Shandong Qilu lndustrial Co.,Ltd.
The Future of Aerospace Forging in Modern Manufacturing
Welcome to My Blog!
Before we dive into the content, I’d love for you to join me on my social media platforms where I share more insights, engage with the community, and post updates. Here’s how you can connect with me:
Facebook:https://www.facebook.com/profile.php?id=100090903441806
Now, let’s get started on our journey together. I hope you find the content here insightful, engaging, and valuable.
Introduction
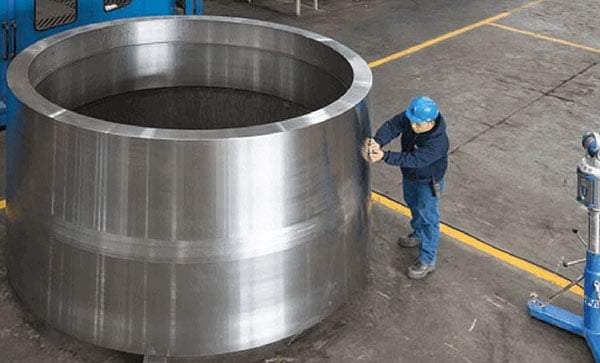
Aerospace forging plays a critical role in the manufacturing of components used in aircraft and spacecraft. As the aerospace industry evolves, so too does the technology and methods used in aerospace forging. This blog will explore the current landscape and future trends of aerospace forging, examining its benefits, challenges, and innovations shaping modern manufacturing. Whether you are an industry professional or an enthusiast, understanding the future of aerospace forging is essential in grasping how it influences the broader aerospace sector.
Overview of Aerospace Forging
Aerospace manufacturing is a manufacturing process that involves shaping metal using localized compressive forces. This technique is vital for producing high-strength components that can withstand the extreme conditions experienced in aerospace applications. The forging process can involve various methods, including open-die, closed-die, and isothermal forging, each with unique applications and benefits.
Key Characteristics of Aerospace Forging:
- Material Integrity: The forging process improves the grain structure of metals, resulting in enhanced mechanical properties.
- Precision: Aerospace manufacturing allows for the production of complex geometries with tight tolerances.
- Durability: Forged components are typically stronger and more reliable than those produced through casting or machining.
Key Benefits of Aerospace Forging
Aerospace forging offers numerous advantages that contribute to its prominence in the industry:
Benefit | Description |
---|---|
Increased Strength | Forged parts have superior strength due to improved grain flow. |
Weight Reduction | Forging allows for lightweight designs without compromising strength. |
Enhanced Fatigue Resistance | Forged components exhibit better resistance to fatigue and stress. |
Reduced Waste | The forging process generates less scrap material compared to casting. |
These benefits make aerospace manufacturing an attractive choice for manufacturers aiming to enhance performance while maintaining cost-effectiveness.
Current Trends in Aerospace Forging
As the aerospace sector continues to advance, several key trends are emerging in aerospace forging:
- Additive Manufacturing Integration: The integration of additive manufacturing techniques with forging processes is enabling the creation of complex parts that were previously challenging to produce.
- Sustainability Efforts: There is an increasing focus on sustainable practices, including the use of eco-friendly materials and reducing carbon footprints in the forging process.
- Digital Transformation: The adoption of Industry 4.0 technologies, including IoT and data analytics, is enhancing process efficiency and quality control.
These trends are shaping the future of aerospace manufacturing, pushing the boundaries of what is possible in manufacturing.
Innovative Technologies in Aerospace Forging
The future of aerospace forging is being driven by innovations in technology. Some notable advancements include:
- Smart Forging Machines: These machines utilize AI and machine learning to optimize forging processes, resulting in improved precision and reduced cycle times.
- Robotics and Automation: Automated systems are enhancing production efficiency and safety by minimizing manual labor and human error.
- Advanced Materials: Research into new alloys and composites is leading to the development of materials that can withstand higher temperatures and stresses, further enhancing the capabilities of forged components.
Here’s a table summarizing some of these innovative technologies:
Technology | Impact |
---|---|
AI and Machine Learning | Optimizes forging parameters for better quality and efficiency. |
Robotics | Reduces labor costs and improves safety. |
New Alloys and Composites | Enhances performance under extreme conditions. |
Challenges Facing Aerospace Forging
Despite its advantages, aerospace manufacturing is not without challenges:
- High Production Costs: The initial investment in forging equipment and technology can be substantial, which may deter smaller manufacturers.
- Material Limitations: Some advanced materials can be challenging to forge due to their unique properties, requiring specialized processes.
- Supply Chain Issues: Global supply chain disruptions can affect the availability of raw materials necessary for forging operations.
Addressing these challenges will be crucial for the continued growth of aerospace manufacturing in the manufacturing landscape.
The Future Outlook for Aerospace Forging
The future of aerospace forging looks promising, with several key developments on the horizon:
- Increased Demand for Lightweight Components: As the aerospace industry pushes for more fuel-efficient designs, the demand for lightweight, high-strength forged components will continue to rise.
- Enhanced Collaboration: Greater collaboration between manufacturers, material scientists, and engineers will lead to innovative forging solutions tailored to specific aerospace applications.
- Global Expansion: Emerging markets are beginning to invest in aerospace manufacturing, creating new opportunities for aerospace manufacturing globally.
In summary, the future of aerospace forging is bright, with opportunities for growth and innovation that will shape the industry’s landscape.
Conclusion
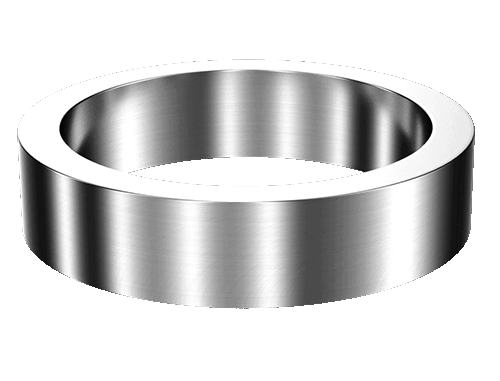
Aerospace forging is at the forefront of modern manufacturing, playing a pivotal role in the production of components that meet the rigorous demands of the aerospace industry. With ongoing advancements in technology, a commitment to sustainability, and the pursuit of efficiency, the future of aerospace manufacturing is bright. As manufacturers adapt to emerging trends and challenges, they will continue to shape the landscape of aerospace manufacturing, ensuring that forged components remain integral to the industry’s evolution.
Frequently Asked Questions (FAQ) About Aerospace Forging
What materials are commonly used in aerospace forging?
Common materials include aluminum alloys, titanium alloys, and steel, each chosen for their specific properties and application requirements.
How does aerospace forging differ from other manufacturing processes?
Unlike casting, which involves pouring molten metal into molds, forging involves shaping solid metal through compressive forces, resulting in enhanced strength and integrity.
What industries benefit from aerospace forging?
While primarily used in aerospace, forging is also crucial in automotive, marine, and industrial applications where high-strength components are required.
What advancements are being made in aerospace forging technology?
Innovations include the integration of AI for process optimization, the use of robotics for increased efficiency, and the development of new materials with superior properties.
How does the sustainability movement impact aerospace forging?
The aerospace industry is focusing on sustainable practices, such as reducing waste and carbon emissions, which is driving advancements in eco-friendly forging processes.