Shandong Qilu lndustrial Co.,Ltd.
The Future of the Forgings Industry: Trends to Watch
Welcome to My Blog!
Before we dive into the content, I’d love for you to join me on my social media platforms where I share more insights, engage with the community, and post updates. Here’s how you can connect with me:
Facebook:https://www.facebook.com/profile.php?id=100090903441806
Now, let’s get started on our journey together. I hope you find the content here insightful, engaging, and valuable.
Introduction
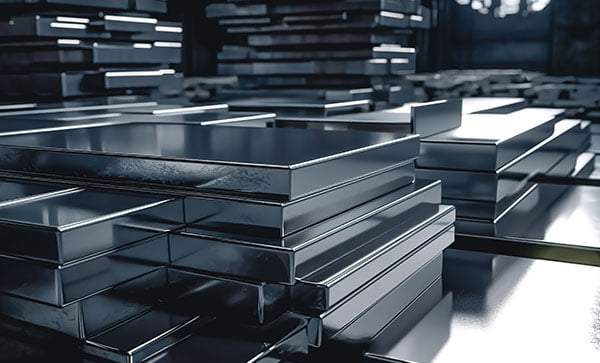
The forgings industry has long been a cornerstone of manufacturing, with applications ranging from aerospace and automotive to heavy machinery and construction. As technology continues to advance and market demands shift, the future of the forgings industry is on the brink of significant transformation. In this blog post, we will explore the key trends shaping the future of the forgings industry, the challenges it faces, and the opportunities it presents for manufacturers and suppliers alike.
The forgings industry plays a vital role in producing strong, durable, and high-performance metal parts through the process of forging, where metal is shaped under high pressure. This industry is evolving rapidly, driven by innovations in materials, technology, and production processes. Understanding these trends is crucial for businesses looking to stay competitive and future-proof their operations.
Key Trends in the Forgings Industry
Technological Advancements
The most significant trend in the forgings industry is the integration of cutting-edge technology. Automation, artificial intelligence (AI), and machine learning are becoming increasingly important in streamlining production processes. Advanced robotics and automated forging systems allow for higher precision, faster production times, and reduced human error. Moreover, additive manufacturing (3D printing) is beginning to make its mark, especially in prototyping and producing complex components that were previously difficult or costly to forge using traditional methods. These technologies are improving quality control, reducing waste, and optimizing resource use, all of which contribute to the overall efficiency of the forgings industry.
Sustainability and Eco-Friendly Practices
As sustainability becomes a key focus across all industries, the forgings industry is also working towards reducing its environmental impact. Manufacturers are adopting more eco-friendly practices, including the use of recycled materials, energy-efficient machinery, and processes that minimize waste. Additionally, the demand for lightweight and durable forged components, particularly in the automotive and aerospace sectors, is driving the development of more sustainable materials and production methods.
Customization and Demand for Complex Parts
The forgings industry is seeing a rise in the demand for highly customized parts, especially in industries like aerospace and defense, where precision and quality are paramount. Companies are investing in advanced forging techniques to create more complex and intricate components, which require precise control over material properties and forging methods. This trend is particularly evident in the production of turbine blades, engine components, and other critical parts. Table: Types of Forging Techniques for Complex Parts Forging Technique Characteristics Common Applications Closed-Die Forging High precision, complex shapes, high material utilization Aerospace components, automotive parts Open-Die Forging Suitable for larger, simpler shapes, flexible process Heavy machinery, rail transport Ring Rolling Produces seamless rings, ideal for circular shapes Aerospace, energy sectors Precision Forging Used for small, intricate parts with tight tolerances Medical implants, high-performance parts
Digitalization and Industry 4.0
Digital transformation is another significant trend in the forgings industry. Industry 4.0 technologies, such as IoT (Internet of Things), big data analytics, and cloud computing, are enabling manufacturers to gather real-time data from machines and processes. This data can be analyzed to improve production efficiency, predict maintenance needs, and optimize the entire supply chain. The rise of digital twins—virtual representations of physical forging processes—allows companies to simulate and test new designs before physically producing them, reducing time and costs.
