Shandong Qilu lndustrial Co.,Ltd.
Benefits of Rolled Ring Forging: A Comprehensive Guide
Welcome to My Blog!
Before we dive into the content, I’d love for you to join me on my social media platforms where I share more insights, engage with the community, and post updates. Here’s how you can connect with me:
Facebook:https://www.facebook.com/profile.php?id=100090903441806
Now, let’s get started on our journey together. I hope you find the content here insightful, engaging, and valuable.
Introduction
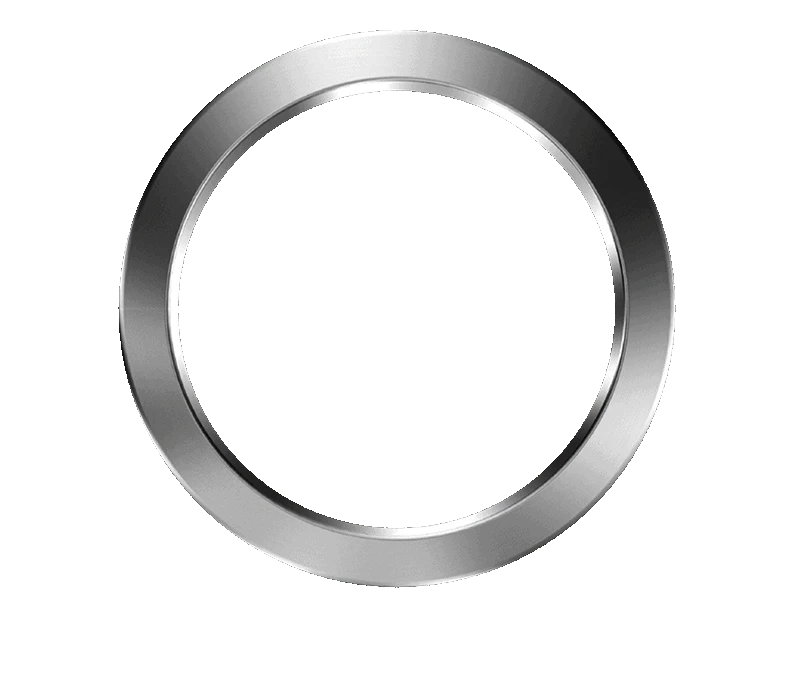
Rolled ring forging is a highly efficient metalworking process that produces near-net-shape cylindrical components with exceptional mechanical properties. This process involves heating a metal billet and then rolling it into a ring shape, gradually increasing the diameter and reducing the wall thickness. The resulting rings possess a fine grain structure, high strength-to-weight ratio, and excellent dimensional accuracy. In this article, we will delve into the numerous benefits of rolled ring forging, making it a preferred choice for various industries.
Understanding Rolled Ring Forging
Before exploring the benefits, let’s briefly understand the rolled ring forging process. It involves several steps, including:
- Billet Preparation: A cylindrical metal billet is prepared with the desired dimensions.
- Heating: The billet is heated to a specific temperature to improve its plasticity.
- Rolling: The heated billet is passed through a series of rolls to form a ring shape.
- Cooling: The formed ring is cooled gradually to achieve the desired properties.
Key Benefits of Rolled Ring Forging
Superior Mechanical Properties
- High Strength: The controlled deformation during the rolling process results in a fine-grained microstructure, enhancing the overall strength and durability of the ring.
- Excellent Ductility: Rolled rings exhibit excellent ductility, allowing them to withstand significant deformation without fracturing.
- Improved Fatigue Resistance: The uniform grain structure and absence of defects contribute to superior fatigue resistance, making rolled rings ideal for applications subjected to cyclic loading.
Dimensional Accuracy and Consistency
- Tight Tolerances: Rolled rings can be produced with extremely tight tolerances, reducing the need for subsequent machining operations.
- Consistent Quality: The controlled process ensures consistent quality and minimizes variations between components.
Material Efficiency
- Near-Net-Shape: The process produces near-net-shape components, minimizing material waste and reducing machining costs.
