Shandong Qilu lndustrial Co.,Ltd.
Stainless Steel Forgings: Expertly Crafted
Welcome to My Blog!
Before we dive into the content, I’d love for you to join me on my social media platforms where I share more insights, engage with the community, and post updates. Here’s how you can connect with me:
Facebook:https://www.facebook.com/profile.php?id=100090903441806
Now, let’s get started on our journey together. I hope you find the content here insightful, engaging, and valuable.
Table of Contents
Introduction
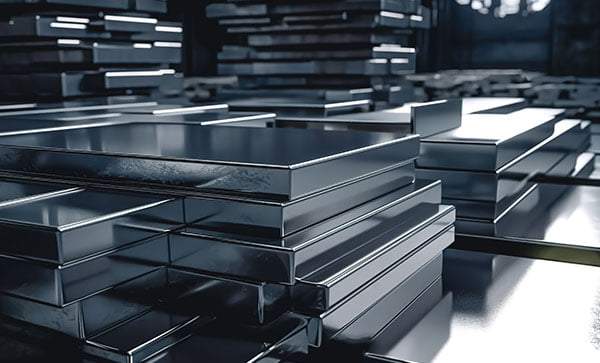
Stainless steel forgings are essential components in numerous industries due to their exceptional combination of corrosion resistance, strength, and durability. These high-performance components are meticulously crafted through a series of precise manufacturing processes. By understanding the intricacies of stainless steel forgings, engineers and manufacturers can harness their potential to optimize product designs and elevate overall performance.
The Manufacturing Process of Stainless Steel Forgings
The creation of stainless steel forgings is a complex and meticulous process that involves several critical steps:
Material Selection: The first step in the manufacturing process is the careful selection of the appropriate stainless steel alloy. Different alloys possess distinct properties, such as varying levels of corrosion resistance, strength, and ductility. Common alloys used for forgings include 304, 316, and 410 stainless steel, each suited for specific applications.
Heating: Once the desired alloy is selected, the raw material, often in the form of a billet, is subjected to a precise heating process. The billet is heated to a specific temperature, known as the forging temperature, to enhance its plasticity. This elevated temperature allows the metal to deform more readily under applied forces, facilitating the shaping process.
Forging: The heated billet is then transferred to a forging press, where it undergoes intense compressive forces. The forging process can be performed using various techniques, including open-die forging, impression die forging, and closed-die forging. Each method offers unique advantages and is selected based on the complexity of the desired shape and the required tolerances.
Heat Treatment: After the initial shaping, the forged component undergoes a critical heat treatment process. This process involves carefully controlled heating and cooling cycles to modify the microstructure of the metal and achieve the desired mechanical properties. Heat treatment techniques such as annealing, quenching, and tempering are employed to enhance the strength, hardness, and ductility of the forging.
Machining and Finishing: The final stage of the manufacturing process involves precision machining and finishing operations. These operations are essential to achieve the precise dimensions, tolerances, and surface finishes required for specific applications. Machining processes, such as milling, drilling, and turning, are used to remove excess material and create complex features. Finishing techniques, such as grinding, polishing, and shot peening, are employed to refine the surface and improve its appearance and performance.
Advantages of Stainless Steel Forgings
Stainless steel forgings offer a multitude of advantages that make them an ideal choice for a wide range of applications:
Exceptional Corrosion Resistance: Stainless steel’s inherent resistance to corrosion is a significant advantage, particularly in harsh environments such as marine applications, chemical processing, and food processing. The protective oxide film that forms on the surface of stainless steel prevents corrosion, ensuring long-term durability and reliability.
High Strength and Durability: Stainless steel forgings possess exceptional strength and toughness, enabling them to withstand heavy loads and demanding operating conditions. This makes them suitable for critical components in industries such as automotive, aerospace, and oil and gas.
Versatility: The wide range of stainless steel alloys available offers unparalleled versatility. Different alloys can be selected to meet specific performance requirements, such as high strength, corrosion resistance, or heat resistance. This versatility allows engineers to design components that are optimized for their intended applications.
Dimensional Accuracy and Precision: Precision forging techniques, combined with advanced machining and finishing processes, ensure that stainless steel forgings meet stringent dimensional tolerances and specifications. This accuracy is crucial for components that require precise fit and function, such as those used in aerospace and medical devices.
Long Service Life: Stainless steel forgings offer excellent longevity, reducing the need for frequent replacements and minimizing downtime. Their durability and resistance to corrosion contribute to their extended service life, making them a cost-effective solution in the long run.
Applications of Stainless Steel Forgings
Stainless steel forgings find extensive applications in a diverse range of industries:
Automotive: Stainless steel forgings are used in various automotive components, including crankshafts, connecting rods, suspension components, and steering components. Their high strength, durability, and corrosion resistance make them ideal for these demanding applications.
