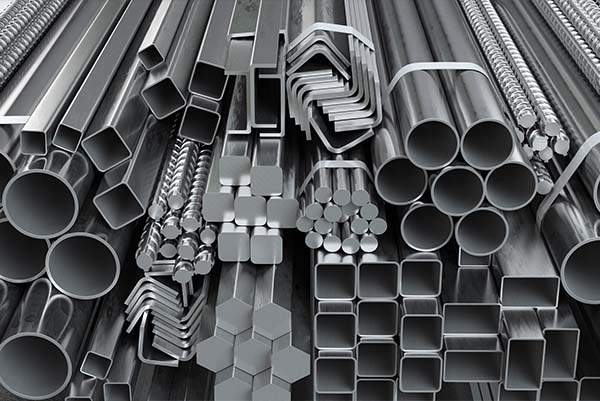
Bar forging stands as a pinnacle in the metallurgical industry, ensuring the creation of robust and high-quality metal bars. This article delves into the intricate process behind exceptional forging bar, exploring its significance, methods, and applications.
Understanding Bar Forging
Bar forging is a process of shaping metal bars through compressive forces, enhancing their strength, durability, and structural integrity. It involves various techniques such as open-die forging, closed-die forging, and seamless rolled ring forging. The choice of method depends on factors like the desired shape, material, and intended application.
The Key Steps in Bar Forging
Bar forging typically involves several key steps:
- Material Selection: Choosing the right metal alloy is crucial for achieving desired properties such as strength, corrosion resistance, and heat resistance.
- Heating: Metal bars are heated to a specific temperature to make them malleable and easier to shape.
- Forging Process: The heated metal is then shaped using mechanical or hydraulic presses, molds, or dies.
- Heat Treatment: After forging, the bars undergo heat treatment processes like quenching and tempering to optimize their mechanical properties.
- Finishing: The forged bars may undergo additional processes such as machining, grinding, or surface treatment for improved surface finish and dimensional accuracy.
The Importance of Quality Control
Quality control is paramount in forging bar to ensure the final products meet stringent standards. This involves:
- Dimensional Accuracy: Ensuring the bars meet specified tolerances and dimensions.
- Mechanical Properties: Conducting tests to verify properties like tensile strength, yield strength, and hardness.
- Non-Destructive Testing (NDT): Employing techniques such as ultrasonic testing or magnetic particle inspection to detect internal defects without damaging the bars.
- Metallurgical Analysis: Examining the microstructure of the bars to assess grain size, inclusion content, and overall integrity.
Advantages and Applications of Bar Forging
Bar forging offers numerous advantages, including:
- Enhanced Strength: Forged bars exhibit superior strength and toughness compared to cast or machined counterparts.
- Better Metallurgical Properties: The forging process refines the metal’s grain structure, resulting in improved mechanical properties and fatigue resistance.
- Cost Efficiency: Despite initial setup costs, forging bar often proves cost-effective in the long run due to reduced material wastage and enhanced product performance.
Forged bars find diverse applications across industries such as aerospace, automotive, oil and gas, and construction, where reliability, performance, and safety are paramount.
Comparison of Different Bar Forging Methods
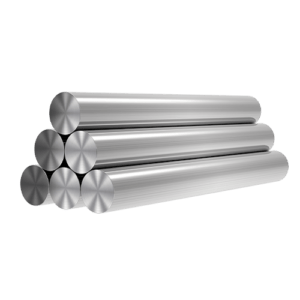
Method | Advantages | Disadvantages |
---|---|---|
Open-Die Forging | – Suited for large and complex shapes | – Less precise dimensional control |
– Minimal tooling requirements | – Limited repeatability | |
Closed-Die Forging | – High precision and dimensional accuracy | – Higher tooling costs |
– Excellent mechanical properties | – Limited to simpler shapes | |
Seamless Rolled Ring | – Superior grain structure and mechanical properties | – Limited to cylindrical shapes |
Forging | – Cost-effective for high-volume production | – Longer lead times for tooling and setup |
Conclusion
Bar forging exemplifies the synergy of craftsmanship, technology, and metallurgical science. By meticulously controlling the forging process and adhering to rigorous quality standards, manufacturers can produce bars of exceptional quality and performance, meeting the diverse needs of modern industries.
FAQ
Q: What materials are commonly used in bar forging?
A: Common materials include carbon steel, alloy steel, stainless steel, aluminum, and titanium.
Q: How does bar forging differ from other metal forming processes?
A: Unlike casting or machining, forging subjects the metal to compressive forces, which align the grain structure and enhance its mechanical properties.
Q: Is bar forging suitable for small-scale production?
A: While bar forging can be adapted for small-scale production, it is more commonly used for medium to large-scale manufacturing due to setup costs and equipment requirements.
Q: What factors influence the choice of forging method?
A: Factors such as part complexity, desired properties, production volume, and cost considerations influence the selection of forging method.
In conclusion, bar forging is a time-honored technique that continues to play a crucial role in shaping the modern world, providing robust and reliable components for various industries.