- Cost-Effective: The high material utilization and reduced machining time contribute to overall cost-effectiveness.
Versatility
- Wide Range of Materials: Rolled ring forging can be applied to a variety of materials, including carbon steel, alloy steel, stainless steel, and non-ferrous metals.
- Complex Geometries: The process can produce rings with complex geometries, such as tapered walls, flanges, and integral features.
Comparison of Rolled Ring Forging with Other Manufacturing Processes
Feature | Rolled Ring Forging | Alternative Processes |
---|---|---|
Material Efficiency | High | Moderate to low |
Dimensional Accuracy | Excellent | Good to moderate |
Mechanical Properties | Superior | Good to excellent |
Complexity of Shapes | High | Moderate |
Cost-Effectiveness | High | Moderate |
Advanced Techniques in Rolled Ring Forging
To further enhance the capabilities of rolled ring forging, several advanced techniques are employed:
- Induction Heating: Precisely controlled heating of the billet using induction coils improves energy efficiency and reduces oxidation.
- Precision Rolling: Advanced rolling mills and tooling enable the production of rings with extremely tight tolerances and complex geometries.
- Computer-Aided Design (CAD) and Computer-Aided Manufacturing (CAM): CAD/CAM systems are used to optimize the design and manufacturing process, leading to improved efficiency and product quality.
Quality Control and Testing
Rigorous quality control measures are essential to ensure the integrity and performance of rolled rings. Common testing methods include:
- Dimensional Inspection: Verifying the dimensions and tolerances of the rings using precision measuring instruments.
- Metallurgical Analysis: Assessing the microstructure, chemical composition, and mechanical properties of the material.
- Non-Destructive Testing (NDT): Employing techniques like ultrasonic testing, magnetic particle inspection, and eddy current testing to detect internal flaws and defects.
- Mechanical Testing: Conducting tensile tests, hardness tests, and impact tests to evaluate the mechanical properties of the rings.
Environmental Impact of Rolled Ring Forging
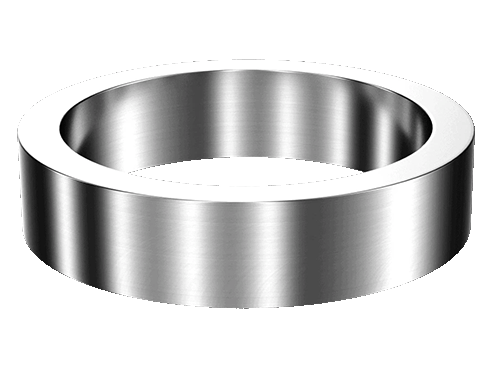
The environmental impact of rolled ring forging can be minimized through various measures:
- Energy Efficiency: Implementing energy-efficient practices, such as optimizing heating processes and reducing idle time.
- Material Conservation: Maximizing material utilization and minimizing waste generation.
- Pollution Control: Adopting pollution control measures to reduce emissions and wastewater discharge.
- Recycling and Reuse: Recycling scrap metal and reusing process water to conserve resources.
Conclusion
Rolled ring forging is a versatile and efficient manufacturing process that offers numerous advantages. By understanding its benefits and applications, engineers and manufacturers can leverage this technology to produce high-quality, cost-effective components for a wide range of industries.
FAQ
What are the key factors affecting the quality of rolled rings?
The quality of rolled rings is influenced by factors such as billet quality, heating temperature, rolling parameters, cooling rate, and post-processing operations.
How can I optimize the design of a rolled ring component?
Consulting with experienced engineers and utilizing advanced design tools can help optimize the design of rolled ring components, considering factors like material selection, geometry, and loading conditions.
What are the common challenges in rolled ring forging?
Common challenges include controlling the temperature distribution, preventing defects like cracks and folds, and achieving precise dimensional tolerances.
How can I improve the productivity of rolled ring forging?
Improving productivity can be achieved by optimizing the process parameters, reducing downtime, and implementing advanced automation techniques.
What is the future of rolled ring forging?
The future of rolled ring forging is promising, with advancements in materials, processing techniques, and automation leading to further improvements in quality, efficiency, and sustainability.