Shandong Qilu lndustrial Co.,Ltd.
Precision with Impression Die Forging: Benefits & Applications
Welcome to My Blog!
Before we dive into the content, I’d love for you to join me on my social media platforms where I share more insights, engage with the community, and post updates. Here’s how you can connect with me:
Facebook:https://www.facebook.com/profile.php?id=100090903441806
Now, let’s get started on our journey together. I hope you find the content here insightful, engaging, and valuable.
Introduction
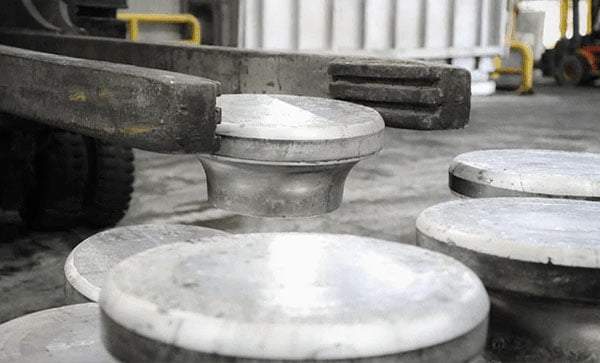
Impression die forging is a sophisticated metalworking technique that involves shaping metal by applying pressure between a male and female die. This process is widely utilized in various industries due to its exceptional ability to produce complex shapes with remarkable dimensional accuracy and a superior surface finish. In this comprehensive blog post, we will delve into the intricacies of impression die forging, exploring its numerous benefits, diverse applications, and the key factors that contribute to its success.
Understanding Impression Die Forging
Impression die forging is a specialized type of closed-die forging where both the upper and lower dies contain a complete impression of the desired final part. This precise alignment ensures that the workpiece conforms to the exact shape of the die cavity, resulting in highly accurate and consistent components. The process typically involves several key stages:
- Heating: The metal billet is heated to a specific temperature, known as the forging temperature, to enhance its plasticity and make it more malleable.
- Placement: The heated billet is carefully positioned between the dies, ensuring proper alignment.
- Forging: A powerful press applies force to the dies, causing the metal to flow and fill the die cavity, taking on the desired shape.
- Trimming: Any excess material is trimmed away, leaving the final part with the desired dimensions and shape.
Benefits of Impression Die Forging
Impression die forging offers a multitude of advantages that make it a preferred choice for many manufacturing applications:
- Exceptional Precision: The closed-die configuration ensures remarkable dimensional accuracy and consistency, making it ideal for components requiring tight tolerances.
- Superior Surface Finish: The smooth surfaces of the dies result in a fine and uniform surface finish on the forged part, eliminating the need for additional finishing processes.
- Enhanced Mechanical Properties: The forging process improves the mechanical properties of the metal, such as strength, toughness, and ductility, making the components more durable and reliable.
- Complex Shape Capabilities: Impression die forging can produce intricate shapes and features that would be difficult or impossible to achieve with other manufacturing methods, offering greater design flexibility.
- Material Efficiency: The process minimizes material waste by forcing the metal to conform to the die cavity, resulting in higher material utilization and reduced costs.
Applications of Impression Die Forging
Impression die forging finds widespread applications in a variety of industries, including:
- Automotive: Crankshafts, connecting rods, gears, and other critical engine components.
- Aerospace: Turbine blades, landing gear components, and structural parts for aircraft and spacecraft.
- Medical: Implants, surgical instruments, and orthopedic devices that require precision and biocompatibility.
- General Engineering: Automotive components, machinery parts, hand tools, and other industrial products.
Materials Suitable for Impression Die Forging
A wide range of metals can be effectively forged using impression dies, including:
- Steel: Carbon steel, alloy steel, stainless steel.
- Aluminum: Aluminum alloys.
- Copper: Copper alloys.
- Titanium: Titanium alloys.
- Nickel-based alloys: Inconel, Monel.
Comparison of Impression Die Forging with Other Processes
Feature | Impression Die Forging | Other Forging Processes (e.g., Open Die) |
---|---|---|
Precision | High | Moderate |
Surface Finish | Fine | Rougher |
Complexity of Shapes | Complex | Simpler |
Material Efficiency | High | Lower |
Cost | Higher tooling cost, lower per-part cost | Lower tooling cost, higher per-part cost |
Factors Affecting Impression Die Forging
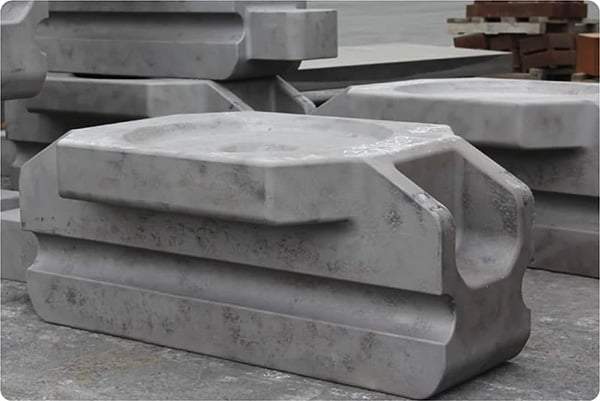
Several key factors influence the success of impression die forging, including:
- Die Design: The design of the dies is critical for achieving the desired part geometry, surface finish, and mechanical properties. Careful consideration must be given to factors such as draft angles, parting lines, and material flow patterns.
- Heating: The appropriate heating temperature is essential for ensuring optimal material flow and plasticity. Heating equipment must be capable of achieving and maintaining the desired temperature range.
- Press Capacity: The press must be capable of exerting sufficient force to shape the metal and fill the die cavity completely. The press capacity should be selected based on the size and material of the workpiece.
- Lubrication: Proper lubrication is crucial for reducing friction and wear on the dies and workpiece, ensuring a smooth forging process and preventing defects.
- Material Properties: The properties of the metal being forged, such as its composition and temperature, can affect the forging process and the quality of the final part.
Conclusion
Impression die forging is a versatile and precise manufacturing process that offers numerous benefits. Its ability to produce complex shapes with exceptional dimensional accuracy and surface finish makes it an ideal choice for a wide range of applications. By carefully considering factors such as die design, heating, press capacity, and lubrication, manufacturers can leverage impression die forging to create high-quality components with improved performance and efficiency.
FAQ
What is the difference between impression die forging and open die forging?
Impression die forging uses both a male and female die to shape the metal, while open die forging uses only one die.
How is the die material selected for impression die forging?
The die material is selected based on the properties of the metal being forged, the required die life, and the cost.
What are the common defects associated with impression die forging?
Common defects include flash, cracks, and dimensional variations.
How can the dimensional accuracy of forged parts be improved?
Dimensional accuracy can be improved by using high-precision dies, controlling the forging temperature, and using proper lubrication.