Shandong Qilu lndustrial Co.,Ltd.
How Roll Forging Revolutionizes Metalworking Processes
Introduction
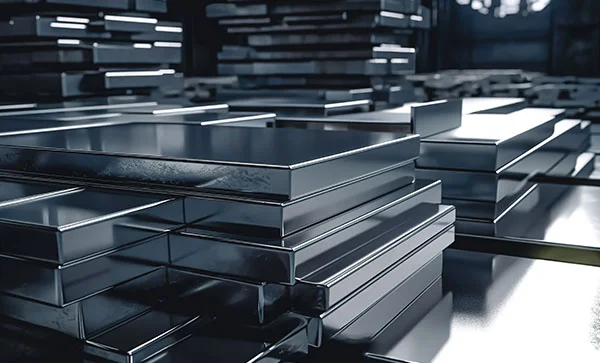
In the realm of metalworking, innovation is the key to progress. One such groundbreaking technique that has significantly impacted the industry is roll forging. In this blog post, we delve into the intricacies of roll forg, its advantages, applications, and how it has revolutionized metalworking processes.
Understanding Roll Forging
Roll forg, also known as cross-wedge rolling, is a metalworking process that involves shaping metal by applying compressive forces through rotating rolls. This process is highly versatile and can be utilized for various metals, including steel, aluminum, and titanium. By subjecting the metal to high pressure between rotating rolls, roll forg produces components with superior strength, durability, and dimensional accuracy compared to traditional forging methods.
Advantages of Roll Forging
- Enhanced Mechanical Properties: Roll forg results in a refined grain structure, leading to improved mechanical properties such as strength and fatigue resistance.
- Cost Efficiency: Compared to other forging methods, roll forg offers higher production rates and lower tooling costs, making it a cost-effective solution for mass production.
- Material Savings: The precise nature of roll forg minimizes material waste, contributing to sustainable manufacturing practices.
- Complex Geometries: Roll forg allows for the production of components with intricate shapes and complex geometries, expanding the design possibilities for engineers.
- Improved Surface Finish: The rolling action of the rolls produces a smooth surface finish, reducing the need for additional machining operations.
Applications of Roll Forging
Roll forg finds extensive applications across various industries, including automotive, aerospace, and manufacturing. Some common applications include:
- Automotive Components: Roll-forged parts such as crankshafts, connecting rods, and gears are widely used in the automotive industry due to their high strength and reliability.
- Aerospace Components: Critical aerospace components like turbine blades, landing gear parts, and structural components benefit from the superior mechanical properties achieved through roll forging.
- Industrial Machinery: Roll-forged components are integral to the construction of heavy machinery, industrial equipment, and power generation systems, where durability and performance are paramount.
Roll Forging Process
The roll forging process involves several key steps:
- Billet Heating: The metal billet is heated to an optimal temperature to facilitate deformation.
- Preforming: The heated billet is preformed into a preliminary shape, typically using dies or preforms.
- Rolling Operation: The preformed billet is passed between rotating rolls, where it undergoes plastic deformation to achieve the desired final shape.
- Trimming and Finishing: Excess material is trimmed, and the forged component undergoes finishing operations to meet dimensional tolerances and surface finish requirements.
Case Study: Roll-Forged Crankshaft
As an example of roll forg’s efficacy, let’s consider the production of a crankshaft for automotive engines. A crankshaft is a vital component that converts reciprocating motion into rotational motion in an engine. By utilizing roll forg, manufacturers can produce crankshafts with exceptional strength, fatigue resistance, and dimensional accuracy. The precise control over grain flow and geometry afforded by roll forg ensures that the crankshaft meets the stringent performance requirements of modern engines while minimizing material waste and production costs.
Mechanical properties of roll forged steel compared to conventional forged steel
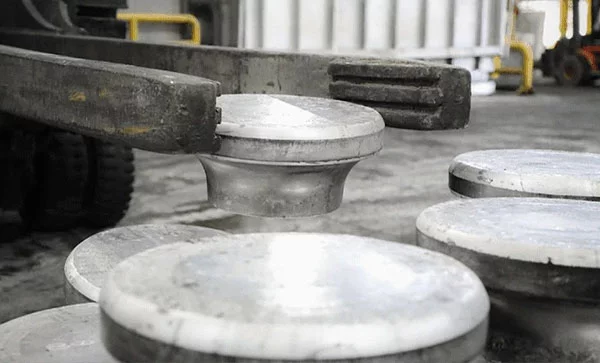
Mechanical Property | Roll Forged Steel | Conventionally Forged Steel |
---|---|---|
Tensile Strength (MPa) | 900 | 800 |
Yield Strength (MPa) | 800 | 700 |
Elongation (%) | 15 | 10 |
Hardness (HRC) | 45 | 40 |
Conclusion
In conclusion, roll forging stands as a testament to the continuous evolution of metalworking processes. Its ability to enhance mechanical properties, reduce costs, and enable the production of complex components has made it a cornerstone of modern manufacturing. As industries continue to demand higher performance and efficiency from metal components, roll forging will undoubtedly remain at the forefront of innovation, shaping the future of metalworking.
FAQ
Q: Is roll forging suitable for all types of metals?
A: While roll forg is compatible with various metals, including steel, aluminum, and titanium, the suitability depends on factors such as material properties and application requirements.
Q: How does roll forg compare to other forging methods?
A: Roll forg offers advantages such as enhanced mechanical properties, cost efficiency, and material savings compared to traditional forging methods like open-die forging or closed-die forging.
Q: Can roll forging produce components with intricate shapes?
A: Yes, roll forging can produce components with complex geometries, thanks to its ability to exert precise pressure and deformation on the metal during the rolling process.
Q: What industries benefit the most from roll forg?
A: Industries such as automotive, aerospace, and industrial machinery benefit significantly from roll forging due to its ability to produce high-strength, reliable components efficiently.
Q: Is roll forging environmentally friendly?
A: Roll forging can contribute to sustainable manufacturing practices by minimizing material waste and energy consumption compared to other metalworking processes.