Aerospace: The aerospace industry relies heavily on stainless steel forgings for critical components such as landing gear components, engine parts, and fasteners. Their lightweight, high-strength, and corrosion-resistant properties are essential for ensuring the safety and reliability of aircraft.
Oil and Gas: In the oil and gas industry, stainless steel forgings are used in valves, fittings, pumps, and other components that come into contact with corrosive fluids and harsh environments. Their exceptional corrosion resistance and durability make them suitable for these demanding applications.
Chemical Processing: The chemical processing industry utilizes stainless steel forgings in piping, tanks, heat exchangers, and other equipment that handles corrosive chemicals. Their corrosion resistance and ability to withstand high temperatures and pressures make them ideal for these applications.
Medical Devices: Stainless steel forgings are used in the manufacturing of surgical instruments, implants, and other medical devices. Their biocompatibility, corrosion resistance, and high strength make them suitable for these critical applications.
Food Processing: In the food processing industry, stainless steel forgings are used in equipment that comes into contact with food and beverages. Their corrosion resistance and ease of cleaning make them ideal for maintaining hygienic conditions and preventing contamination.
Stainless Steel Forgings vs. Castings: A Comparison
Feature | Stainless Steel Forgings | Stainless Steel Castings |
---|---|---|
Grain Structure | Fine and uniform | Coarse and irregular |
Strength | Higher strength and toughness | Lower strength and toughness |
Dimensional Accuracy | High dimensional accuracy | Lower dimensional accuracy |
Cost | Generally higher cost | Lower cost |
Complexity of Shapes | Limited to simpler shapes | Can produce complex shapes |
Factors to Consider When Selecting Stainless Steel Forgings
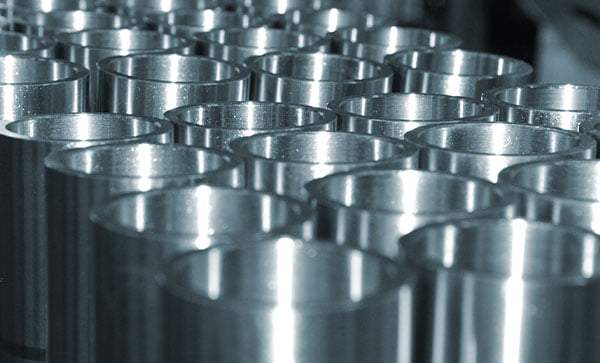
When selecting stainless steel forgings, several factors must be considered to ensure that the components meet the specific requirements of the application:
Alloy Selection: The choice of stainless steel alloy is crucial, as different alloys possess varying properties. Factors such as corrosion resistance, strength, ductility, and cost should be considered when selecting the appropriate alloy.
Forging Process: The selection of the appropriate forging process depends on the complexity of the desired shape, the required tolerances, and the quantity of forgings needed. Open-die forging, impression die forging, and closed-die forging are common techniques used for stainless steel forgings.
Heat Treatment: Heat treatment is a critical step in the manufacturing process, as it significantly influences the mechanical properties of the forging. The specific heat treatment process, such as annealing, quenching, or tempering, is selected based on the desired properties.
Tolerances: The required tolerances must be specified to ensure that the forgings meet the dimensional requirements of the application. Tight tolerances can be achieved through precision forging techniques and advanced machining processes.
Quantity: The quantity of forgings required can impact the manufacturing process and cost. Large quantities may justify investments in specialized tooling and equipment to optimize production efficiency.
Conclusion
Stainless steel forgings are indispensable components in a wide range of industries due to their exceptional performance and reliability. Their combination of strength, corrosion resistance, and durability, coupled with their versatility and precision, makes them ideal for critical applications. By understanding the manufacturing process, advantages, and applications of stainless steel forgings, engineers and manufacturers can make informed decisions to optimize their product designs and elevate overall performance.
FAQ
Q: What is the difference between stainless steel forgings and castings?
A: Stainless steel forgings are created by shaping metal through compressive forces, resulting in a fine-grained, dense microstructure. Castings, on the other hand, are formed by pouring molten metal into a mold, resulting in a coarser-grained structure. Forgings generally offer superior mechanical properties, such as higher strength and toughness.
Q: How is the strength of a stainless steel forging determined?
A: The strength of a stainless steel forging is influenced by several factors, including the alloy composition, the forging process, and the subsequent heat treatment. The specific alloy selected, the forging techniques employed, and the heat treatment parameters significantly impact the final mechanical properties of the forging.
Q: What are the common stainless steel alloys used for forgings?
A: Some of the most common stainless steel alloys used for forgings include:
- 304 Stainless Steel: A versatile alloy known for its excellent corrosion resistance and good mechanical properties.
- 316 Stainless Steel: Offers superior corrosion resistance, particularly in chloride-containing environments.
- 410 Stainless Steel: A martensitic stainless steel that provides high strength and hardness.