Shandong Qilu lndustrial Co.,Ltd.
Benefits of Using Hollow Metal Tubes
Welcome to My Blog!
Before we dive into the content, I’d love for you to join me on my social media platforms where I share more insights, engage with the community, and post updates. Here’s how you can connect with me:
Facebook:https://www.facebook.com/profile.php?id=100090063158454
Now, let’s get started on our journey together. I hope you find the content here insightful, engaging, and valuable.
Introduction
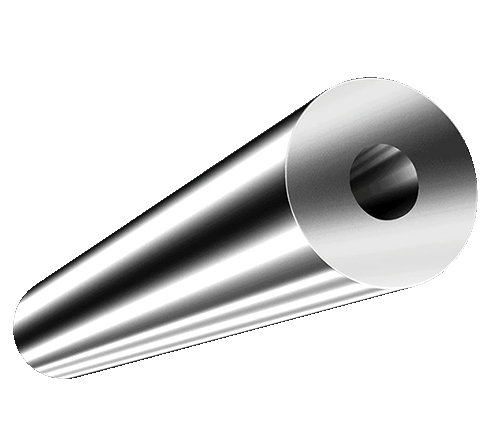
Hollow metal tubes have emerged as a cornerstone in various industries, revolutionizing design and engineering practices. Their unique blend of strength, versatility, and weight efficiency has made them indispensable in numerous applications. This blog post delves deep into the advantages of using hollow tubes, exploring their diverse applications, remarkable properties, and comparative benefits over solid metal counterparts.
The Versatility of Hollow Metal Tubes
The versatility of hollow metal tubes is truly astounding, extending across a wide spectrum of industries. From the towering structures of modern cities to the intricate components of high-performance vehicles, these tubes have proven their adaptability.
- Construction: In the construction industry, hollow tubes serve as the backbone of structural frameworks, supporting the weight of buildings, bridges, and towers. Their exceptional strength-to-weight ratio allows for lighter and more efficient designs, reducing material costs and construction time.
- Automotive: The automotive industry leverages hollow metal tubes to create lightweight yet robust components such as frames, chassis, and suspension systems. This optimization of weight distribution enhances fuel efficiency and vehicle performance.
- Furniture: The design world embraces hollow tubes for their sleek aesthetics and durability. They are used to craft stylish and functional furniture pieces, from minimalist chairs to sturdy shelving units.
- Industrial Machinery: In industrial settings, hollow metal tubes are employed to construct machinery components that require high strength and resistance to wear and tear. Their hollow structure allows for efficient internal routing of fluids and electrical cables.
The Strength-to-Weight Ratio: A Competitive Edge
One of the most compelling advantages of hollow metal tubes is their exceptional strength-to-weight ratio. This means that hollow tubes can deliver equivalent strength to solid tubes, while significantly reducing weight. This characteristic offers numerous benefits:
- Reduced Material Costs: By using less material to achieve the same strength, hollow tubes can lead to substantial cost savings.
- Improved Energy Efficiency: Lighter structures and components require less energy to transport and operate, contributing to reduced environmental impact.
- Enhanced Performance: In applications where weight is critical, such as aerospace and automotive, hollow metal tubes can improve performance metrics like fuel efficiency and payload capacity.
Corrosion Resistance: A Durable Solution
Many hollow metal tubes are manufactured from materials renowned for their corrosion resistance, such as stainless steel and aluminum. This makes them ideal for use in harsh environments where exposure to moisture, chemicals, and extreme temperatures is a concern.
- Marine Applications: In marine environments, hollow tubes withstand the corrosive effects of saltwater, ensuring the longevity of boats, ships, and offshore structures.
- Chemical Processing: In chemical processing plants, hollow metal tubes resist the corrosive nature of chemicals, preventing equipment failure and maintaining operational efficiency.
Cost-Effectiveness: A Balanced Approach
While the initial cost of hollow metal tubes may be slightly higher than that of solid metal tubes, the long-term savings can be substantial. The reduced weight and improved efficiency of hollow tubes can lead to lower transportation costs, reduced energy consumption during manufacturing, and extended service life.
Easy Fabrication: Tailored Solutions
Hollow metal tubes are relatively easy to fabricate using a variety of techniques, including welding, bending, and cutting. This flexibility allows for the creation of custom shapes and sizes, catering to specific design requirements.
Comparison of Hollow and Solid Metal Tubes
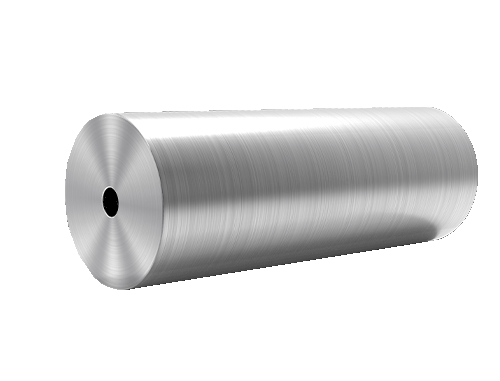
Feature | Hollow Metal Tubes | Solid Metal Tubes |
---|---|---|
Strength-to-weight ratio | High | Low |
Cost-effectiveness | Generally higher initial cost but lower long-term cost | Lower initial cost but higher long-term cost |
Corrosion resistance | High in many cases | Varies depending on material |
Versatility | High | Moderate |
Fabrication ease | High | Moderate |
Conclusion
Hollow metal tubes have solidified their position as a versatile and efficient solution across numerous industries. Their exceptional strength-to-weight ratio, corrosion resistance, cost-effectiveness, and ease of fabrication make them a compelling choice for engineers and designers seeking to optimize their projects. By understanding the multifaceted benefits of hollow tubes, professionals can unlock innovative possibilities and achieve greater success in their endeavors.
FAQ
What are the most common materials used for hollow metal tubes?
Stainless steel, aluminum, and carbon steel are the most commonly used materials for hollow metal tubes. These materials offer a balance of strength, weight, and corrosion resistance, making them suitable for various applications.
How are hollow tubes manufactured?
Hollow tubes are primarily manufactured through two principal methods: extrusion and welding.
Extrusion: In this process, a solid metal billet is forced through a die to form a hollow tube.
Welding: Two metal sheets are rolled into cylindrical shapes and then welded together to create a seamless or welded tube.
What are some of the limitations of using hollow metal tubes?
While hollow metal tubes offer numerous advantages, they may be susceptible to certain limitations:
Buckling: Under compressive loads, hollow tubes may be prone to buckling, especially if the tube’s wall thickness is insufficient. Careful design considerations are necessary to mitigate this risk.
Impact Resistance: In applications involving high-impact loads, hollow tubes may have lower impact resistance compared to solid tubes. However, advancements in material science and manufacturing techniques are addressing this limitation.