Shandong Qilu lndustrial Co.,Ltd.
Application of Forging Steel: A Comprehensive Guide
Welcome to My Blog!
Before we dive into the content, I’d love for you to join me on my social media platforms where I share more insights, engage with the community, and post updates. Here’s how you can connect with me:
Facebook:https://www.facebook.com/profile.php?id=100090903441806
Now, let’s get started on our journey together. I hope you find the content here insightful, engaging, and valuable.
Table of Contents
Introduction
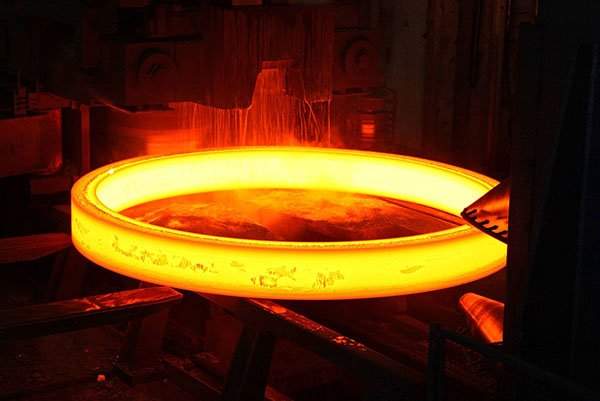
Forging steel, a material shaped through intense pressure and heat, stands as a cornerstone in countless industries. Its remarkable properties – unparalleled strength, unwavering durability, and an inherent resistance to wear and tear – make it the go-to choice for applications demanding unwavering reliability and robust performance. This in-depth guide will delve into the multifaceted world of forging steel, exploring its defining characteristics, the intricate forging processes, and its indispensable role across a diverse array of sectors. We will examine how its unique qualities enable it to excel in demanding environments, from the heart of the automotive industry to the cutting edge of aerospace engineering.
Understanding Forging Steel
What is Forging Steel?
Forging steel transcends the ordinary. It’s born from a process that involves subjecting a heated workpiece to immense compressive forces, a process that fundamentally transforms its internal structure. This transformative journey refines the steel’s grain structure, resulting in a material with significantly enhanced mechanical properties. The precise characteristics of forged steel can be meticulously tailored by carefully selecting the alloying elements and meticulously controlling the forging process itself.
Key Characteristics of Forging Steel:
- Unmatched Strength: Forging steel boasts exceptional tensile strength and yield strength, making it an ideal candidate for applications where the ability to withstand immense loads is paramount. Its robust internal structure provides an unwavering foundation for demanding structural integrity.
- Enduring Durability: The dense and homogenous microstructure of forging steel endows it with exceptional resistance to wear and tear. This inherent durability ensures that components crafted from forging steel can withstand the relentless demands of continuous operation and resist the gradual degradation that can plague lesser materials.
- Exceptional Toughness: Forging steel possesses a remarkable capacity to absorb sudden impacts and withstand significant vibrations without succumbing to fracture. This toughness makes it an invaluable asset in applications where unpredictable forces are encountered, ensuring the continued reliability and safety of critical components.
- Versatility Without Limits: The remarkable versatility of forged steel stems from the ability to manipulate its properties through the judicious selection of alloying elements and the precise control of the forging process itself. This adaptability allows engineers to tailor the material to meet the specific demands of any application, from the most mundane to the most demanding.
Applications of Forging Steel
Forging steel permeates a wide array of industries, serving as the backbone of countless critical components.
- Automotive: The automotive industry relies heavily on forging steel to produce essential components such as crankshafts, connecting rods, gears, and axles. These components operate under immense stress and require exceptional strength and durability to ensure optimal engine performance and vehicle safety.
- Aerospace: In the demanding realm of aerospace engineering, forging steel plays a vital role in the construction of critical components such as landing gear, turbine blades, and structural elements within aircraft. The ability to withstand extreme temperatures, resist fatigue, and maintain structural integrity under immense loads is paramount in this industry, and forging steel consistently delivers.
