Shandong Qilu lndustrial Co.,Ltd.
Advantages of Metal Forging in Manufacturing Today
Welcome to My Blog!
Before we dive into the content, I’d love for you to join me on my social media platforms where I share more insights, engage with the community, and post updates. Here’s how you can connect with me:
Facebook:https://www.facebook.com/profile.php?id=100090903441806
Now, let’s get started on our journey together. I hope you find the content here insightful, engaging, and valuable.
Introduction
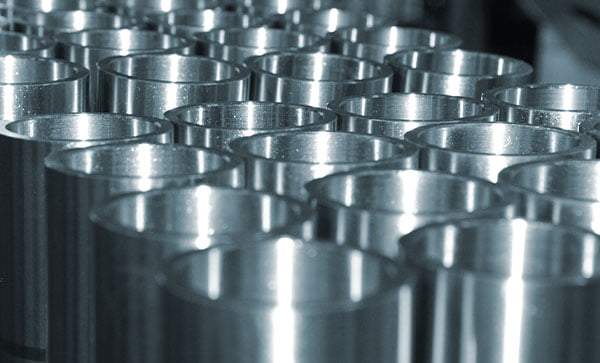
Metal forging is a vital manufacturing process that transforms metal into desired shapes through the application of compressive forces. This technique has been around for centuries and has evolved significantly, becoming integral in various industries today. With its ability to enhance the properties of metals and improve product performance, metal forging has emerged as a preferred choice for manufacturers seeking durability, precision, and cost-effectiveness. In this blog, we will explore the numerous advantages of forged metal, providing insights into its applications, processes, and the reasons it continues to thrive in modern manufacturing.
What is Metal Forging?
Understanding the Metal Forging Process
Forged metal involves shaping metal using localized compressive forces. This can be done through various methods, including:
- Open-die forging: Metal is shaped between two flat dies.
- Closed-die forging: Metal is pressed into a die cavity, allowing for more intricate shapes.
- Ring forging: Specifically used for creating ring-shaped components.
These methods enhance the mechanical properties of the metal, making it stronger and more durable. The process typically involves heating the metal to a plastic state before applying force, which allows for easier shaping.
Common Materials Used in Metal Forging
Several types of metals can be forged, including:
- Steel: Known for its strength and versatility.
- Aluminum: Lightweight and corrosion-resistant.
- Titanium: Offers excellent strength-to-weight ratio.
- Copper: Good electrical and thermal conductivity.
Choosing the right material for forged metal depends on the intended application and desired properties.
Key Advantages of Metal Forging
Enhanced Mechanical Properties
One of the primary advantages of metal forging is its ability to improve the mechanical properties of metals. The forging process refines the grain structure of the material, resulting in:
- Increased strength
- Improved toughness
- Higher fatigue resistance
These enhancements are crucial for components subjected to high-stress conditions, such as those found in automotive and aerospace applications.
Cost-Effectiveness in Production
Metal forging can significantly reduce production costs, especially for large-scale manufacturing. Some of the cost benefits include:
- Reduced Material Waste: Forging often results in less scrap material compared to other manufacturing methods.
- Fewer Processing Steps: The ability to create complex shapes reduces the need for additional machining operations.
- Increased Production Speed: Forging can be performed quickly, allowing for higher output rates.
These factors combined make forged metal a financially viable option for manufacturers.
Superior Surface Finish and Dimensional Accuracy
Metal forging often results in components with excellent surface finishes and tight tolerances. The controlled nature of the process allows manufacturers to achieve:
- Consistent dimensions: Ensuring parts fit perfectly in assembly processes.
- Reduced need for secondary operations: Less machining is required, which saves time and resources.
This accuracy is particularly beneficial in industries where precision is paramount, such as medical devices and high-performance automotive parts.
Applications of Metal Forging
Industries Utilizing Metal Forging
Forged metal is prevalent in a variety of industries, including:
Industry | Common Applications |
---|---|
Aerospace | Engine components, landing gear |
Automotive | Crankshafts, connecting rods |
Oil and Gas | Valves, fittings, and pump components |
Construction | Structural components, tools |
Defense | Firearms, armored vehicle parts |
These applications demonstrate the versatility and importance of forged metal across different sectors.
Innovations in Metal Forging Technology
Recent advancements in technology have further enhanced the metal forging process. Innovations such as:
- Computer-Aided Design (CAD): Streamlining the design process for complex components.
- Automation and Robotics: Increasing efficiency and precision in production.
- Additive Manufacturing: Integrating 3D printing techniques with traditional forging for hybrid solutions.
These technologies not only improve the forging process but also expand its possibilities.
Challenges in Metal Forging
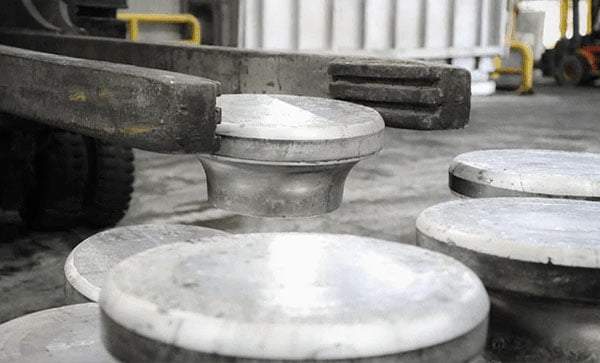
Addressing Common Challenges in Metal Forging
While forged metal has many advantages, there are challenges that manufacturers must consider:
- Initial Setup Costs: High tooling costs can be a barrier for small-scale production.
- Material Limitations: Not all metals are suitable for forging; some may be too brittle or difficult to shape.
- Skill Requirements: Skilled operators are necessary to ensure quality and safety during the forging process.
Addressing these challenges is essential for manufacturers to maximize the benefits of metal forging.
Conclusion
Metal forging remains a cornerstone of modern manufacturing, offering numerous advantages such as enhanced mechanical properties, cost-effectiveness, and precision. As industries continue to evolve, the demand for high-quality, durable components will only increase, solidifying the role of metal forging in various applications. With ongoing technological advancements and a commitment to overcoming challenges, metal forging is set to thrive in the manufacturing landscape for years to come.
FAQ
What is the difference between forging and casting?
Forging involves shaping metal through compressive forces, while casting involves pouring molten metal into a mold. Forging generally results in stronger and more durable parts compared to casting.
Can any metal be forged?
While many metals can be forged, not all materials are suitable. Metals like steel, aluminum, and titanium are commonly used due to their desirable properties when forged.
What are the primary benefits of closed-die forging?
Closed-die forging offers high precision and better surface finish due to the die’s shape. It is ideal for producing complex shapes with tight tolerances.
How does forged metal impact environmental sustainability?
Forged metal is often more sustainable than other manufacturing processes, as it generates less waste and requires less energy compared to methods like casting.
Is metal forging suitable for small-scale production?
While metal forging is most cost-effective for large-scale production, small-scale operations can benefit from it if the right tooling and processes are employed.