Shandong Qilu lndustrial Co.,Ltd.
How Ring Forgings Improve Performance in Heavy Machinery
Welcome to My Blog!
Before we dive into the content, I’d love for you to join me on my social media platforms where I share more insights, engage with the community, and post updates. Here’s how you can connect with me:
Facebook:https://www.facebook.com/profile.php?id=100090903441806
Now, let’s get started on our journey together. I hope you find the content here insightful, engaging, and valuable.
Introduction
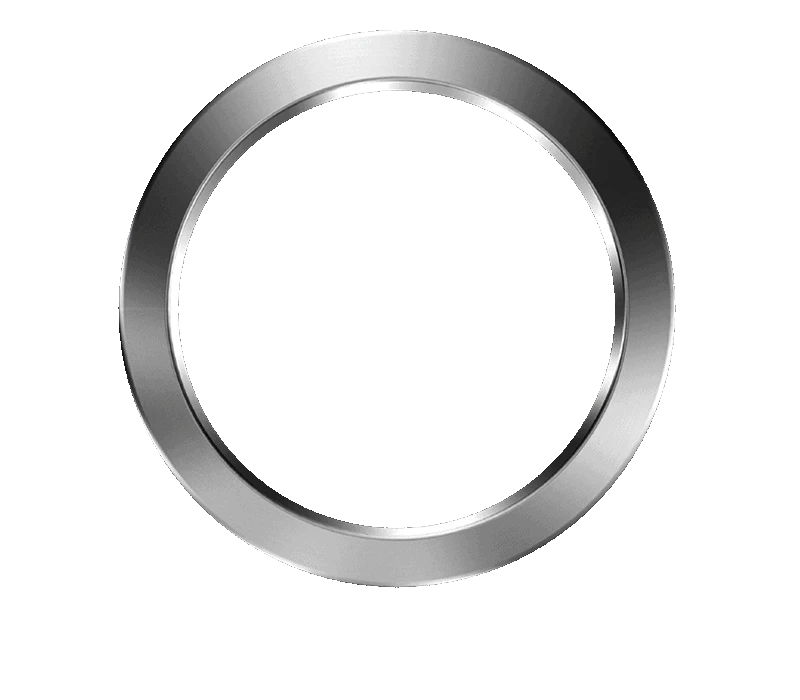
In the world of heavy machinery, performance, durability, and reliability are paramount. As machinery operates under intense conditions, the components used must be designed to withstand high stresses and severe operational demands. One such critical component is the ring forging. Ring forgings are essential in various heavy machinery applications due to their ability to enhance performance and longevity. This blog explores how ring forging improve performance in heavy machinery, detailing their benefits, applications, and best practices.
What Are Ring Forgings?
Definition and Process
Ring forgings are a specific type of forged metal component characterized by their ring-like shape. The forging process involves heating a metal billet until it becomes malleable and then shaping it under high pressure using a die or hammer. This process enhances the material’s strength and durability by refining its internal structure and eliminating any defects. Ring forging are used in applications where high strength, durability, and precision are required.
Characteristics of Ring Forgings
- Shape and Size: Typically circular or ring-shaped, designed to fit specific machinery components.
- Material: Commonly made from high-strength alloys such as steel, titanium, or aluminum.
- Forging Method: Includes open-die forging, closed-die forging, and ring rolling, depending on the required specifications and size.
Benefits of Ring Forgings in Heavy Machinery
Enhanced Strength and Durability
Ring forgings offer superior strength and durability compared to cast or machined components. The forging process aligns the grain structure of the metal, which enhances its mechanical properties. This results in components that can withstand high loads and stresses, making them ideal for heavy machinery applications. The improved strength-to-weight ratio also contributes to better performance and longevity of the machinery.
Improved Fatigue Resistance
In heavy machinery, components are often subjected to cyclic loads that can lead to fatigue failure. Ring forging are engineered to resist these cyclic stresses due to their uniform grain structure and superior material properties. This makes them less prone to cracking and other fatigue-related issues, thereby extending the service life of the machinery.
Precision and Reliability
Ring forgings are produced with high precision, ensuring that they meet the exact specifications required for their applications. This precision translates to better fit and alignment within machinery, leading to improved performance and reduced risk of malfunction. Reliable components are crucial in heavy machinery to maintain operational efficiency and safety.
Reduced Material Waste
The forging process is highly efficient, with minimal material waste compared to casting or machining. The process involves compressing a billet of metal into the desired shape, which maximizes the use of the material and reduces scrap. This not only makes the process more economical but also contributes to more sustainable manufacturing practices.
Superior Toughness
Ring forging exhibit exceptional toughness, which is crucial for components that experience high impact loads and harsh operational conditions. The forging process enhances the material’s ability to absorb and dissipate energy, reducing the likelihood of failure under extreme conditions. This toughness ensures reliable operation and safety in heavy machinery.
Applications of Ring Forgings in Heavy Machinery
Gear Rings
Gear rings are critical components in many types of heavy machinery, including excavators, bulldozers, and cranes. Ring forgings used for gear rings provide the strength and durability needed to handle the high torque and stress associated with gear operations. The precision of ring forgings ensures accurate meshing and smooth operation of gears.