- Construction: The construction industry utilizes forging steel for essential structural components, including robust beams, columns, and connectors. The material’s exceptional strength and unwavering reliability make it an indispensable asset for building structures that must withstand the test of time and the unpredictable forces of nature.
- Energy: In the energy sector, forging steel finds applications in the production of turbine shafts, valves, and fittings. The material’s inherent resistance to corrosion and its ability to withstand high temperatures make it an ideal choice for components operating in harsh environments and exposed to extreme conditions.
- Machinery: The manufacturing of diverse machinery relies heavily on forging steel for the production of essential components such as gears, shafts, and bearings. The precision and durability of forging steel ensure optimal performance and longevity, minimizing downtime and maximizing productivity.
Forging Process
The forging process itself is a testament to the transformative power of pressure and heat. The journey begins with the heating of the workpiece to a specific temperature, a crucial step that renders the material more malleable and amenable to shaping. The subsequent shaping process involves the application of compressive forces, skillfully manipulating the material into the desired form.
- Open-die Forging: This versatile method employs two flat dies to shape the workpiece, offering flexibility and adaptability for a wide range of applications.
- Impression Die Forging: This method utilizes intricately crafted dies with precisely shaped cavities that mirror the final desired shape of the workpiece. This approach enables the creation of highly complex shapes with exceptional precision.
- Upsetting: This process focuses on increasing the cross-sectional area of the workpiece while simultaneously reducing its height. This technique is particularly useful for producing short, thick components.
- Drawing: The drawing process involves reducing the cross-sectional area of the workpiece while simultaneously increasing its length, resulting in elongated components.
Comparison of Forging Methods
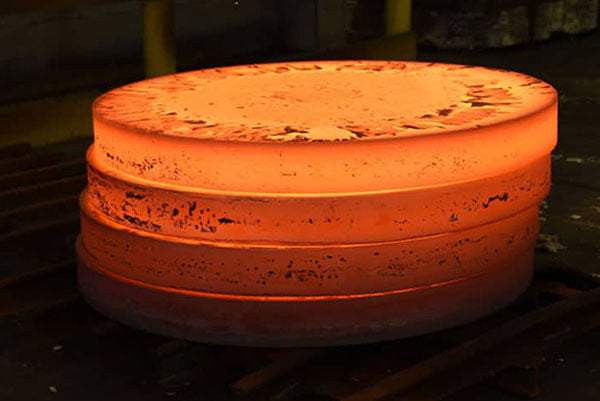
Forging Method | Advantages | Disadvantages | Applications |
---|---|---|---|
Open-die forging | Versatility, simple tooling | Less precise, limited complexity | Large forgings, rough shaping |
Impression die forging | High precision, complex shapes | Higher tooling costs, limited material flow | Mass production of complex parts |
Upsetting | Increases cross-sectional area, simple tooling | Can cause flash formation | Producing short, thick parts |
Drawing | Reduces cross-sectional area, improves surface finish | Can cause cracking, requires lubrication | Producing long, thin parts |
Conclusion
Forging steel stands as a testament to the remarkable capabilities of human ingenuity and the transformative power of advanced manufacturing processes. Its unique blend of exceptional strength, unwavering durability, and inherent versatility makes it an indispensable material across a vast array of industries. From the intricate components that power modern vehicles to the robust structures that shape our world, forging steel plays a pivotal role in driving progress and shaping the future. As technology continues to evolve, we can expect even more innovative applications of forging steel, pushing the boundaries of what is possible and unlocking new frontiers of engineering excellence.
FAQ
What is the difference between forging and casting?
Forging involves shaping metal through pressure and heat, while casting involves pouring molten metal into a mold. Forging generally results in a stronger and more refined grain structure.
How is the strength of forging steel determined?
The strength of forging steel is primarily determined by its chemical composition (alloying elements), the forging process itself, and subsequent heat treatment. Tensile strength and yield strength are common metrics used to measure its strength.
What are some common alloying elements used in forging steel?
Common alloying elements include carbon, chromium, nickel, molybdenum, and vanadium. These elements enhance properties like strength, toughness, and wear resistance.