Shandong Qilu lndustrial Co.,Ltd.
How NDT Systems Ensure Product Integrity
Introduction
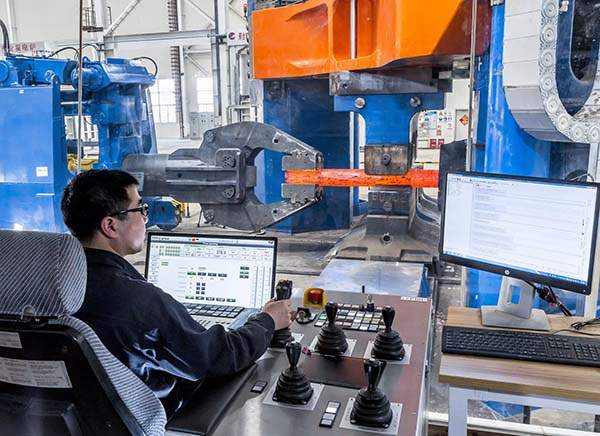
Non-Destructive Testing (NDT) systems play a crucial role in ensuring the integrity and quality of products across various industries. This article delves into the mechanisms and significance of NDT systems in maintaining product quality and safety.
Understanding NDT Systems
NDT system encompass a range of techniques designed to inspect materials and components without causing damage. These techniques include ultrasonic testing, radiographic testing, magnetic particle testing, liquid penetrant testing, and eddy current testing. Each method offers unique advantages and is tailored to specific applications.
Importance of Product Integrity
Product integrity is paramount across industries such as aerospace, automotive, manufacturing, and construction. Any compromise in integrity can lead to catastrophic consequences, including safety hazards, financial losses, and damage to reputation. NDT systems serve as a frontline defense by detecting defects, flaws, and irregularities early in the production process.
Applications of NDT Systems
NDT systems play a pivotal role across diverse stages of the product lifecycle, encompassing raw material inspection, in-process monitoring, and final product evaluation. The versatility of NDT techniques allows for comprehensive assessment, ensuring that products meet stringent quality standards and regulatory requirements.
Raw material inspection marks the initial phase where NDT system are employed to scrutinize incoming materials for any imperfections or irregularities. Whether it’s metals, polymers, composites, or other materials, NDT techniques such as ultrasonic testing, magnetic particle inspection, and eddy current testing can swiftly identify defects like cracks, inclusions, or inconsistencies in material composition. By intercepting issues at this early stage, manufacturers can preemptively address potential quality concerns, thus safeguarding the integrity of subsequent manufacturing processes.
In-process monitoring constitutes a critical checkpoint where NDT system facilitate real-time assessment of components as they undergo various manufacturing operations. For instance, in welding processes, ultrasonic testing can detect weld defects like porosity, lack of fusion, or incomplete penetration, ensuring weld quality and structural integrity. Similarly, eddy current testing can be employed during machining operations to monitor surface finish and detect surface cracks or defects. By integrating NDT into the production line, manufacturers can implement corrective measures promptly, minimizing scrap, rework, and production delays.
Advantages of NDT Systems
The adoption of NDT system offers numerous benefits to manufacturers, including improved quality control, enhanced safety, reduced downtime, and cost savings. By identifying potential issues before they escalate, NDT system help prevent costly rework, recalls, and liability claims.
Case Studies
To illustrate the effectiveness of NDT systems, let’s examine a few real-world scenarios:
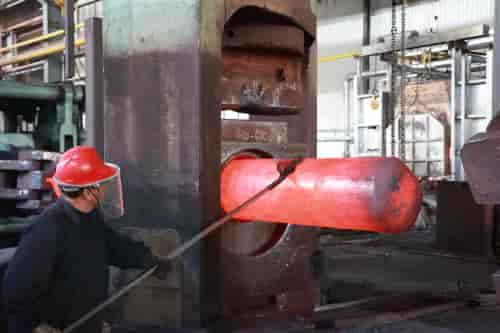
Industry | Application | NDT Technique | Result |
---|---|---|---|
Aerospace | Wing Inspection | Ultrasonic Testing | Detected hidden defects, preventing potential failure during flight. |
Automotive | Weld Quality Control | Radiographic Testing | Ensured structural integrity of welded components, meeting safety standards. |
Manufacturing | Casting Inspection | Magnetic Particle Testing | Identified surface cracks and inclusions, ensuring product reliability. |
Challenges and Innovations
Despite their effectiveness, NDT systems face challenges such as limited inspection access, complex geometries, and evolving materials. However, ongoing research and technological advancements, including robotics, artificial intelligence, and digital imaging, are expanding the capabilities of NDT systems, making inspections faster, more accurate, and versatile.
Conclusion
In conclusion, NDT systems are indispensable tools for maintaining product integrity across industries. By leveraging advanced techniques and technologies, these systems enable manufacturers to detect defects, ensure compliance, and deliver products of the highest quality and safety standards.
FAQ
Q: How do NDT systems differ from traditional testing methods?
A: Unlike traditional methods that may require destructive testing, NDT system allow for inspection without causing damage to the product, making them ideal for quality control and safety assessments.
Q: Are NDT systems suitable for all types of materials?
A: NDT system can be adapted to inspect a wide range of materials, including metals, plastics, composites, and ceramics, making them versatile across various industries.
Q: What are the regulatory standards governing NDT inspections?
A: Regulatory standards vary by industry and region. Common standards include those set by organizations such as ASTM International, ASME, and ISO, outlining specific requirements for NDT procedures and qualifications.
Q: How can I implement NDT systems in my manufacturing process?
A: Implementing NDT systems requires careful planning, investment in equipment and training, and integration into existing quality assurance processes. Consulting with NDT experts and equipment suppliers can help tailor solutions to specific needs.
With the increasing demand for high-quality, reliable products, the role of NDT systems in ensuring product integrity will continue to expand, driving innovation and advancements in inspection technologies.