Shandong Qilu lndustrial Co.,Ltd.
How Metals Forging Enhances Material Strength
Welcome to My Blog!
Before we dive into the content, I’d love for you to join me on my social media platforms where I share more insights, engage with the community, and post updates. Here’s how you can connect with me:
Facebook:https://www.facebook.com/profile.php?id=100090903441806
Now, let’s get started on our journey together. I hope you find the content here insightful, engaging, and valuable.
Introduction
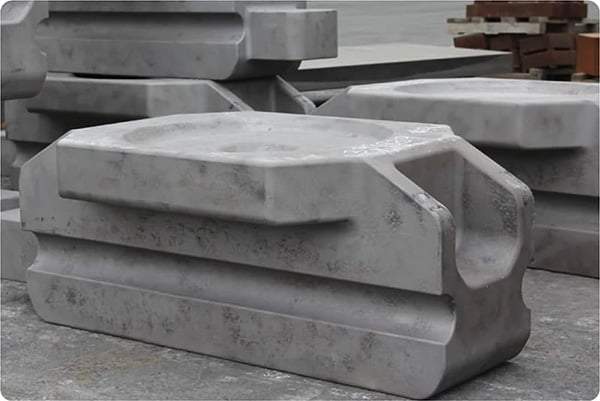
Metals forging is a crucial process in the manufacturing industry that significantly enhances the strength and durability of various metal components. This ancient technique, which dates back thousands of years, has evolved into a sophisticated method used across various sectors, including aerospace, automotive, and construction. In this blog, we will explore how metals forging improves material strength, the different types of forging processes, and their applications, providing a comprehensive understanding of this vital manufacturing technique.
Understanding Metals Forging
Metals forging is a manufacturing process that involves shaping metal using compressive forces. This can be accomplished through various methods, including hammering, pressing, or rolling. The primary goal of metals forging is to produce a material that is stronger and more reliable than its original form.
Key Processes in Metals Forging
- Open Die Forging: Involves shaping metal between two flat surfaces, allowing for greater flexibility in design.
- Closed Die Forging: Uses pre-shaped dies to produce more intricate shapes and dimensions with higher precision.
- Upset Forging: Involves increasing the diameter of a piece of metal while decreasing its length.
- Roll Forging: A continuous process that involves passing metal through rollers to achieve desired thickness and shape.
Forging Process | Description | Key Advantages |
---|---|---|
Open Die Forging | Metal is shaped between flat surfaces. | Flexibility in design, large parts possible |
Closed Die Forging | Metal is shaped using pre-formed dies. | High precision, complex shapes |
Upset Forging | Increases diameter while shortening length. | Efficient for specific shapes |
Roll Forging | Metal is passed through rollers. | Continuous process, uniform thickness |
How Metals Forging Enhances Material Strength
Grain Structure Improvement
One of the primary benefits of metals forging is the alteration of the metal’s grain structure. When metal is forged, the grains become elongated and aligned in the direction of the applied force. This alignment increases the overall strength of the material, making it more resistant to deformation and failure.
Elimination of Defects
The forging process helps eliminate defects that may exist in cast metals, such as porosity and inclusions. During forging, the intense pressure compacts the material, leading to a denser and more homogeneous structure. This quality makes forged parts significantly more reliable than their cast counterparts.
Enhanced Mechanical Properties
Metals forging enhances mechanical properties, such as yield strength, tensile strength, and toughness. The controlled deformation experienced during the forging process leads to a refined microstructure, which is essential for applications requiring high strength and durability.
Mechanical Property | Forged Metal | Cast Metal |
---|---|---|
Yield Strength | High | Moderate |
Tensile Strength | Very High | Low |
Toughness | Excellent | Fair |
Improved Fatigue Resistance
Forged metals exhibit superior fatigue resistance compared to non-forged materials. The directional grain structure created during the forging process allows the material to better withstand cyclic loading, making it ideal for applications in high-stress environments, such as aerospace and automotive components.
Applications of Metals Forging
Aerospace Industry
In the aerospace sector, components like turbine blades, landing gear, and structural elements are often made using metals forging due to their need for high strength and reliability. The ability to produce lightweight yet robust components is critical for aircraft performance.
Automotive Industry
The automotive industry relies heavily on forged components for parts such as crankshafts, connecting rods, and gears. These parts must endure significant mechanical stress and high temperatures, making the enhanced strength from metals forging essential.
Construction Sector
Forged steel is widely used in the construction industry for structural elements like beams and reinforcements. The durability and strength provided by metals forging contribute to the safety and longevity of buildings and bridges.
Economic Benefits of Metals Forging
The economic advantages of metals forging are substantial. While the initial investment in forging equipment can be high, the long-term benefits often outweigh the costs.
Reduced Material Waste
Metals forging processes generate less waste compared to casting and machining. This reduction in waste translates to lower material costs and environmental benefits.
Lower Production Costs
The durability and strength of forged parts mean they often require less maintenance and replacement. This longevity reduces the overall production costs over time.
Efficiency in Production
Forging processes can produce components more quickly than traditional machining methods. This efficiency leads to shorter lead times and increased productivity, providing a competitive edge for manufacturers.
Quality Control in Metals Forging
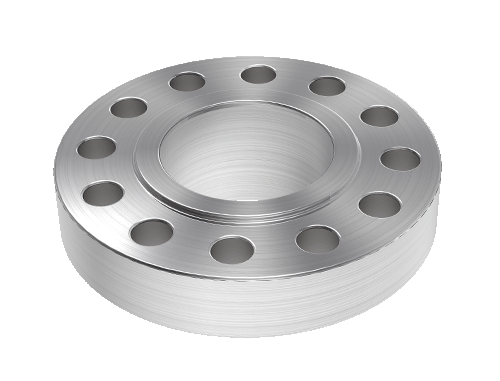
Ensuring the quality of forged products is critical. Manufacturers often implement strict quality control measures throughout the forging process. These include:
Material Inspection
Before forging, raw materials are thoroughly inspected for defects. This ensures that only high-quality materials are used in the forging process.
Process Monitoring
During forging, various parameters, such as temperature, pressure, and deformation rate, are monitored to ensure consistency and quality.
Post-Processing Testing
After forging, components undergo rigorous testing, including tensile tests, hardness tests, and non-destructive testing methods, to verify their mechanical properties.
Conclusion
Metals forging is an indispensable manufacturing process that significantly enhances material strength. By improving grain structure, eliminating defects, and enhancing mechanical properties, forging produces components that are more reliable and durable. With applications spanning various industries, the benefits of metals forging extend beyond strength to include economic advantages and quality control. As technology continues to advance, the role of forging in manufacturing will only become more critical.
FAQ
What is metals forging?
Metals forging is a manufacturing process that shapes metal using compressive forces, enhancing its strength and durability.
How does forging improve material strength?
Forging improves material strength by altering the grain structure, eliminating defects, and enhancing mechanical properties.
What are the different types of metals forging?
The main types include open die forging, closed die forging, upset forging, and roll forging.
What industries use forged components?
Industries such as aerospace, automotive, and construction extensively use forged components for their strength and reliability.
Is forged metal stronger than cast metal?
Yes, forged metal typically exhibits higher yield strength, tensile strength, and toughness compared to cast metal.