Shandong Qilu lndustrial Co.,Ltd.
Ring Rolling Forging: Enhancing Strength and Durability
Welcome to My Blog!
Before we dive into the content, I’d love for you to join me on my social media platforms where I share more insights, engage with the community, and post updates. Here’s how you can connect with me:
Facebook:https://www.facebook.com/profile.php?id=100090903441806
Now, let’s get started on our journey together. I hope you find the content here insightful, engaging, and valuable.
Introduction
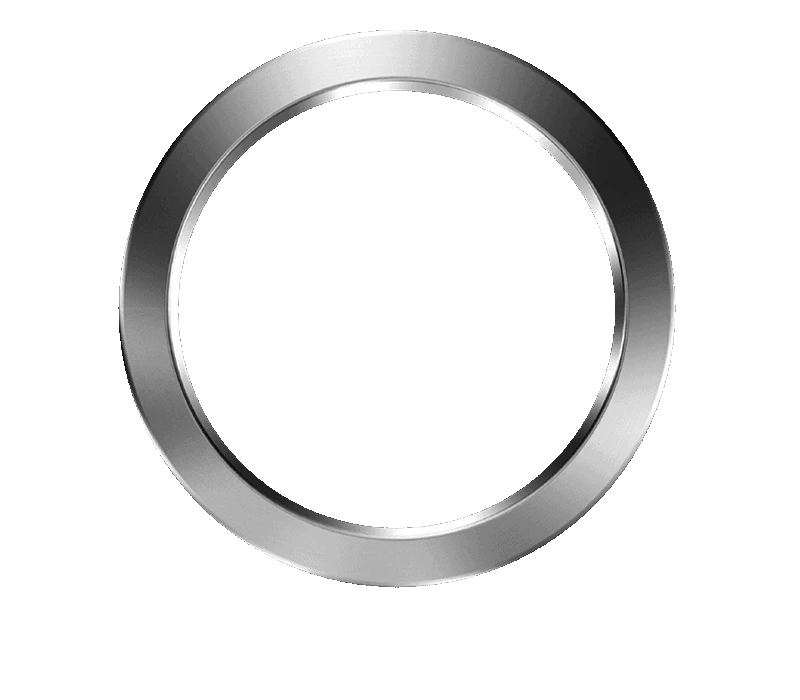
Ring rolling forging is a sophisticated manufacturing process that plays a crucial role in enhancing the strength and durability of metal components. This technique involves the deformation of metal rings using a rolling process to achieve the desired geometric and mechanical properties. It is widely used in industries ranging from aerospace to automotive, owing to its ability to produce high-quality, high-performance components. In this blog, we will delve into the intricacies of ring forging, exploring its benefits, applications, and technological advancements.
What is Ring Rolling Forging?
Ring rolling forging is a specialized forging process used to shape metal into ring-like components. The process starts with a preheated metal billet, which is placed between two rotating rolls. The rolls apply pressure to the billet, causing it to expand radially and contract axially, forming a ring shape. The ring is then further processed to achieve the desired dimensions and properties.
Advantages of Ring Rolling Forging
- Improved Mechanical Properties: Ring rolling forging significantly enhances the mechanical properties of metal components. The process aligns the grain structure in a favorable orientation, resulting in higher strength and better fatigue resistance.
- Reduced Material Waste: Compared to traditional forging methods, ring forging is more material-efficient. The process minimizes waste by using nearly the entire billet, which is especially beneficial for high-cost metals.
- Cost-Effective Production: The high precision of ring forging reduces the need for additional machining and finishing, leading to lower overall production costs.
- Versatility: This method can be used with a wide range of metals, including steel, aluminum, and titanium, making it suitable for various applications.
Applications of Ring Rolling Forging
Ring rolling forging is employed in numerous industries due to its versatility and effectiveness. Below are some key applications:
Aerospace Industry
- Engine Components: The aerospace sector relies on ring rolling forging for producing high-strength components such as turbine rings, compressor disks, and shafts.
- Structural Parts: Components like landing gear and structural rings benefit from the improved durability and performance characteristics provided by ring forging.
Automotive Industry
- Drive Shafts: Automotive drive shafts made using ring rolling forging exhibit enhanced strength and resistance to torsional stress.
