Shandong Qilu lndustrial Co.,Ltd.
Forged Metal: The Heart of Custom Fabrication
Welcome to My Blog!
Before we dive into the content, I’d love for you to join me on my social media platforms where I share more insights, engage with the community, and post updates. Here’s how you can connect with me:
Facebook:https://www.facebook.com/profile.php?id=100090903441806
Now, let’s get started on our journey together. I hope you find the content here insightful, engaging, and valuable.
Table of Contents
Introduction
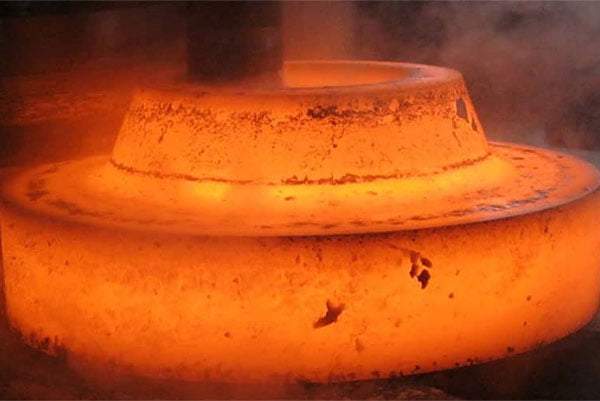
Forged metal, a testament to the power of pressure and heat, has been a cornerstone of countless industries for centuries. From the intricate components of a timepiece to the colossal structures of bridges, forged metal components offer a unique blend of strength, durability, and precision. This blog post delves into the world of metal forged, exploring its manufacturing process, its diverse applications, and the compelling reasons why it remains indispensable in the realm of custom fabrication.
Understanding the Forging Process
Forging is a metalworking technique that involves shaping a workpiece through the application of compressive forces. Unlike casting, which relies on pouring molten metal into a mold, forging begins with a heated metal blank that is systematically hammered or pressed into the desired form.
Key stages in the forging process:
- Heating: The metal blank is meticulously heated to a specific temperature to enhance its malleability.
- Shaping: The heated metal undergoes shaping through various techniques such as open-die forging, impression die forging, and closed-die forging.
- Finishing: The forged part undergoes a series of finishing operations, including machining, heat treatment, and surface finishing, to achieve the desired final product.
Advantages of Forged Metal Components
Forged metal components offer a multitude of advantages that make them highly sought-after in various industries:
- Superior strength and durability: The unique grain structure of metal forged aligns with the direction of applied forces, resulting in exceptional strength and resistance to fatigue, making it ideal for applications that demand reliability and longevity.
- Enhanced material properties: The forging process can significantly improve the mechanical properties of metals, such as tensile strength, ductility, and impact toughness, leading to components that can withstand extreme conditions.
- Complex shapes: Forging enables the creation of intricate shapes and features that are challenging to achieve through other manufacturing methods.
- Consistent quality: Forging offers excellent dimensional accuracy and repeatability, ensuring consistent quality in both small and large production runs.
Applications of Forged Metal
Forged metal components find widespread application across a diverse range of industries:
- Automotive: Crankshafts, connecting rods, gears, and axles are critical components in automotive engines and drivetrains, and metal forged ensures their durability and performance.
- Aerospace: Landing gear, turbine blades, and structural components in aircraft require exceptional strength and lightweight properties, which forged metal can deliver.
- Construction: Structural steel, bolts, and fasteners, essential for building infrastructure, rely on the strength and reliability of metal forged.
- Oil and gas: Valves, fittings, and pump components in the oil and gas industry must withstand harsh conditions and high pressures, making metal forged a preferred choice.
- Machinery: Gears, shafts, and cams, crucial components in various machinery, benefit from the precision and durability of metal forged.
The Role of Forged Metal in Custom Fabrication
Custom fabrication often demands components with unique shapes, sizes, and material properties. Forged metal offers the flexibility to create highly customized parts that precisely meet specific performance requirements.
Key benefits of using forged metal for custom fabrication:
- Tailored solutions: Forged metal components can be meticulously designed to meet the exact needs of a particular application, ensuring optimal performance.
- Reduced material waste: The forging process minimizes material waste compared to other manufacturing methods, such as machining, leading to increased efficiency and cost-effectiveness.
- Improved efficiency: The forging process can be optimized to produce components with minimal defects, reducing the need for rework and increasing overall efficiency.
Comparison of Forging Processes
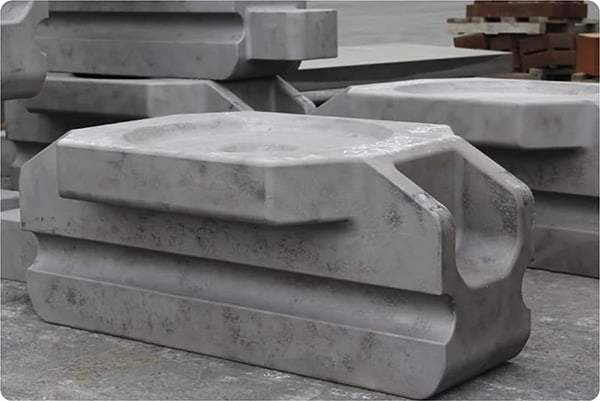
Forging Process | Description | Advantages | Disadvantages |
---|---|---|---|
Open-die forging | A simple shaping process that involves using hammers or presses to shape metal between two flat dies. | Versatile, low tooling cost | Limited shape complexity |
Impression die forging | A more precise process that involves shaping metal between two dies with specific impressions. | Precise dimensions, complex shapes | Higher tooling cost |
Closed-die forging | A highly controlled process that involves forging metal in a completely enclosed die cavity. | Excellent dimensional accuracy, repeatability | High tooling cost, limited part size |
Conclusion
Forged metal remains an indispensable material in manufacturing, owing to its exceptional strength, durability, and versatility. By understanding the intricacies of the forging process and its myriad benefits, engineers and designers can make informed decisions when selecting materials for custom fabrication projects. As technology continues to evolve, we can anticipate even more innovative applications of forged metal in the years to come.
FAQ
What is the most common material used in forging?
Steel is the most common material used in forging due to its high strength and versatility.
What are the different types of forging processes?
The primary types of forging processes include open-die forging, impression die forging, and closed-die forging.
What are the advantages of using forged metal components?
Forged metal components offer superior strength, durability, and resistance to fatigue, making them ideal for critical applications.
Can forged metal components be customized?
Yes, forged metal components can be highly customized to meet specific design requirements.
What industries commonly use forged metal components?
Forged metal components are widely used in various industries, including automotive, aerospace, construction, oil and gas, and machinery.