Shandong Qilu lndustrial Co.,Ltd.
How Seamless Rolled Ring Forging Revolutionizes Manufacturing
Introduction
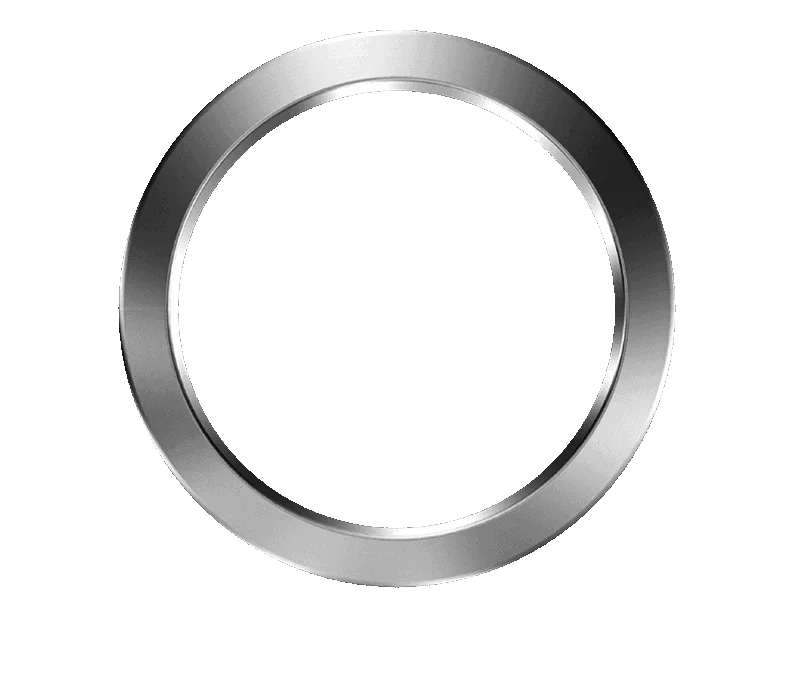
In the realm of manufacturing, innovations constantly drive efficiency and quality. One such innovation that has transformed various industries is seamless rolled ring forging. This process involves shaping metal into seamless rings with exceptional strength and reliability. In this blog, we’ll delve into the intricacies of ring forging, exploring its advantages, applications, and impact on modern manufacturing.
Understanding Seamless Rolled Ring Forging
Seamless rolled ring forging is a specialized metalworking process that produces seamless, circular components with superior mechanical properties. Unlike traditional methods like casting or welding, which may result in weaker points and seams, seamless ring forging ensures uniformity and strength throughout the entire ring. This process involves shaping heated metal billets using high pressure and controlled deformation within specialized forging equipment.
Advantages of Seamless Rolled Ring Forging
The adoption of seamless rolled ring forging offers numerous advantages for manufacturers across various sectors:
- Superior Strength: The absence of seams and grain flow optimization during forging results in superior mechanical properties, including enhanced strength, toughness, and fatigue resistance.
- Cost Efficiency: While initial setup costs may be higher compared to other methods, seamless ring forging often proves more cost-effective in the long run due to reduced material waste, minimal machining requirements, and extended component lifespan.
- Versatility: Seamless ring forging can produce a wide range of shapes and sizes, catering to diverse industrial applications such as gears, bearings, flanges, and structural components.
- Enhanced Material Properties: The forging process refines the microstructure of the metal, eliminating defects and improving material integrity, leading to better performance under demanding conditions.
- Customization: Manufacturers can tailor the properties of forged rings to meet specific requirements, including alloy selection, heat treatment, and dimensional accuracy.
Applications of Seamless Rolled Ring Forging
Seamless ring forging finds extensive application across industries such as aerospace, automotive, oil and gas, power generation, and heavy machinery. Some common applications include:
- Aerospace: Jet engine components, landing gear bearings, structural components.
- Automotive: Transmission gears, drivetrain components, wheel bearings.
- Oil and Gas: Flanges, wellhead components, valves.
- Power Generation: Turbine shafts, generator rings, gearbox components.
- Heavy Machinery: Slewing bearings, gear blanks, crane components.
Impact on Modern Manufacturing
The widespread adoption of seamless rolled ring forging has revolutionized modern manufacturing in several ways:
- Improved Product Performance: Components produced through this process exhibit superior mechanical properties, contributing to the reliability and performance of end products.
- Streamlined Production Processes: By reducing the need for secondary machining operations and assembly, seamless rolled ring forging streamlines the manufacturing process, saving time and resources.
- Increased Sustainability: The efficiency and material utilization inherent in seamless ring forging align with sustainability goals, minimizing waste and energy consumption.
- Enhanced Competitiveness: Manufacturers leveraging this advanced forging technique gain a competitive edge by offering high-quality, reliable components to their customers.
Comparison of Forging Methods
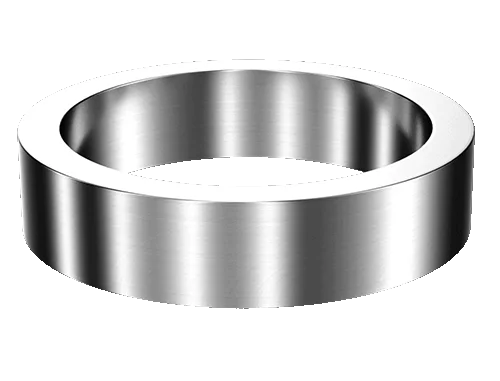
Criteria | Seamless Rolled Ring Forging | Open-Die Forging | Closed-Die Forging |
---|---|---|---|
Mechanical Properties | Superior | Variable | Variable |
Dimensional Accuracy | High | Moderate | High |
Material Waste | Low | Moderate | Low |
Secondary Machining Required | Minimal | Often required | Often required |
Setup Costs | Moderate to High | Moderate | High |
Versatility | High | Moderate | Low |
FAQ
Q:Is seamless rolled ring forging suitable for all metals?
A:While seamless rolled ring forging is commonly associated with steel and alloy steels, it can also be applied to various metals such as titanium, aluminum, and nickel-based alloys, depending on the specific requirements of the application.
Q:What are the size limitations of seamless rolled ring forging?
A:Seamless ring forging can accommodate a wide range of sizes, from small bearings to large, heavy-duty components used in industrial machinery. The size limitations are primarily determined by the capacity of the forging equipment and the material properties.
Q:How does seamless rolled ring forging compare to other forging methods?
A:Unlike open-die or closed-die forging, seamless rolled ring forging produces rings without seams, offering superior mechanical properties and dimensional accuracy. Additionally, it eliminates the need for machining operations typically required to remove seam defects.
Conclusion
Seamless rolled ring forging stands as a testament to the ingenuity and precision of modern manufacturing techniques. Its ability to produce seamless, high-strength rings with exceptional reliability has transformed various industries, from aerospace to heavy machinery. As technology continues to advance, seamless rolled ring forging will undoubtedly remain a cornerstone of efficient and sustainable manufacturing processes.