Shandong Qilu lndustrial Co.,Ltd.
How Hot Forging Enhances Metal Strength and Durability
Welcome to My Blog!
Before we dive into the content, I’d love for you to join me on my social media platforms where I share more insights, engage with the community, and post updates. Here’s how you can connect with me:
Facebook:https://www.facebook.com/profile.php?id=100090903441806
Now, let’s get started on our journey together. I hope you find the content here insightful, engaging, and valuable.
Introduction

In the world of metalworking, one process that stands out for its ability to improve the strength and durability of metals is hot forging. Whether you’re producing complex parts for industrial machinery, automotive components, or aerospace applications, hot forging plays a critical role in shaping metal and enhancing its properties. This blog will explore how hot forging works, why it’s so effective in improving metal strength, and how it compares to other processes. By the end, you’ll have a deep understanding of why hot forging is essential for high-quality metal products.
What is Hot Forging?
Hot forging is a metalworking process that involves shaping metal at elevated temperatures, usually above the recrystallization temperature, to enhance the material’s properties. The process includes applying compressive forces to the metal in its plastic state, causing it to flow and take the shape of the die or mold. This technique is often used to produce large quantities of parts that require excellent mechanical properties like strength, durability, and resistance to fatigue.
In heat forging, the heat allows the metal to become more malleable, making it easier to manipulate and shape. It also helps in refining the grain structure of the metal, contributing to a more uniform distribution of material properties throughout the part.
The Process of Hot Forging
The process of heat forging typically involves several steps, which are outlined below:
Heating: The metal is heated to a temperature where it becomes soft enough to deform under pressure. This is usually achieved in a furnace or using induction heating.
Forging: Once the metal reaches the optimal temperature, it is transferred to a press or hammer, where the desired shape is formed. The compressive forces applied during this step break down any existing metal grains and form new ones.
Cooling: After forging, the part is gradually cooled to room temperature. This cooling process is carefully controlled to avoid cracking or warping, and in some cases, it is followed by a heat treatment process.
Finishing: The forged part may undergo further machining or surface treatments to meet specific design and functional requirements.
During this process, the metal undergoes a transformation that makes it stronger and more durable. The heat causes the metal to soften, and the forging pressure aligns the grain structure, which significantly enhances its mechanical properties.
How Hot Forging Enhances Metal Strength
One of the primary reasons heat forging is used in metalworking is its ability to enhance the strength of the material. This is achieved through several mechanisms:
Refined Grain Structure: Hot forging helps refine the grain structure of the metal. The repetitive deformation of the metal causes the grains to become smaller and more uniform. This uniformity results in improved strength, toughness, and resistance to cracking.
Elimination of Internal Defects: The heat and pressure involved in the heat forging process help eliminate internal defects such as porosity, voids, or cracks. This is particularly important for ensuring the final product has the required strength for demanding applications.
Improved Material Flow: The heat applied during the forging process allows the metal to flow more easily, filling every cavity of the mold without the risk of air pockets or incomplete filling. This results in a more consistent part that performs better under stress.
Enhanced Homogeneity: Since the metal is deformed while it’s still hot, hot forging helps in achieving better homogeneity in the material. The uniformity in composition and microstructure makes the forged part more reliable, especially in high-stress environments.
The Benefits of Hot Forging for Durability
Durability is a key requirement for many industrial applications, and hot forging plays an essential role in achieving long-lasting products. Some of the primary durability benefits include:
Improved Fatigue Resistance: Hot forged parts generally exhibit better fatigue resistance than those made using other methods, such as casting or machining. The grain structure produced in the heat forging process is more resistant to crack propagation, making it less likely to fail under cyclic loading.
Enhanced Toughness: The malleability of the metal during the forging process allows it to absorb energy more effectively, improving its toughness. This makes the part less likely to break or fracture under impact or high stress.
Resistance to Wear: The refining of the grain structure during hot forging results in a smoother surface and reduced friction, which can enhance wear resistance. This is particularly beneficial for parts that will be subjected to abrasive forces over time.
Consistent Material Properties: The hot forging process ensures that the material’s properties are consistent throughout the part. This eliminates weak spots that could potentially fail in harsh operating conditions.
