Shandong Qilu lndustrial Co.,Ltd.
How to Choose the Right Forge Metals for Your Project
Welcome to My Blog!
Before we dive into the content, I’d love for you to join me on my social media platforms where I share more insights, engage with the community, and post updates. Here’s how you can connect with me:
Facebook:https://www.facebook.com/profile.php?id=100090903441806
Now, let’s get started on our journey together. I hope you find the content here insightful, engaging, and valuable.
Introduction
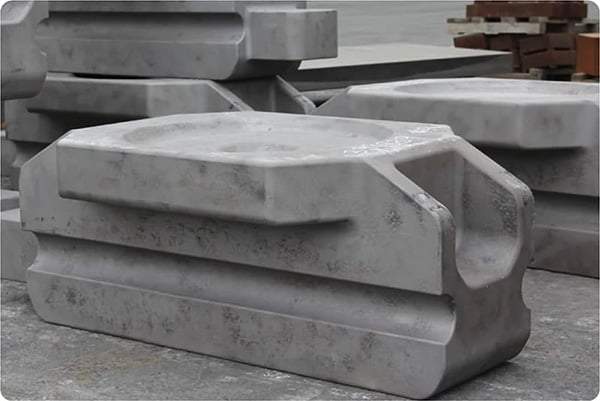
Choosing the right forge metals is crucial for the success of any metalworking project. Forge metals, which include various types of steel and alloys, are utilized in a wide range of applications—from industrial machinery to artistic creations. This blog will provide a comprehensive guide to selecting the appropriate forge metal for your project, exploring the properties, applications, and considerations that influence this critical decision.
What Are Forge Metals?
Forge metals refer to metals that are manipulated through forging, a process that involves shaping metal using compressive forces. This method enhances the material’s strength and durability. Common types of forge metal include:
- Carbon Steel: Known for its strength and versatility, often used in structural applications.
- Alloy Steel: Steel combined with other elements to enhance specific properties.
- Stainless Steel: Highly resistant to corrosion and staining, ideal for applications requiring hygiene.
- Tool Steel: Designed for making tools, known for its hardness and resistance to deformation.
Common Types of Forge Metals
Type | Characteristics | Common Applications |
---|---|---|
Carbon Steel | Strong, versatile, affordable | Structural components |
Alloy Steel | Enhanced properties, durable | Automotive parts, machinery |
Stainless Steel | Corrosion-resistant, hygienic | Kitchen equipment, medical tools |
Tool Steel | Hard, wear-resistant | Cutting tools, dies |
Factors to Consider When Choosing Forge Metals
When selecting forge metals for your project, several factors must be taken into account to ensure the best outcome. These factors include:
Project Requirements
Identify the specific requirements of your project, including load-bearing capacity, environmental conditions, and any industry-specific standards. Understanding these parameters will help narrow down your options.
Mechanical Properties
Different forge metal have varying mechanical properties such as tensile strength, hardness, ductility, and impact resistance. Consider the mechanical properties needed for your application:
- Tensile Strength: The maximum stress a material can withstand while being stretched or pulled.
- Hardness: A measure of a material’s resistance to deformation.
- Ductility: The ability of a material to deform under tensile stress.
Corrosion Resistance
For projects exposed to moisture or corrosive environments, selecting a metal with high corrosion resistance is essential. Stainless steel is often the go-to choice in such scenarios due to its chromium content, which provides a protective layer against corrosion.
Cost
Budget constraints play a significant role in the selection of forge metals. While high-performance alloys may offer enhanced properties, they often come with a higher price tag. Balancing cost and performance is vital for project feasibility.
Availability
Check the availability of the forge metals you are considering. Some specialized alloys may have limited availability, which could affect your project timeline. Working with suppliers who can provide the required materials promptly is essential.
Fabrication Process
Different forge metals may require specific fabrication processes. Understanding how your chosen metal will be worked—whether through traditional forging, machining, or welding—can help you make an informed decision.
