Shandong Qilu lndustrial Co.,Ltd.
Exploring the Versatility of Hot Forged Components
Introduction
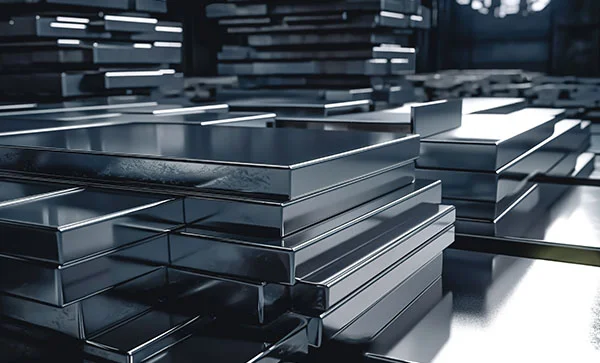
Hot forged components play a crucial role in various industries due to their exceptional strength, durability, and versatility. In this blog, we will delve into the fascinating world of hot forged components, exploring their applications, advantages, manufacturing process, and more.
Understanding Hot Forged Components
Hot forging is a manufacturing process that involves shaping metal using localized compressive forces while it is in a heated state. This process results in robust and precisely shaped components that exhibit superior mechanical properties compared to those produced by other methods.
Applications of Hot Forged Components
Hot forged components find applications across a wide range of industries, including automotive, aerospace, construction, and manufacturing. Their high strength-to-weight ratio makes them ideal for critical applications where reliability and performance are paramount.
Advantages of Hot Forging
- Enhanced Strength: Hot forged components exhibit higher strength and toughness compared to components produced by other methods.
- Improved Grain Structure: The controlled heating and shaping process during hot forging result in a fine-grained microstructure, enhancing mechanical properties.
- Complex Geometries: Hot forging allows for the production of complex shapes with minimal machining requirements, reducing material waste.
- Cost-Effectiveness: Despite the initial investment in tooling and equipment, hot forging often proves to be cost-effective due to its high production rates and material savings.
Manufacturing Process
The hot forging process typically involves several stages, including heating, deformation, and finishing. Here’s a brief overview:
- Heating: The raw material, usually a metal billet or ingot, is heated to a temperature above its recrystallization point to facilitate deformation.
- Deformation: The heated material is placed in a die cavity and subjected to compressive forces using a hydraulic press or hammer, shaping it into the desired form.
- Finishing: After forging, the components may undergo additional processes such as trimming, machining, and heat treatment to achieve the desired dimensions and properties.
Advancements in Hot Forging Technology
Recent advancements in hot forging technology have further expanded the capabilities of this manufacturing process. These include:
- Computer-Aided Design (CAD): CAD software allows for the design of intricate forging dies, optimizing material flow and reducing defects.
- Simulation Tools: Finite element analysis (FEA) and computational fluid dynamics (CFD) simulations enable engineers to predict and optimize the forging process, reducing trial and error.
- Hybrid Forging Processes: Combining hot forging with other processes such as cold forging or additive manufacturing opens up new possibilities for complex component manufacturing.
Case Studies: Applications in Real-world Scenarios
To illustrate the versatility of hot forged components, let’s explore some real-world case studies:
Automotive Industry
Hot forged components such as crankshafts, connecting rods, and gears are widely used in automotive engines due to their high strength and fatigue resistance.
Aerospace Sector
Critical aerospace components like landing gear components, turbine disks, and structural fittings are often hot forged to meet stringent performance requirements.
Oil and Gas Exploration
Hot forged components play a vital role in oil and gas exploration equipment, with applications in drilling tools, valves, and wellhead components.
Materials commonly used in hot forging:
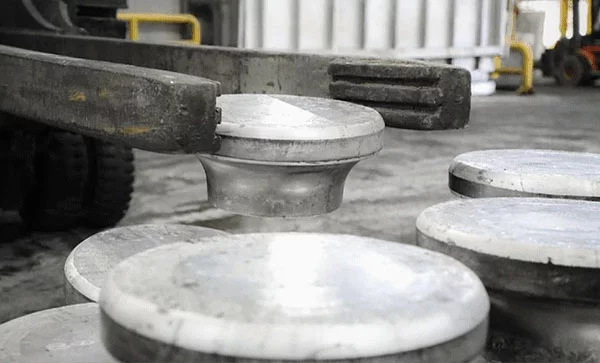
Material | Description |
---|---|
Carbon Steel | Offers high strength and toughness at an affordable cost. |
Alloy Steel | Contains additional alloying elements for enhanced properties such as corrosion resistance and wear resistance. |
Stainless Steel | Provides excellent corrosion resistance and is suitable for applications requiring hygiene and durability. |
Aluminum | Lightweight with good corrosion resistance, ideal for applications where weight reduction is critical. |
Conclusion
Hot forged components represent a cornerstone of modern manufacturing, offering unparalleled strength, durability, and versatility across various industries. As technology continues to advance, we can expect hot forging to remain a key process for producing critical components with exceptional performance characteristics.
In conclusion, the exploration of hot forged components underscores their significance in driving innovation and progress in engineering and manufacturing.
FAQ
Q: What materials are commonly used in hot forging?
A: Common materials for hot forging include carbon steel, alloy steel, stainless steel, and aluminum.
Q: What are the limitations of hot forging?
A: Hot forging may not be suitable for all materials and geometries, and the initial tooling costs can be significant for small production runs.
Q: How does hot forging compare to other manufacturing processes?
A: Hot forging offers advantages in terms of strength, material utilization, and production rates compared to processes like casting and machining.