Shandong Qilu lndustrial Co.,Ltd.
Ring Forging: A Comprehensive Overview
Welcome to My Blog!
Before we dive into the content, I’d love for you to join me on my social media platforms where I share more insights, engage with the community, and post updates. Here’s how you can connect with me:
Facebook:https://www.facebook.com/profile.php?id=100090903441806
Now, let’s get started on our journey together. I hope you find the content here insightful, engaging, and valuable.
Introduction
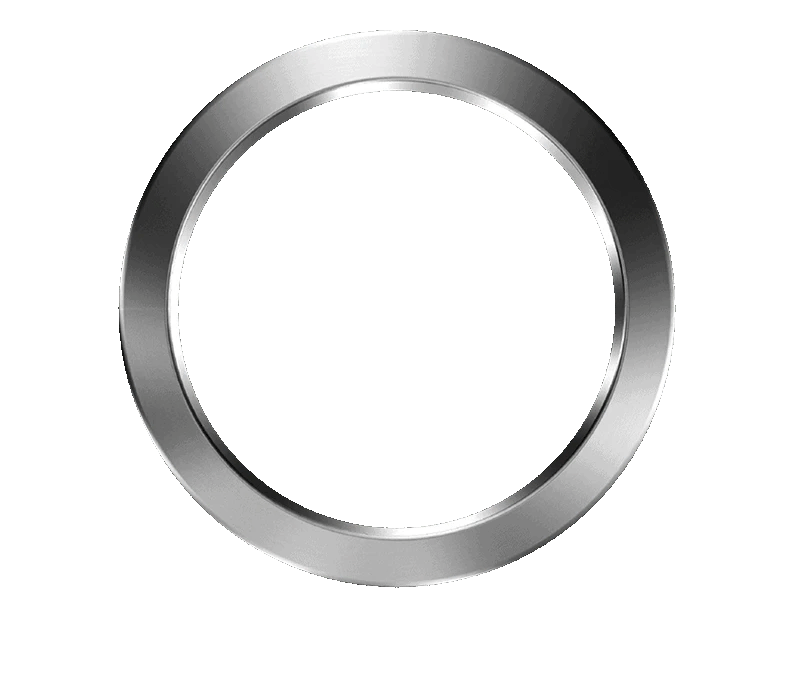
Ring forging is a specialized metalworking process that involves shaping a cylindrical workpiece into a ring or annular component. This technique is widely employed across diverse industries, including automotive, aerospace, and manufacturing, to produce a wide array of products. These products range from simple components like bearings and gears to complex parts like turbine blades and valve bodies. The process involves subjecting a heated metal billet to precise forging forces, resulting in a high-quality, high-performance ring.
Understanding the Ring Forging Process
The ring forge process typically involves several key steps:
- Heating: The cylindrical workpiece is heated to a specific temperature, often within a controlled furnace. This heating process enhances the metal’s ductility, making it more malleable and easier to shape.
- Forging: The heated workpiece is then placed between specialized forging dies, which are designed to impart the desired shape and dimensions to the metal. The forging press applies immense force to the workpiece, compressing and shaping it into a ring.
- Trimming: Once the ring has been formed, any excess material is removed through a trimming operation, ensuring precise dimensions and a clean finish.
- Heat Treatment: In many cases, the forged ring undergoes heat treatment processes, such as annealing, quenching, and tempering. These processes modify the metal’s microstructure, enhancing its mechanical properties like strength, hardness, and ductility.
Advantages of Ring Forging
Ring forging offers several significant advantages over other manufacturing methods, making it a preferred choice for many applications:
- Superior Mechanical Properties: The forging process refines the metal’s grain structure, resulting in enhanced strength, toughness, and fatigue resistance compared to cast or machined components.
- Reduced Material Waste: Ring forge is a highly efficient process that minimizes material waste, as the metal is shaped directly into the desired form.
- Complex Shape Capabilities: Ring forge can produce intricate shapes and geometries, including those with varying wall thicknesses and internal features.
- High Production Rates: Modern forging presses are capable of high production rates, making ring forging a cost-effective solution for large-scale manufacturing.
- Improved Surface Finish: Forging can produce a relatively good surface finish, often eliminating the need for extensive machining operations.
Applications of Ring Forging
The versatility of ring forging makes it suitable for a wide range of applications across various industries:
- Automotive: Ring forging is extensively used to produce critical components like bearings, gears, piston rings, and valve bodies.
- Aerospace: The aerospace industry relies on ring forge for components such as turbine blades, compressor discs, and landing gear parts, where high strength and reliability are paramount.