Environmental Impact
Consider the environmental implications of your metal choice. Some metals are more eco-friendly than others in terms of sourcing and recycling. Choosing sustainable forge metal can enhance the overall responsibility of your project.
Factors to Consider When Choosing Forge Metals
Factor | Consideration |
---|---|
Project Requirements | Load capacity, environmental conditions |
Mechanical Properties | Tensile strength, hardness, ductility |
Corrosion Resistance | Resistance to moisture and chemicals |
Cost | Budget constraints and material pricing |
Availability | Timeliness and accessibility of materials |
Fabrication Process | Compatibility with forging, machining, welding |
Environmental Impact | Sustainability and recycling considerations |
Applications of Forge Metals
Forge metals are used in various industries and applications. Understanding where and how these metals are applied can guide your selection process.
Construction
In construction, forge metals such as carbon steel are commonly used for structural components, beams, and reinforcements. Their strength and durability make them ideal for load-bearing applications.
Automotive
The automotive industry relies heavily on alloy steels for components like gears, axles, and frames. These materials provide the necessary strength while being lightweight.
Aerospace
Aerospace applications require forge metal that can withstand extreme conditions. High-strength alloys and titanium are commonly used for components that must endure high stresses and temperatures.
Tool Making
Tool steels are specifically designed for creating tools, dies, and molds. Their hardness and resistance to wear make them ideal for cutting and shaping materials.
Medical Equipment
In the medical field, stainless steel is often used for surgical instruments and equipment due to its corrosion resistance and ease of sterilization.
How to Source Forge Metals
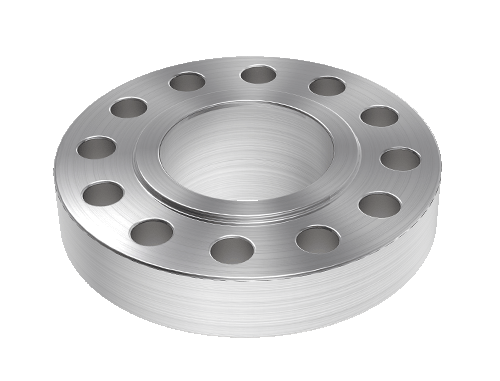
Sourcing the right forge metals involves a strategic approach. Here are some steps to consider:
Research Suppliers
Identify reliable suppliers who specialize in forge metals. Look for those with a good reputation, solid customer reviews, and a wide range of available materials.
Request Samples
Before making a bulk purchase, consider requesting samples of the forge metals you are considering. This allows you to assess the quality and suitability for your project.
Evaluate Technical Support
Choose suppliers that offer technical support and guidance. They can provide valuable insights into the best materials for your specific applications.
Assess Delivery Times
Ensure that the suppliers can meet your project timelines. Delays in obtaining forge metals can impact your project schedule.
Conclusion
Choosing the right forge metals for your project is a multifaceted decision that involves understanding project requirements, evaluating mechanical properties, and considering costs and availability. By taking into account the factors discussed in this blog, you can make informed choices that enhance the quality and success of your metalworking projects. Whether you’re working in construction, automotive, or any other industry, selecting the appropriate forge metals is essential for achieving your project goals.
FAQ
What are forge metals?
Forge metals are materials that are shaped through the forging process, enhancing their strength and durability. Common types include carbon steel, alloy steel, stainless steel, and tool steel.
Why is the selection of forge metals important?
The right forge metals directly impact the performance, durability, and cost-effectiveness of your project. Choosing unsuitable materials can lead to project failures or increased expenses.
How do I determine the best forge metal for my project?
Consider project requirements, mechanical properties, corrosion resistance, cost, availability, fabrication processes, and environmental impact to determine the best forge metal for your needs.
Are stainless steel and alloy steel the same?
No, while both are types of steel, stainless steel is specifically formulated to resist corrosion due to its chromium content, whereas alloy steel is combined with other elements to enhance certain properties.
Can I use carbon steel in outdoor applications?
While carbon steel is strong and versatile, it is susceptible to rust and corrosion when exposed to moisture. For outdoor applications, consider applying protective coatings or using corrosion-resistant materials.