Hot Forging vs. Other Forging Techniques
Hot forging is just one of several forging techniques used in metalworking. To understand its advantages, let’s compare it briefly to other forging methods:
Forging Method | Temperature Range | Benefits | Drawbacks |
---|---|---|---|
Hot Forging | Above recrystallization temperature (typically 900–1,300°C) | Improved grain structure, enhanced strength and toughness, better material flow | Requires more energy, parts may require additional finishing |
Cold Forging | Below recrystallization temperature (room temperature) | High dimensional accuracy, lower energy consumption | Increased tool wear, limited material options |
Warm Forging | Between room and recrystallization temperatures (300–900°C) | Balance of strength and precision, less energy than hot forging | Less malleable than hot forging, may require preheating |
Isothermal Forging | Maintains constant temperature throughout process | Highly accurate, minimal distortion | Complex setup, higher cost |
As the table shows, heat forging offers significant benefits in terms of strength and toughness, especially for high-stress applications. However, it does require more energy compared to cold or warm forging.
Applications of Hot Forging in Various Industries
Hot forging is used across a wide range of industries due to its ability to enhance the mechanical properties of metals. Below are some key applications:
- Automotive Industry: Hot forging is commonly used to manufacture engine components, suspension parts, and gears that need to withstand high levels of stress and fatigue.
- Aerospace: Hot forged components like turbine blades, landing gear, and structural parts require excellent strength-to-weight ratios and high durability.
- Oil and Gas: Components like drill pipes, valve bodies, and connectors must endure extreme pressure and temperature conditions, which is where hot forging excels.
- Heavy Machinery: High-stress parts such as crankshafts, axles, and gears benefit from the strength and toughness imparted by heat forging.
The versatility of hot forging makes it suitable for creating complex, high-strength components in various sectors.
Common Metals Used in Hot Forging
Hot forging can be applied to a wide variety of metals, each with its own unique properties. Common metals used in heat forging include:
- Carbon Steel: Known for its strength and hardness, carbon steel is widely used in heat forging, particularly for industrial machinery.
- Alloy Steel: Adding alloying elements like chromium, molybdenum, or nickel to steel enhances its hardness and resistance to corrosion, making it ideal for forging.
- Titanium: Though more difficult to forge, titanium’s light weight and excellent strength-to-weight ratio make it valuable in aerospace and high-performance applications.
- Aluminum: Hot forging aluminum is commonly used for lightweight components in automotive and aerospace industries.
- Copper and Brass: These metals are forged for electrical components, heat exchangers, and plumbing fixtures due to their excellent thermal and electrical conductivity.
Conclusion
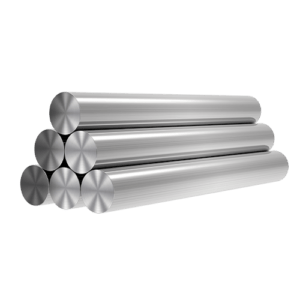
Hot forging is an essential process for producing strong, durable, and high-performance metal parts. By refining the grain structure, improving material flow, and eliminating internal defects, heat forging significantly enhances the strength and durability of metals. The benefits are especially evident in industries like aerospace, automotive, and heavy machinery, where component reliability is critical. Whether you’re producing small, intricate parts or large, load-bearing components, hot forging offers significant advantages over other manufacturing techniques.
Frequently Asked Questions (FAQ)
What is the difference between hot and cold forging?
The primary difference lies in the temperature at which the metal is forged. Hot forging occurs above the recrystallization temperature, making the metal more malleable, while cold forging is done at or near room temperature, offering better precision but requiring higher forces.
What metals are best suited for hot forging?
Metals such as carbon steel, alloy steel, titanium, aluminum, and copper are commonly used for hot forging, as they offer good strength and can withstand the high temperatures involved in the process.
Can hot forging be used for complex shapes?
Yes, hot forging can produce complex shapes, especially when combined with precision die designs. However, certain shapes may require additional machining or finishing.
Is hot forging more cost-effective than other methods?
While heat forging can be energy-intensive, it is often more cost-effective for producing large quantities of high-strength parts, especially when compared to more intricate