- Wheel Hubs: Ring rolling forging is used to create durable and lightweight wheel hubs that improve vehicle performance.
Oil and Gas Industry
- Drill Components: Components like drill collars and subs are forged using ring rolling techniques to withstand extreme operational conditions.
- Flanges: High-strength flanges used in pipelines benefit from the uniform grain structure achieved through ring rolling forging.
Technological Advancements in Ring Rolling Forging
Recent technological advancements have significantly enhanced the efficiency and capabilities of ring rolling forging processes. These innovations include:
Computer Numerical Control (CNC) Systems
CNC systems enable precise control over the rolling process, improving the accuracy and consistency of forged components. This technology allows for complex geometries and tight tolerances.
Advanced Materials
The development of new alloy compositions and heat treatments has expanded the range of materials that can be effectively forged using ring rolling techniques. These advancements contribute to better performance and longevity of forged components.
Automation and Robotics
Automation and robotics are increasingly being integrated into ring forging processes. Automated systems enhance production speed, reduce labor costs, and improve safety by minimizing manual intervention.
Benefits of Ring Rolling Forging
Ring rolling forging offers numerous benefits that make it a preferred choice for many manufacturing applications. Some key benefits include:
- Enhanced Strength and Durability: The process results in components with superior mechanical properties, making them more resistant to wear and fatigue.
- Uniform Properties: The controlled rolling process ensures consistent material properties throughout the component, leading to reliable performance.
- Reduced Residual Stresses: Ring forging minimizes the introduction of residual stresses compared to other forging methods, reducing the likelihood of component failure.
- Improved Surface Finish: The process produces components with a smooth surface finish, reducing the need for additional machining and finishing operations.
Ring Rolling Forging Process Overview
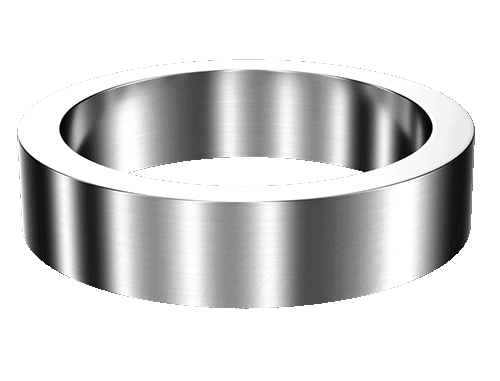
To better understand the ring forging process, the following table provides an overview of the key stages involved:
Stage | Description |
---|---|
Billet Preparation | Metal billets are preheated to a suitable temperature for forging. |
Initial Rolling | The billet is placed between rotating rolls and subjected to initial rolling. |
Ring Formation | The metal expands radially and contracts axially to form a ring shape. |
Secondary Rolling | Additional rolling may be performed to achieve precise dimensions. |
Heat Treatment | The forged ring may undergo heat treatment to enhance its properties. |
Final Inspection | The finished component is inspected for quality and dimensional accuracy. |
Conclusion
Ring rolling forging stands out as a vital manufacturing process that significantly enhances the strength and durability of metal components. Its benefits, including improved mechanical properties, reduced material waste, and cost-effectiveness, make it a preferred choice across various industries. With ongoing technological advancements, ring rolling forging continues to evolve, offering even greater precision and efficiency. By understanding and leveraging the capabilities of this process, manufacturers can produce high-quality components that meet the demanding requirements of modern applications.
FAQ
What metals are commonly used in ring rolling forging?
Ring rolling forging can be used with a wide range of metals, including carbon steel, alloy steel, stainless steel, aluminum, and titanium.
How does ring forging compare to other forging methods?
Ring forging offers superior mechanical properties, reduced material waste, and a more efficient production process compared to traditional forging methods.
What are the typical applications of ring rolling forged components?
Common applications include aerospace engine parts, automotive drive shafts, oil and gas drill components, and structural components in various industries.
How does ring rolling forging improve the mechanical properties of components?
The process aligns the grain structure of the metal, enhancing its strength, fatigue resistance, and overall durability.
What are the recent advancements in ring rolling forging technology?
Recent advancements include the integration of CNC systems, the development of advanced materials, and the use of automation and robotics to improve precision and efficiency.