Shandong Qilu lndustrial Co.,Ltd.
Exploring the Evolution of Steel Pipe Flange Designs
Introduction
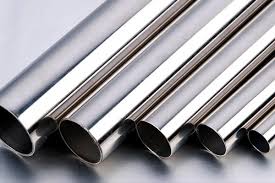
Steel pipe flanges have evolved significantly over time, serving as crucial components in piping systems across various industries. From their early utilitarian forms to today’s sophisticated designs, steel pipe flanges have adapted to meet changing industrial demands and technological advancements. This blog delves into the historical evolution, modern innovations, applications, and considerations surrounding steel pipe flange designs.
Historical Overview of Steel Pipe Flanges
The history of steel pipe flanges dates back to the Industrial Revolution, where they emerged as essential connectors in steam engines and early boiler systems. Initially, flanges were simple, flat rings welded or bolted to pipes to facilitate assembly and disassembly. As industrial processes advanced, the need for stronger, more durable flanges became apparent. Innovations in metallurgy led to the development of carbon steel flanges, which provided better strength and corrosion resistance compared to earlier iron counterparts.
Modern Steel Pipe Flange Designs
In the 20th and 21st centuries, steel pipe flange designs underwent significant advancements driven by the demands of high-pressure applications and diverse operational environments. Modern flanges are engineered with various configurations such as weld neck, slip-on, socket weld, lap joint, and blind flanges, each tailored to specific requirements. These designs incorporate features like raised faces, serrated finishes, and precision machined sealing surfaces to ensure optimal performance and reliability in critical industries such as oil and gas, chemical processing, and water distribution.
Key Innovations in Steel Pipe Flange Technology
- Metallurgical Advancements: The introduction of stainless steel and alloy steel flanges revolutionized the industry by offering superior corrosion resistance and strength properties. Duplex stainless steels, in particular, have become popular for their exceptional resistance to chloride stress corrosion cracking.
- Sealing Technologies: Gasket materials and sealing techniques have evolved to enhance flange integrity and prevent leakage under extreme pressures and temperatures. Innovations include the use of graphite, PTFE (polytetrafluoroethylene), and spiral wound gaskets tailored to specific operational conditions.
- Standardization: International standards such as ANSI (American National Standards Institute), ASME (American Society of Mechanical Engineers), and DIN (Deutsches Institut für Normung) play a crucial role in ensuring interoperability and reliability across global supply chains. Standardized dimensions, pressure ratings, and material specifications facilitate seamless integration of flange components in diverse industrial applications.
- Advanced Manufacturing Processes: Precision machining techniques enabled by CNC (Computer Numerical Control) technology and robotic welding ensure consistency and accuracy in flange manufacturing. These advancements reduce production lead times and enhance product quality, meeting stringent industry standards and regulatory requirements.
- Digitalization and IoT Integration: Emerging trends in digitalization and Internet of Things (IoT) technologies are transforming the monitoring and maintenance of flange systems. Smart flange solutions equipped with sensors and predictive analytics capabilities enable proactive maintenance, minimizing downtime and enhancing operational efficiency.
Case Studies and Applications
To illustrate the versatility and practical applications of modern steel pipe flanges:
- Oil and Gas Industry: Offshore platforms require robust flange solutions capable of withstanding high pressures, corrosive environments, and temperature fluctuations. Weld neck and blind flanges are commonly used to ensure secure connections in offshore piping systems.
- Chemical Processing: Flanges used in chemical plants must resist chemical reactions and maintain integrity under varying temperatures. Alloy steel flanges with specialized coatings or linings are deployed to mitigate corrosion and ensure long-term reliability.
- Water and Wastewater Treatment: Municipal water distribution networks rely on durable flange solutions to maintain water quality and operational efficiency. Slip-on and socket weld flanges are preferred for their ease of installation and reliability in critical infrastructure projects.
Steel Pipe Flange Design Considerations
When selecting steel pipe flanges for specific applications, several critical factors must be considered:
- Pressure and Temperature Ratings: Flanges must be rated to withstand the operating pressures and temperatures encountered in the application environment.
- Material Compatibility: Compatibility with the fluid conveyed and surrounding environment (e.g., corrosive chemicals, seawater) is essential to prevent degradation and ensure long-term performance.
- Sealing Performance: Effective sealing mechanisms, including gaskets and sealing surfaces, are crucial to prevent leaks and maintain system integrity under varying conditions.
- Regulatory Compliance: Adherence to international standards and local regulations ensures flanges meet safety, quality, and environmental requirements, reducing risks associated with non-compliance.
Common Types of Steel Pipe Flanges and Their Applications
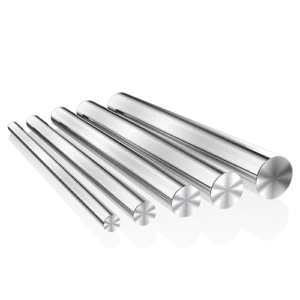
Flange Type | Description | Applications |
---|---|---|
Weld Neck | Features a tapered hub for welding to the pipe, providing strong and durable connections. | Oil and gas pipelines, high-pressure applications. |
Slip-On | Slips over the pipe and is then welded in place, facilitating quick assembly and disassembly. | Chemical processing, water treatment facilities. |
Socket Weld | Has a recessed area around the pipe for welding, ideal for smaller diameter pipes and high pressure systems. | Steam systems, hydraulic and pneumatic systems. |
Lap Joint | Consists of two parts: a stub end that is welded to the pipe and a loose backing flange. | Low-pressure applications, where alignment flexibility is needed. |
Blind | Solid plate used to block off a pipeline or vessel opening, typically used in testing or maintenance procedures. | Pressure vessels, shutdown and isolation applications. |
Conclusion
The evolution of steel pipe flange designs reflects advancements in materials science, manufacturing technologies, and engineering practices. From their humble origins in steam engines to their pivotal role in modern industrial infrastructure, steel pipe flanges continue to evolve to meet the demands of diverse applications worldwide.
FAQ
Q:What is the purpose of a steel pipe flange?
A:Steel pipe flanges serve as connectors to join pipes, valves, and equipment components in a piping system. They facilitate easy assembly, disassembly, and maintenance operations.
Q:What are the different types of steel pipe flanges?
A:Common types include weld neck, slip-on, socket weld, lap joint, threaded, and blind flanges. Each type is designed for specific applications based on pressure, temperature, and alignment requirements.
Q:How are steel pipe flanges installed?
A:Installation methods vary depending on the type of flange and piping system configuration. Typically, flanges are bolted or welded to pipes using nuts, bolts, or welding techniques to ensure a secure and leak-free connection.
Q:What materials are used to manufacture steel pipe flanges?
A:Steel pipe flanges are predominantly made from carbon steel, stainless steel, alloy steel, and specialty alloys like Inconel and Monel. Material selection depends on factors such as mechanical properties, corrosion resistance, and environmental conditions.