Shandong Qilu lndustrial Co.,Ltd.
Benefits of Cold Forging in Manufacturing Processes
Welcome to My Blog!
Before we dive into the content, I’d love for you to join me on my social media platforms where I share more insights, engage with the community, and post updates. Here’s how you can connect with me:
Facebook:https://www.facebook.com/profile.php?id=100090903441806
Now, let’s get started on our journey together. I hope you find the content here insightful, engaging, and valuable.
Introduction

Cold forging is a pivotal manufacturing process that offers numerous advantages over traditional methods. By shaping metal at room temperature, this technique enhances the mechanical properties of materials while minimizing waste and production costs. In this blog, we will delve into the key benefits of cold forge, its applications, and why it has become a preferred choice in modern manufacturing.
What is Cold Forging?
Cold forging involves the process of deforming metal at ambient temperatures to produce specific shapes and sizes. This method is typically used for creating parts such as fasteners, connectors, and various automotive components. The process is characterized by high precision and minimal material waste, making it an efficient manufacturing technique.
Advantages of Cold Forging
Improved Mechanical Properties
One of the primary benefits of cold forge is the enhancement of the material’s mechanical properties. The process induces strain hardening, which increases the strength and durability of the metal. As a result, components produced through cold forge often exhibit superior performance under stress.
Reduced Waste
Cold forging is known for its ability to minimize waste. Unlike other methods, which may involve cutting or machining excess material, cold forging shapes metal without significant waste generation. This not only reduces material costs but also contributes to a more sustainable manufacturing process.
High Dimensional Accuracy
Cold forging offers exceptional dimensional accuracy, allowing for tighter tolerances compared to many other manufacturing methods. This precision is essential in industries where exact specifications are critical, such as aerospace and automotive.
Enhanced Surface Finish
The cold forging process typically results in a better surface finish. The compressive forces involved in forging can eliminate the need for extensive post-processing, saving time and resources. Components often require less machining, further reducing costs.
Cost Efficiency
While the initial setup for cold forge can be higher than for some other methods, the long-term savings are significant. The reduction in material waste, lower energy consumption, and decreased need for machining all contribute to overall cost efficiency.
Increased Production Rates
Cold forging processes are capable of producing large quantities of components quickly. The automation of the cold forge process allows manufacturers to achieve higher production rates without sacrificing quality. This efficiency is vital in meeting market demands.
Versatility in Applications
Cold forging is suitable for a wide range of materials, including steel, aluminum, and brass. This versatility makes it applicable across various industries, from automotive and aerospace to electronics and medical devices.
Table of Cold Forging Benefits
Benefit | Description | Impact on Manufacturing |
---|---|---|
Improved Mechanical Properties | Increased strength and durability | Enhanced performance under stress |
Reduced Waste | Minimal material loss during production | Lower material costs and sustainability |
High Dimensional Accuracy | Tight tolerances and precise dimensions | Essential for critical applications |
Enhanced Surface Finish | Better surface quality with less post-processing | Time and cost savings |
Cost Efficiency | Long-term savings through reduced waste and energy | Competitive advantage in pricing |
Increased Production Rates | High output capacity and efficiency | Ability to meet high demand |
Versatility in Applications | Usable with various materials and industries | Broad applicability across sectors |
Applications of Cold Forging
Automotive Industry
Cold forging plays a crucial role in the automotive sector, where high-strength components are required. Parts such as gears, axles, and fasteners benefit from the improved mechanical properties achieved through cold forge.
Aerospace Sector
In aerospace, the demand for lightweight yet strong materials is paramount. Cold-forged components are ideal for this industry, providing the necessary strength-to-weight ratio while adhering to strict safety standards.
Electronics Manufacturing
The electronics industry utilizes cold forge for producing connectors, terminals, and other small components. The high precision and surface finish are critical in ensuring the reliability of electronic devices.
Medical Devices
In the medical field, cold forge is employed to manufacture surgical instruments and implantable devices. The enhanced strength and accuracy of cold-forged components are vital for patient safety and device efficacy.
Evaluating Cold Forging Manufacturers
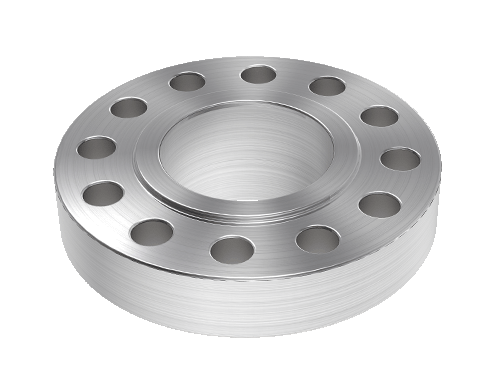
Key Factors to Consider
When selecting a cold forging manufacturer, consider the following factors:
- Experience and Expertise: Look for manufacturers with a proven track record in cold forging and relevant industry experience.
- Quality Assurance: Ensure the manufacturer has stringent quality control processes in place to guarantee the integrity of the components produced.
- Technology and Equipment: Modern equipment and technology can significantly affect the efficiency and quality of the cold forge process.
- Customization Capabilities: Verify if the manufacturer can accommodate custom designs and specifications to meet your unique requirements.
Questions to Ask Potential Manufacturers
- What types of materials do you work with?
- Can you provide references or case studies from previous clients?
- What is your typical lead time for production?
- How do you ensure quality control throughout the manufacturing process?
Conclusion
Cold forging is a transformative manufacturing process that offers a multitude of benefits, including improved mechanical properties, reduced waste, and cost efficiency. Its versatility makes it applicable across various industries, and its ability to produce high-quality components quickly is a significant advantage in today’s fast-paced market. By understanding the benefits and applications of cold forging, manufacturers can make informed decisions that enhance their production processes.
FAQ
What materials can be used in cold forging?
Cold forging can be performed on a variety of materials, including steel, aluminum, brass, and other alloys, making it a versatile option for many applications.
How does cold forge compare to hot forging?
Cold forge takes place at room temperature, leading to strain hardening, while hot forging occurs at elevated temperatures, which can reduce material strength. Each method has its advantages depending on the application.
What are the typical applications of cold forged components?
Cold forged components are commonly used in the automotive, aerospace, electronics, and medical device industries due to their strength, precision, and reliability.
Can cold forging be automated?
Yes, cold forging processes can be highly automated, which increases production rates and efficiency while maintaining high quality and consistency.
What are the initial costs associated with cold forging?
While the initial setup costs for cold forging can be higher than other methods, the long-term savings from reduced material waste and lower processing costs often outweigh these initial investments.