Shandong Qilu lndustrial Co.,Ltd.
Exploring the Top Technologies Used in a Leading Forged Shaft Factory
Introduction
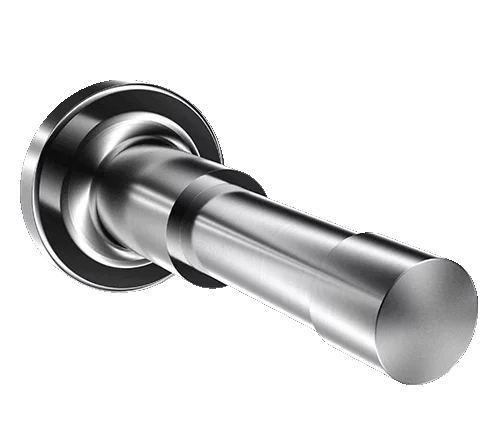
Forged shafts are essential components in various industries, including automotive, aerospace, and heavy machinery, known for their superior strength, durability, and resistance to fatigue failure. A leading forged shaft factory relies on advanced technologies to ensure precision manufacturing and meet stringent quality standards. This blog delves into the key technologies and processes employed in such factories, highlighting their importance and impact on industry applications.
Importance of Forged Shaft Manufacturing
Forged shafts are critical for transmitting power and motion in machinery and equipment. Their forged nature, typically from alloy steel, stainless steel, or carbon steel, ensures they can withstand high loads, harsh environments, and extended service life without failure. This reliability makes them indispensable in critical applications where safety and performance are paramount.
Advanced Machinery and Equipment
Modern forged shaft factories invest significantly in state-of-the-art machinery and equipment to enhance production capabilities and maintain competitive advantages:
- Hydraulic Presses: These presses are crucial for the hot forging process, where raw material (billet) is heated to a plastic state and shaped under high pressure into the desired shaft form. Hydraulic presses provide precise control over forging parameters such as temperature, pressure, and speed, ensuring consistent quality and dimensional accuracy.
- CNC Machining Centers: After forging, shafts undergo machining operations to achieve precise tolerances and surface finishes. CNC machining centers enable automated machining processes, including turning, milling, and grinding, which are essential for producing shafts with complex geometries and critical dimensions.
- Induction Heating Systems: Induction heating is used to heat the billet uniformly before forging. This technology allows for precise temperature control and rapid heating rates, minimizing thermal gradients and ensuring uniform material properties throughout the shaft. Proper heating is crucial to achieving optimal metallurgical characteristics, such as improved grain structure and mechanical strength.
Materials and Metallurgical Expertise
The choice of materials and metallurgical processes are critical in forged shaft manufacturing to meet specific performance requirements:
- Alloy Steel: Known for its high strength, toughness, and wear resistance, alloy steel is commonly used for forging shafts in heavy-duty applications where mechanical properties are critical.
- Stainless Steel: Stainless steel shafts offer excellent corrosion resistance and are ideal for applications exposed to harsh environments or corrosive substances.
- Carbon Steel: Carbon steel shafts are cost-effective and offer good machinability, making them suitable for applications requiring moderate strength and durability.
Metallurgical expertise ensures that the selected material properties are optimized through processes such as heat treatment (quenching and tempering) and surface hardening (induction hardening), enhancing shaft performance and longevity.
Quality Control and Testing
Maintaining stringent quality control measures is essential to ensure the reliability and performance of forged shafts:
- Non-Destructive Testing (NDT): Techniques such as ultrasonic testing (UT), magnetic particle inspection (MPI), and dye penetrant testing (PT) are employed to detect surface and subsurface defects without compromising the integrity of the shaft.
- Dimensional Inspection: Advanced metrology tools, including coordinate measuring machines (CMMs) and optical measurement systems, verify dimensional accuracy and adherence to design specifications.
Automation and Robotics
Automation plays a crucial role in optimizing production efficiency and consistency:
- Robotic Arms: Automated robotic arms are used for material handling, forging operations, and post-forging processes such as machining and inspection. They enhance productivity by performing repetitive tasks with high precision and repeatability.
- Automated Inspection Systems: Integrated into production lines, automated inspection systems utilize sensors and imaging technologies to monitor quality parameters continuously. These systems provide real-time feedback, enabling prompt adjustments and ensuring consistent product quality.
Environmental and Safety Measures
Leading forged shaft factories prioritize environmental sustainability and workplace safety:
- Energy Efficiency: Implementing energy-efficient technologies, such as regenerative hydraulic systems and LED lighting, reduces energy consumption and lowers carbon emissions.
- Safety Protocols: Strict adherence to occupational health and safety standards, including ergonomic workstations, personal protective equipment (PPE), and safety training programs, ensures a safe working environment for employees.
Comparison of Materials Used in Forged Shaft Manufacturing
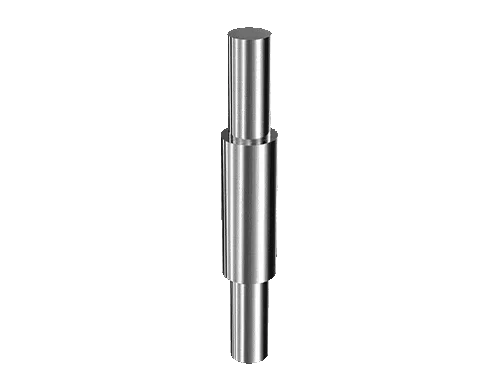
Material Type | Advantages | Disadvantages |
---|---|---|
Alloy Steel | High strength, toughness, wear resistance | Higher cost than carbon steel |
Stainless Steel | Corrosion resistance | Lower impact resistance |
Carbon Steel | Cost-effective, good machinability | Prone to corrosion in some environments |
Conclusion
The technologies employed in a leading forged shaft factory underscore its commitment to innovation, quality assurance, and operational excellence. By leveraging advanced machinery, metallurgical expertise, automation, and stringent quality control measures, these factories meet the exacting demands of diverse industries while ensuring the reliability and performance of forged shafts.
FAQ
Q: What are forged shafts used for?
A:Forged shafts are essential components used in machinery and equipment across various industries to transmit power and motion efficiently, ensuring reliable operation under demanding conditions.
Q: How are forged shafts manufactured?
A:Forged shafts are manufactured through a process of heating raw material (billet) to a plastic state, shaping it under high pressure using hydraulic presses, and then machining it to achieve precise dimensions and surface finishes.
Q: What technologies improve the quality of forged shafts?
A:Technologies such as CNC machining, induction heating, non-destructive testing (NDT), and automated inspection systems significantly enhance the quality, reliability, and performance of forged shafts.