- Manufacturing: Ring forging is employed in the manufacturing of a variety of products, including pipe fittings, couplings, bushings, and other mechanical components.
- Energy: The energy sector utilizes ring forges for components like valve bodies, pump shafts, and turbine rotors, which operate under demanding conditions.
Types of Ring Forging
There are two primary types of ring forging processes:
- Radial Forging: In radial forging, the workpiece is compressed radially inward by two forging dies, forming a ring shape.
- Axial Forging: In axial forging, the workpiece is compressed axially between two dies, causing it to flow outward and form a ring.
Ring Forging Equipment
Ring forging is performed on specialized forging presses, which can be categorized as follows:
- Mechanical Presses: These presses utilize mechanical energy, such as flywheel and crank mechanisms, to generate the forging force.
- Hydraulic Presses: Hydraulic presses employ hydraulic fluid to exert the necessary force for shaping the workpiece.
- Screw Presses: Screw presses use a rotating screw to apply pressure to the workpiece, gradually forming the ring shape.
Material Selection for Ring Forging
The choice of material for ring forging depends on the specific application and the desired properties of the final product. Common materials used in ring forge include:
- Steel: Carbon steel, alloy steel, and stainless steel are widely used due to their high strength and durability.
- Aluminum Alloys: Aluminum alloys offer a good balance of strength and weight, making them suitable for various applications.
- Titanium Alloys: Titanium alloys possess excellent corrosion resistance and high strength-to-weight ratio, making them ideal for aerospace and medical applications.
- Nickel-Based Alloys: Nickel-based alloys, such as Inconel and Monel, offer exceptional high-temperature strength and corrosion resistance.
Comparison of Ring Forging and Other Manufacturing Processes
Feature | Ring Forging | Machining | Casting |
---|---|---|---|
Material Efficiency | High | Low | Moderate |
Strength and Toughness | High | Moderate | Moderate |
Complexity of Shapes | High | Moderate | High |
Production Rate | High | Moderate | Moderate |
Surface Finish | Good | Excellent | Varies |
Quality Control in Ring Forging
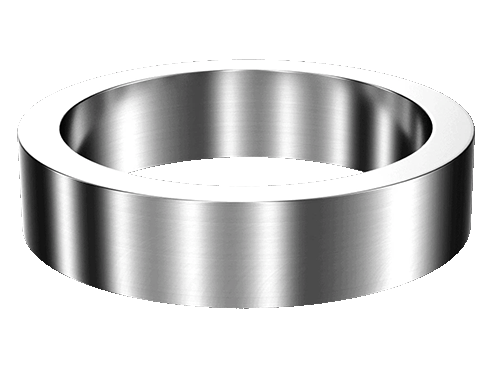
To ensure the production of high-quality ring forges, rigorous quality control measures are implemented throughout the process:
- Material Inspection: Incoming materials are thoroughly inspected to verify their composition, mechanical properties, and conformity to specifications.
- Process Monitoring: The forging process is closely monitored to ensure that it adheres to the specified parameters, such as temperature, pressure, and die alignment.
- Dimensional Inspection: The dimensions of the forged rings are precisely measured to verify that they meet the required tolerances.
- Non-destructive Testing: Non-destructive testing techniques, such as ultrasonic testing, radiography, and magnetic particle inspection, are employed to detect any internal defects or flaws in the forged rings.
- Metallurgical Analysis: Metallurgical analysis is conducted to assess the microstructure and mechanical properties of the forged rings, ensuring that they meet the required standards.
Conclusion
Ring forging is a versatile and efficient manufacturing process that offers numerous advantages over other methods. By understanding the fundamental principles, available equipment, and quality control considerations, manufacturers can effectively leverage ring forge to produce high-quality, high-performance components for a wide range of applications.
FAQ
What are the main advantages of ring forging?
Ring forging offers several advantages, including improved mechanical properties, reduced material waste, the ability to produce complex shapes, high production rates, and a relatively good surface finish.
What are the different types of ring forge?
The two primary types of ring forge are radial forging and axial forging.
What materials are commonly used in ring forging?
Common materials used in ring forging include steel, aluminum alloys, titanium alloys, and nickel-based alloys.
How does ring forge compare to other manufacturing processes?
Compared to machining and casting, ring forge offers superior mechanical properties, higher material efficiency, and the ability to produce complex shapes.
What are the key factors to consider when selecting a ring forging process?
Key factors to consider include the desired shape and size of the ring, the required material properties, the production volume, and the available equipment and expertise.