Turbine Discs
In heavy machinery such as gas turbines and steam turbines, turbine discs must withstand extreme temperatures and stresses. Ring forgings are used to manufacture these discs, offering the necessary strength and thermal resistance. The superior mechanical properties of ring forgings ensure reliable performance and longevity of turbine components.
Rolling Mill Rolls
Rolling mills, used in metalworking industries, require rolls that can endure significant forces during the rolling process. Ring forgings are used to produce these rolls due to their high strength and resistance to wear. The durability of ring forging ensures consistent quality and performance of the rolled products.
Axle Components
Axle components in heavy machinery, such as trucks and construction equipment, are subjected to heavy loads and impact forces. Ring forgings provide the strength and toughness needed for these critical components. The reliability of ring forging in axle applications contributes to the overall performance and safety of the machinery.
Maintenance and Care for Ring Forgings
Regular Inspections
To ensure the continued performance of ring forgings, regular inspections are essential. Check for signs of wear, cracks, or deformation that may indicate potential issues. Early detection of problems can prevent more severe damage and ensure the reliability of the machinery.
Lubrication and Cleaning
Proper lubrication and cleaning of components involving ring forging help maintain their performance and longevity. Ensure that lubricants are applied as recommended by the manufacturer, and keep components clean to prevent contaminants from causing wear or damage.
Adherence to Manufacturer Specifications
Always adhere to the manufacturer’s specifications and maintenance guidelines for ring forgings. This includes following recommended operational limits, handling procedures, and maintenance schedules. Proper adherence ensures that ring forging perform optimally and have a longer service life.
Maintenance Checklist for Ring Forgings
Task | Frequency | Notes |
---|---|---|
Inspect for wear and damage | Monthly | Check for cracks, deformation, and other signs of wear |
Lubricate components | According to manufacturer’s recommendations | Use specified lubricants to ensure proper function |
Clean surfaces | As needed | Remove contaminants and debris to prevent wear |
Review operational limits | Quarterly | Ensure components are operating within recommended limits |
Document maintenance | Ongoing | Keep records of inspections, repairs, and maintenance activities |
Future Trends in Ring Forging Technology
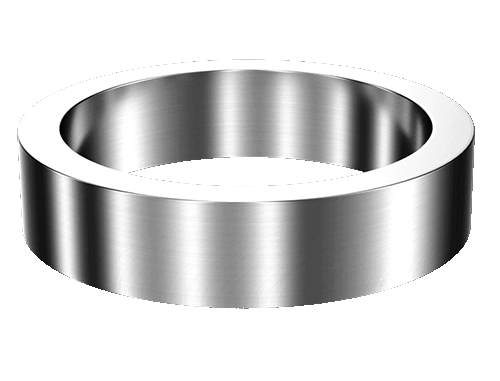
Advanced Materials
The development of advanced materials and alloys is a key trend in ring forging technology. New materials with enhanced properties, such as higher strength-to-weight ratios and improved corrosion resistance, are being explored. These advancements aim to further enhance the performance and durability of ring forgings.
Automation and Precision Engineering
Automation and precision engineering are transforming the forging process. Advanced forging technologies, such as robotic automation and computer-controlled systems, are improving the precision and consistency of ring forgings. These innovations lead to higher quality components and more efficient production processes.
Sustainable Practices
Sustainability is becoming increasingly important in manufacturing. The ring forging industry is exploring ways to reduce environmental impact through energy-efficient processes, recycling of materials, and sustainable sourcing practices. These efforts contribute to a more environmentally friendly approach to manufacturing.
Conclusion
Ring forgings play a crucial role in enhancing the performance and reliability of heavy machinery. Their superior strength, durability, and precision make them ideal for demanding applications in various industries. By understanding the benefits of ring forgings and implementing proper maintenance practices, manufacturers and operators can ensure optimal performance and longevity of their machinery. As technology continues to advance, ring forging will likely benefit from innovations in materials, automation, and sustainability, further improving their role in heavy machinery.
FAQ
What are the main benefits of using ring forgings in heavy machinery?
Ring forgings offer enhanced strength, improved fatigue resistance, precision, reduced material waste, and superior toughness. These benefits make them ideal for heavy machinery applications that require durability and reliability.
How does the forging process improve the properties of ring forgings?
The forging process refines the internal grain structure of the metal, eliminating defects and aligning the grains for greater strength and durability. This results in a component with superior mechanical properties compared to cast or machined parts.
What types of heavy machinery commonly use ring forgings?
Ring forgings are used in various types of heavy machinery, including gear rings, turbine discs, rolling mill rolls, and axle components. Their strength and precision make them suitable for critical components in these applications.
How should ring forgings be maintained?
Regular inspections, proper lubrication, cleaning, and adherence to manufacturer specifications are essential for maintaining ring forgings. Early detection of issues and following recommended maintenance practices help ensure optimal performance and longevity.
What are some future trends in ring forging technology?
Future trends include advancements in materials, automation, precision engineering, and sustainable practices. These innovations aim to enhance the performance, efficiency, and environmental impact of ring forgings.