Shandong Qilu lndustrial Co.,Ltd.
Benefits of Forging the Shaft in Manufacturing Processes
Introduction
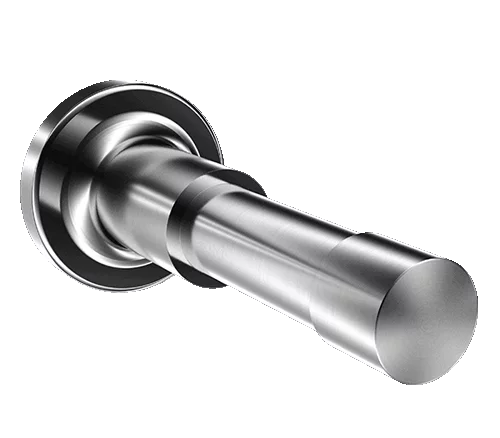
In modern manufacturing, the process of forging the shaft stands as a cornerstone of efficient production. This article delves into the numerous advantages that forging offers over alternative methods, emphasizing its impact on material strength, durability, and cost-effectiveness.
Understanding Forging the Shaft
Forging involves shaping metal through compressive forces, typically with hammers or presses. Forging the shaft specifically refines the material’s grain structure, aligning it along the shape of the shaft. This alignment enhances the mechanical properties of the shaft, resulting in superior strength, toughness, and resistance to fatigue and impact stresses compared to materials processed through casting or machining methods.
Key Advantages of Forging the Shaft
- Enhanced Strength and Durability Forging the shaft significantly enhances its strength by improving the material’s grain structure. The controlled deformation during forging aligns the grain along the contours of the shaft, eliminating weak spots and ensuring uniform mechanical properties throughout. This results in shafts that can withstand higher stresses and loads, making them ideal for critical applications where reliability is paramount.
- Improved Material Utilization Unlike machining processes that often generate significant waste, forging optimizes material use. By shaping the metal under high pressure, forging minimizes material waste and achieves better material integrity. This efficiency not only reduces costs associated with raw materials but also lowers environmental impact by decreasing scrap and energy consumption.
- Precision and Consistency Forged shafts offer precise dimensional control and consistency in mechanical properties. The forging process allows for tight tolerances and uniformity in shape and size, ensuring compatibility and ease of assembly in complex machinery and equipment. This level of precision translates into reliable performance and reduced downtime in industrial operations.
- Versatility in Design One of the key advantages of forging is its versatility in producing complex shapes and customized designs. Forged shafts can be tailored to meet specific engineering requirements, including unique geometries and intricate features that are challenging to achieve with other manufacturing methods. This flexibility makes forging suitable for a wide range of applications across industries such as automotive, aerospace, marine, and heavy machinery.
- Economic Benefits While the initial costs of forging equipment and tooling may be higher than other methods, the long-term economic benefits are significant. The durability and longevity of forged shafts reduce maintenance costs and downtime, leading to overall cost savings throughout the lifespan of the component. Moreover, the superior mechanical properties of forged shafts contribute to enhanced operational efficiency and reliability, further optimizing return on investment.
Applications of Forged Shafts
Forged shafts find extensive application in critical components where strength, durability, and reliability are essential. Industries such as automotive rely on forged shafts for crankshafts and transmission components, while aerospace and power generation sectors utilize them in turbine shafts and rotor assemblies. The versatility of forged shafts extends to various machinery and equipment requiring robust performance under demanding conditions.
Environmental Impact and Sustainability
Forging offers environmental advantages over machining due to reduced material waste and energy consumption. The efficiency in material utilization and minimal scrap generation aligns with sustainable manufacturing practices, contributing to lower carbon footprints and resource conservation in industrial operations.
Industry-specific benefits of forged shafts.
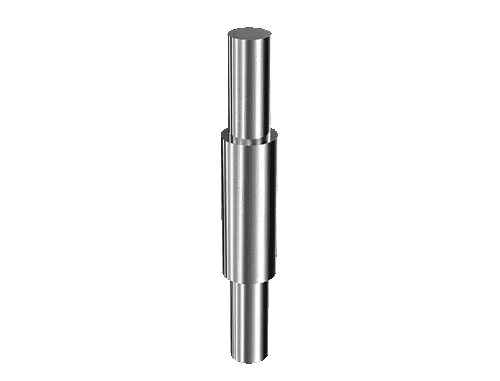
Industry Application | Forged Shaft Benefits |
---|---|
Automotive | Improved torsional strength for crankshafts, enhancing engine performance and durability. |
Aerospace | High fatigue resistance and dimensional stability crucial for turbine and rotor shafts. |
Oil and Gas | Enhanced corrosion resistance and reliability in drill string components under extreme conditions. |
Heavy Machinery | Superior load-bearing capacity and wear resistance in gears and transmission shafts. |
Power Generation | Consistent mechanical properties ensure reliability in turbine generator shafts for continuous operation. |
Conclusion
In conclusion, the benefits of forging the shaft in manufacturing processes are compelling across various dimensions—from superior mechanical properties and enhanced durability to economic efficiency and environmental sustainability. As industries continue to demand high-performance solutions, forging remains a preferred method for producing shafts that meet stringent quality standards and deliver reliable performance under challenging conditions.
FAQ
Q: How to improve the strength of forging the shaft?
A: Forging the shaft can produce complex shapes and custom designs, resulting in superior mechanical properties such as increased strength and resistance to fatigue.
Q: What are the cost benefits of forging compared to machining?
A: Forging typically reduces production costs due to minimal material waste and lower lifetime maintenance expenses.
Q: Can forged shafts be customized for specific applications?
A: Yes, forging allows for the production of complex shapes and custom designs, making it suitable for a wide range of industrial needs.