Shandong Qilu lndustrial Co.,Ltd.
The Advantages of Billet Forging in Industrial Manufacturing
Introduction
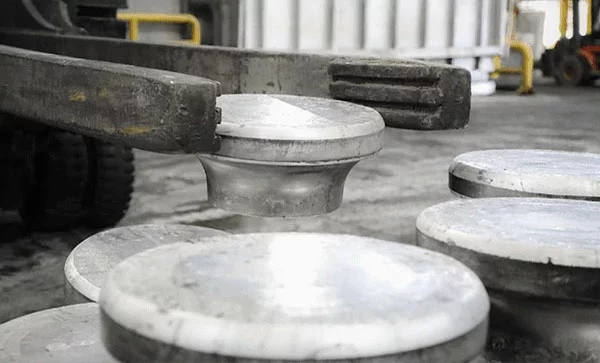
In the realm of industrial manufacturing, the process of billet forging stands out as a cornerstone technique. With its ability to shape metal into complex geometries with exceptional strength and durability, billet forging offers a myriad of advantages over other manufacturing methods. In this article, we delve into the various benefits of billet forging and its applications across industries.
Understanding Billet Forging
Billet forging, also known as open-die forging, involves shaping metal by compressing it between two dies that do not completely enclose the material. Instead, the metal is worked into the desired shape through repeated hammering or pressing. This process is highly versatile and can produce components ranging from small intricate parts to large industrial machinery.
Advantages of Billet Forging
- Enhanced Strength and Durability: Billet forging results in superior mechanical properties compared to other manufacturing methods. The process refines the grain structure of the metal, leading to increased strength, toughness, and resistance to fatigue.
- Cost-Effectiveness: While the initial setup costs for billet forging may be higher than some other methods, the long-term benefits outweigh the investment. The durability and reliability of forged components often translate to lower maintenance and replacement costs over time.
- Customization and Design Flexibility: Billet forging offers unparalleled flexibility in design. Manufacturers can create intricate shapes and complex geometries that are not feasible with other techniques. This allows for the production of highly customized components tailored to specific applications.
- Improved Metallurgical Properties: The forging process results in a more homogeneous microstructure with fewer defects compared to cast components. This leads to improved metallurgical properties such as better corrosion resistance and thermal stability.
- Material Utilization: Billet forging minimizes material waste by efficiently shaping the metal into the desired form. Unlike machining processes, which often produce significant scrap, forging maximizes material utilization and reduces environmental impact.
Applications of Billet Forging
Billet forging finds widespread applications across various industries, including aerospace, automotive, oil and gas, and construction. From aircraft components to high-performance automotive parts, forged products play a critical role in ensuring safety, reliability, and performance in demanding environments.
Case Study: Billet Forging in Aerospace Manufacturing
To illustrate the advantages of billet forging, let’s consider its application in aerospace manufacturing. Aircraft components such as landing gear, engine parts, and structural elements require exceptional strength, reliability, and precision. Billet forging allows aerospace manufacturers to meet these stringent requirements by producing forged components with superior mechanical properties and dimensional accuracy.
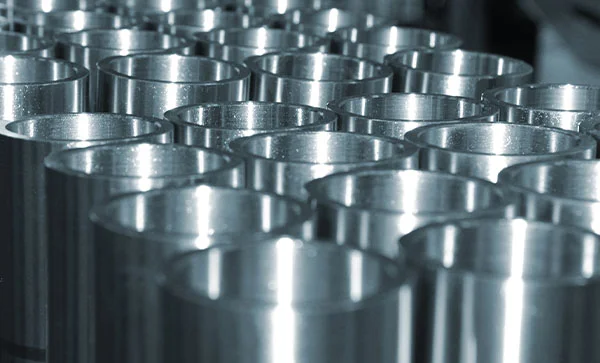
Component | Material | Forging Process | Advantages |
---|---|---|---|
Landing Gear | Titanium Alloy | Closed-Die Forging | Enhanced Strength, Fatigue Resistance |
Engine Shaft | Nickel Alloy | Open-Die Forging | Custom Geometries, High Temperature Resistance |
Structural Bracket | Aluminum Alloy | Press Forging | Lightweight, Corrosion Resistance |
Conclusion
In conclusion, billet forging stands as a cornerstone technique in industrial manufacturing, offering unparalleled strength, durability, and design flexibility. From aerospace to automotive applications, the advantages of billet forging are evident in the performance and reliability of forged components. As industries continue to demand higher performance and efficiency, billet forging remains a critical process for meeting these evolving requirements.
FAQ
Q: What materials can be forged using the billet forging process?
A: Billet forging can be applied to a wide range of materials, including steel, aluminum, titanium, nickel alloys, and more.
Q: Is billet forging suitable for mass production?
A: While billet forging is commonly used for low to medium volume production, it can also be scaled up for mass production depending on the complexity of the components and the efficiency of the forging process.
Q: How does billet forging compare to other manufacturing methods such as casting or machining?
A: Billet forging offers several advantages over casting and machining, including higher strength, improved metallurgical properties, better dimensional accuracy, and reduced material waste. However, the choice of manufacturing method depends on factors such as component complexity, material properties, and production volume.