Shandong Qilu lndustrial Co.,Ltd.
How Custom Forgings Revolutionize Product Design
Introduction
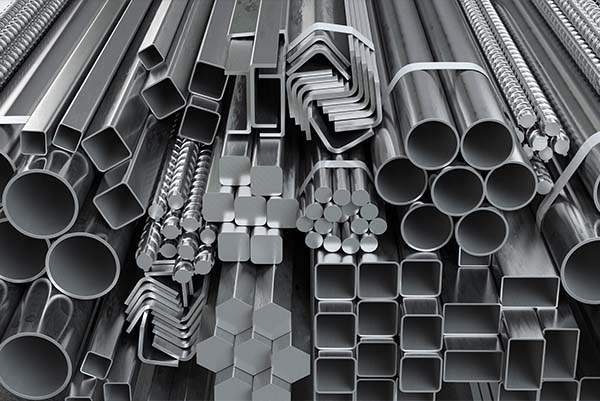
In the realm of product design and manufacturing, customization has become the cornerstone of innovation and competitiveness. Among the various techniques available, custom forgings stand out for their versatility, strength, and adaptability. This article delves into the transformative impact of custom forging on product design, exploring their benefits, applications, and future prospects.
The Basics of Custom Forgings
Custom forgings entail the process of shaping metal into desired forms through localized compressive forces. Unlike other manufacturing methods like casting or machining, forging offers unparalleled strength and durability, making it ideal for critical components in diverse industries such as aerospace, automotive, and oil & gas.
Advantages of Custom Forgings
- Strength and Durability: Custom forgings provide superior strength due to the grain structure alignment achieved during the forging process. This results in parts that can withstand high stress, fatigue, and impact loads.
- Design Flexibility: With custom forging, designers have the freedom to create intricate shapes and geometries that are otherwise difficult or impossible to achieve through traditional methods. This flexibility enables the optimization of performance and weight reduction in complex assemblies.
- Cost Efficiency: Despite the initial setup costs, custom forging offer long-term cost savings by minimizing material waste, reducing secondary machining operations, and enhancing product reliability, thus lowering maintenance and replacement expenses over the product lifecycle.
Challenges and Considerations
While custom forgings offer numerous benefits, certain challenges need to be addressed, including:
- Design Complexity: Custom forgings often cater to intricate designs that demand precision and intricacy. While this allows for unique and innovative product designs, it also introduces complexities in the manufacturing process. Sophisticated tooling and specialized equipment are often required to accurately replicate intricate designs. Additionally, precise process control becomes imperative to maintain dimensional accuracy and ensure the integrity of the final product. These factors contribute to higher initial costs associated with custom forging compared to standardized manufacturing methods.
- Material Selection: The selection of materials is a critical aspect of custom forging, as it directly influences the mechanical properties and performance characteristics of the final product. Engineers and designers must carefully consider factors such as strength, ductility, corrosion resistance, and temperature tolerance when choosing the appropriate material for a specific application. Furthermore, the availability of materials and their compatibility with the forging process must be taken into account. While a wide range of materials, including carbon steel, alloy steel, stainless steel, aluminum, titanium, and nickel alloys, are suitable for forging, each material has its unique properties and limitations, requiring thorough evaluation and testing.
- Lead Times: The custom forging process typically involves multiple stages, including design, tooling preparation, material procurement, forging, heat treatment, machining, and inspection. Each stage contributes to the overall lead time required to produce custom forging. Unlike off-the-shelf components readily available in the market, custom forging may entail longer lead times due to their tailored nature and the need for meticulous attention to detail at every step of the manufacturing process. Furthermore, factors such as design complexity, material availability, and production volume can influence lead times significantly. As a result, manufacturers and customers must engage in careful planning and coordination to manage production schedules effectively and minimize delays.
Case Studies: Custom Forgings in Action
- Aerospace Innovations: XYZ Aerospace leveraged custom forgings to develop lightweight yet robust wing components for their latest aircraft model, enhancing fuel efficiency and structural integrity simultaneously.
- Automotive Advancements: ABC Motors incorporated custom forging into their engine designs, resulting in improved power-to-weight ratios and reduced emissions, setting new benchmarks in performance and sustainability.
- Oil & Gas Solutions: DEF Energy implemented custom forging in critical downhole tools, increasing reliability and longevity in harsh drilling environments, thereby minimizing downtime and operational risks.
Applications of Custom Forgings
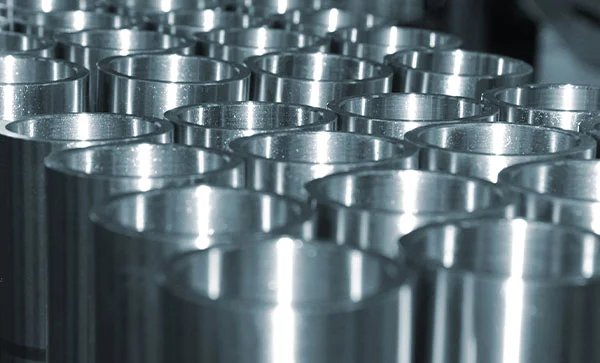
The versatility of custom forgings finds applications across various industries:
Industry | Application |
---|---|
Aerospace | Aircraft structural components, landing gear assemblies |
Automotive | Engine components, drivetrain parts, suspension systems |
Oil & Gas | Drill bits, valves, wellhead equipment |
Marine | Propulsion shafts, steering components |
Power Generation | Turbine blades, generator shafts |
Conclusion
Custom forgings represent a paradigm shift in product design, enabling engineers and designers to push the boundaries of innovation and performance. By harnessing the strengths of forging technology, industries can unlock new possibilities in efficiency, reliability, and sustainability, ensuring a competitive edge in the dynamic marketplace.
FAQ
Q:What materials can be used for custom forgings?
A:Custom forgings can be crafted from a wide range of materials, including carbon steel, alloy steel, stainless steel, aluminum, titanium, and nickel alloys, among others.
Q:How are custom forgings different from standard off-the-shelf components?
A:Custom forgings are tailored to specific design requirements, offering greater strength, durability, and design flexibility compared to standard off-the-shelf components, which are mass-produced with limited customization options.
Q:What are the typical lead times for custom forgings?
A:Lead times for custom forgings vary depending on factors such as design complexity, material availability, and production volume. However, they typically range from several weeks to a few months, including design, tooling, and manufacturing stages.