Shandong Qilu lndustrial Co.,Ltd.
Cold Forging Process vs. Hot Forging: Key Differences
Welcome to My Blog!
Before we dive into the content, I’d love for you to join me on my social media platforms where I share more insights, engage with the community, and post updates. Here’s how you can connect with me:
Facebook:https://www.facebook.com/profile.php?id=100090903441806
Now, let’s get started on our journey together. I hope you find the content here insightful, engaging, and valuable.
Introduction
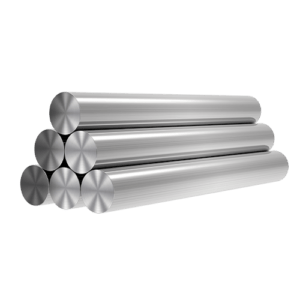
Forging is a crucial manufacturing technique that shapes metal into desired forms. Among the various methods, the cold forging process and hot forging stand out as two dominant techniques. While they share the same goal—creating strong, precise components—their methodologies, applications, and outcomes differ significantly. In this article, we’ll explore the cold forging technique, its comparison with hot forging, and the key differences to help you make informed decisions for your manufacturing needs.
What Is the Cold Forging Process?
The cold forging technique involves shaping metal at or near room temperature. Unlike hot forging, where metals are heated to high temperatures, cold forging depends on the material’s ductility to achieve the desired shape.
Key attributes of the cold forging process include:
- No heating required: Reduces energy consumption.
- High dimensional accuracy: Produces precise parts with minimal finishing required.
- Increased strength: Work hardening during the process enhances material strength.
Examples of parts commonly manufactured using the cold forging process include bolts, screws, and rivets.
What Is Hot Forging?
Hot forging requires heating the metal above its recrystallization temperature, making it malleable and easier to shape.
Key attributes of hot forging include:
- Higher malleability: Allows shaping of metals that are hard to deform.
- Reduced work hardening: Minimizes stress on tools and equipment.
- Enhanced ductility: Suitable for complex shapes.
Applications of hot forging include automotive parts, industrial machinery, and heavy-duty components.
Cold Forging Process vs. Hot Forging: Key Differences
Criteria | Cold Forging Process | Hot Forging |
---|---|---|
Temperature | Room temperature or slightly elevated | High temperature above recrystallization |
Energy Efficiency | Low energy consumption | High energy due to heating requirements |
Dimensional Accuracy | High precision, minimal finishing needed | Moderate, requires finishing |
Material Strength | Strengthened through work hardening | Retains ductility, lower work hardening |
Tool Wear | Higher due to material hardness | Lower, as metals are more malleable |
Cost | Lower operational costs | Higher due to energy and maintenance |
Application | Simple shapes and mass production | Complex and large components |
Advantages of the Cold Forging Process
The cold forging technique offers several advantages that make it appealing for various industries:
Cost Efficiency: The absence of heating reduces energy costs.
Material Utilization: Minimizes waste, ensuring efficient use of raw materials.
Improved Surface Finish: Produces smooth surfaces that require little or no post-processing.
Environmental Benefits: Lower energy use results in a reduced carbon footprint.
Enhanced Strength: Work hardening increases the durability and wear resistance of components.
Limitations of the Cold Forging Process
Despite its benefits, the cold forging technique has certain limitations:
- Material Restrictions: Not all metals are suitable for cold forging. Metals must be ductile and malleable.
- Design Constraints: Complex shapes are harder to achieve.
- Tooling Costs: Requires high-strength tools that can withstand greater forces.
Factors to Consider When Choosing Between Cold and Hot Forging
When deciding between the cold forging technique and hot forging, consider the following:
Material Type:
- Use cold forging for softer, more ductile materials like aluminum and low-carbon steel.
- Choose hot forging for harder metals like titanium and alloys.
Desired Shape and Size:
- Opt for hot forging for intricate designs.
- Use cold forging for simple, mass-produced components.
Budget and Resources:
- Cold forging requires lower operational costs.
- Hot forging demands higher energy inputs but supports a wider range of materials.
Industries Leveraging the Cold Forging Process
Several industries rely on the cold forging process for its efficiency and precision:
- Automotive: Manufacturing fasteners, gear blanks, and axles.
- Aerospace: Producing lightweight, durable components.
- Electronics: Creating connectors and precision screws.
- Construction: Producing nails, bolts, and other fasteners.
Conclusion
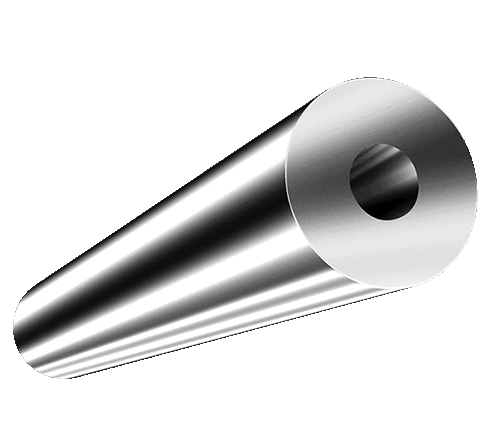
Understanding the key differences between the cold forging process and hot forging is essential for optimizing manufacturing outcomes. The cold forging technique excels in cost efficiency, material utilization, and precision, making it ideal for mass production of simpler shapes. On the other hand, hot forging remains indispensable for shaping complex, high-strength components.
Choosing the right forging method depends on your material, design requirements, and budget constraints. By considering these factors, you can achieve the desired quality and performance for your products.
FAQ
What materials are best suited for the cold forging process?
Soft and ductile metals such as aluminum, brass, and low-carbon steel are ideal for the cold forging process.
Is the cold forging process more eco-friendly than hot forging?
Yes, the cold forging process consumes less energy, resulting in a lower carbon footprint.
Can cold forging achieve complex shapes?
Cold forging is better suited for simpler shapes due to the higher force required to deform the metal.
Which industries benefit most from the cold forging process?
Industries like automotive, aerospace, electronics, and construction frequently use the cold forging process for its precision and cost-effectiveness.
How does tool wear differ in cold and hot forging?
Cold forging causes greater tool wear because the metal’s hardness remains unchanged, while hot forging experiences lower tool wear due to the material’s increased malleability.
What is work hardening in the cold forging process?
Work hardening occurs when the metal’s strength increases due to plastic deformation, a common effect in the cold forging process.