Globalization and Supply Chain Evolution
As the world becomes increasingly interconnected, the forgings industry is experiencing greater competition, especially from low-cost manufacturing regions such as Asia. However, this has also led to greater collaboration across borders, with companies in different regions exchanging technology, expertise, and resources. Additionally, the globalization of supply chains means that companies need to adapt quickly to changing market demands and economic conditions.
Material Innovation
Innovations in materials science are another key driver in the future of the forgings industry. New alloys and composite materials are being developed to meet the needs of industries such as aerospace, automotive, and energy. For example, high-performance steel alloys, titanium, and superalloys are in demand for their lightweight and high-strength properties. These materials can withstand extreme conditions, making them ideal for use in engine parts, aircraft, and turbines. Manufacturers are also exploring bio-based and recyclable materials to improve sustainability.
Workforce Development and Training
With the increased adoption of new technologies and complex processes, there is a growing need for a highly skilled workforce in the forgings industry. Companies are investing in training and development programs to ensure that their workers have the skills necessary to operate advanced machinery and adapt to changing production methods. This trend is crucial to maintaining a competitive edge in an increasingly automated and digitalized manufacturing landscape.
Challenges Facing the Forgings Industry
Cost Pressure
The forgings industry is under constant pressure to reduce costs, especially as raw material prices fluctuate and competition intensifies. Companies must find ways to balance cost-saving initiatives with maintaining the quality and precision of their forged products.
Supply Chain Disruptions
The COVID-19 pandemic highlighted vulnerabilities in global supply chains, and the forgings industry has not been immune. From material shortages to delays in transportation, disruptions continue to challenge manufacturers. To mitigate these risks, companies are investing in more resilient and flexible supply chains.
Environmental Regulations
As governments around the world impose stricter environmental regulations, the forgings industry must comply with new standards concerning emissions, waste management, and energy consumption. Adapting to these regulations requires significant investment in new technologies and processes.
Opportunities in the Forgings Industry
Expansion into Emerging Markets
With industries like automotive, aerospace, and energy expanding rapidly in emerging markets, the forgings industry has a significant opportunity for growth. Countries in Asia, Africa, and South America are investing in infrastructure and industrialization, creating demand for high-quality forged components.
Collaboration with Tech Companies
The increasing reliance on technology presents a unique opportunity for collaboration between forging companies and technology providers. Partnering with software and automation experts can lead to the development of next-generation forging techniques that improve production efficiency and part quality.
Conclusion
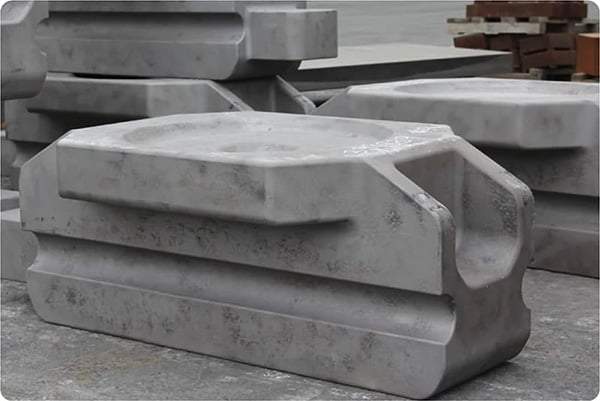
The future of the forgings industry is both exciting and challenging. As technology advances, material science evolves, and sustainability becomes a central focus, the industry will continue to adapt and innovate. By staying ahead of trends such as automation, digitalization, and customization, manufacturers in the forgings industry can position themselves for success in the years to come.
FAQ
What is the main trend shaping the future of the forgings industry?
Technological advancements, such as automation, AI, and 3D printing, are the main trends influencing the future of the forgings industry.
How does sustainability impact the forgings industry?
Sustainability drives the adoption of eco-friendly practices, such as using recycled materials and energy-efficient processes, in the forgings industry.
What are the common applications of forging techniques?
Forging techniques are commonly used in industries like aerospace, automotive, heavy machinery, and energy for producing durable, high-performance parts.
How can companies stay competitive in the forgings industry?
Companies can stay competitive by adopting new technologies, investing in workforce training, and focusing on quality and innovation.
What challenges does the forgings industry face?
Challenges include cost pressures, supply chain disruptions, and adapting to stringent environmental regulations.